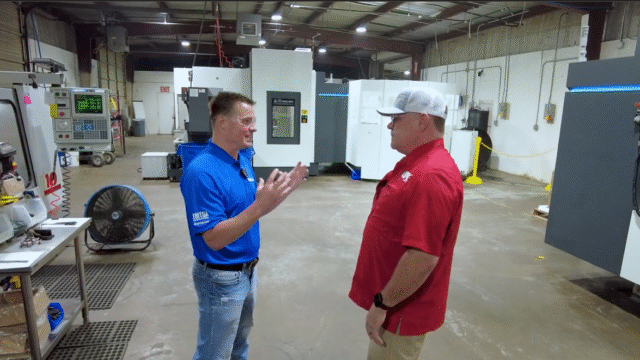
Who knew automation could thrive in the middle of nowhere?!
Tucked away in rural Texas, OX Manufacturing is doing something incredible—running parts unmanned for up to…
Investing in punch press tooling for your machine is a significant expenditure, but it’s a necessary one. As with any major purchase, you want to ensure you’re getting the most value out of your investment. For punch press tooling, this means striving for the maximum number of hits possible over the tool’s lifespan. Proper regrinding and maintenance practices are essential for achieving this goal and avoiding issues associated with tool wear, such as unexpected replacement costs, diminished product quality, and costly machine downtime.
Why Regrind Tools?
Maintaining sharp tools through regular regrinding is crucial for extending tool life and maximizing the number of hits. Sharp tools not only produce higher quality and quantity of holes but also wear much more slowly compared to dull ones. Contrary to intuition, sharpening tools more frequently has been found to enhance tool life and hole consistency. As tools begin to wear, the wear rate accelerates rapidly. The more the cutting edge deteriorates, the more material must be removed during grinding to restore sharpness, ultimately shortening the tool’s lifespan.
For example, a .040-inch (1 mm) radius can develop in less than 80,000 hits, necessitating the removal of .040 inches (1 mm) of material from the tool to regain sharpness.
Dull tools not only shorten tool life but also lead to various punching problems that compromise hole quality and consistency. Dull tools require more tonnage to punch a hole, resulting in unnecessary stress on the punch press. This increased workload generates more heat at the tool tip, leading to galling and stripping issues. Excessive heat can even affect the heat treatment on the punch tip, potentially resulting in total tool failure. Additionally, dull tools behave as if they lack sufficient die clearance, causing issues like slug pulling.
When to Regrind Tools
While there’s no strict rule for how often tools should be regrinded, a general guideline is to sharpen them frequently enough so that no more than .010 inches (.25 mm) of material needs to be removed to completely renew the sharp edge of the punch. Typically, the die needs sharpening about half as often as the punch.
For instance, if a tool is sharpened every time a .010-inch (.25 mm) radius develops on the cutting edge, only .010 inches (.25 mm) of material is removed from the tool to restore sharpness. Since the edge of a sharp tool deteriorates more slowly, the tool lasts longer.
Three Signs Your Tool Needs Regrinding
Feel the punch for a dull cutting edge. Experts recommend sharpening tools when the cutting edges are worn to a .004-inch (0.1 mm) radius. Watch for a decline in hole quality. Dull tools increase rollover and produce excessive burrs. Listen to the punching noise. If the punch press generates more noise than usual, the tool’s cutting edge may need sharpening.
How to Regrind Tools
Regardless of the grinding machine used, the grinding wheel should be dressed to present a clean, flat surface with each use to reduce side loading, which can damage the punch assembly. Using an open, coarse, soft bond wheel, take light, frequent passes while moving horizontally on the punch or die face. Always flood the tooling with coolant while grinding to prevent heat buildup, which can weaken the punch and lead to surface cracking. Clamping punches and dies firmly in a fixture during grinding minimizes vibrations and chatter.
Check Station Alignment and Die Clearance
Proper alignment of the punch and die is essential to prevent rapid and uneven wear. Before starting a new punching job, use alignment tools to ensure both units are properly aligned. Additionally, maintaining the correct die clearance is crucial for hole quality and tool life. Too much clearance leads to slugs and burrs, while too little accelerates wear and may cause tool breakage.
Remember, properly sharpened and maintained punch press tooling performs optimally, providing high-quality parts and maximizing return on investment. Failure to maintain tooling leads to poor performance, lower-quality parts, and frequent replacements, resulting in increased costs.
Original source Fabricating & Metalworking
Stay up to date with the latest industry news and events.
Be first to see all the updates from MTDCNC
Our newsletters frequency varies dependant on content
All the latest deals from the industry feature on our newsletters