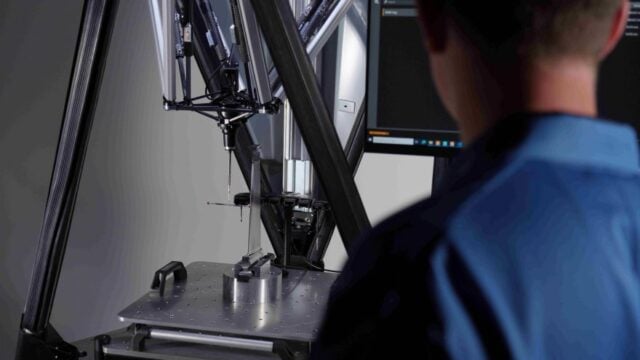
Renishaw Launches Equator–X 500: A Dual-Mode Breakthrough in Shopfloor Metrology
Renishaw, a global leader in precision measurement and manufacturing systems, has unveiled its latest innovation for…
The challenge of producing machine component assemblies with ever tighter machining tolerances at low production cost is well known. Advanced design and manufacturing techniques can help to reduce costs, but parts with tight tolerances generally have a higher cost.
Tolerance stacks occur when modules are assembled from parts that must fit together. The overall tolerance stack of an assembly of parts can be calculated by summing all individual feature tolerances. Therefore, the required dimensional precision of each part can increase proportionally as the number of parts increases in the tolerance stack.
By increasing the overall dimensional tolerances of an assembly, significant cost reductions are possible, due to easing of the tolerance requirements of each component.
Furthermore, the time taken to align and fit assemblies can be reduced with faster, well-designed installation procedures that help to minimise both associated costs and product lead times.
How can QUANTiC encoders increase profitability and reduce lead times?
Optical position encoders are used in a huge variety of machines and devices. They consist of an electro-optical readhead (sensor) and a precision graduated rotary or linear scale. The readhead measures linear position or rotation by optically sensing the regularly spaced scale markings and outputs this information as an analogue or digital signal.
Wider installation tolerances
Consider the example of an encoder installed on a rotary drive shaft. The shaft is machined to enable an interference fit with a rotary encoder ring, such as Renishaw’s RESM40, and the readhead is mounted on a bracket above the ring such that the separation (rideheight) between the scale surface and readhead is maintained to within a tolerance of ±0.1 mm. If the rideheight tolerance is doubled, the tolerances on the shaft, ring assembly and readhead mounting bracket can also be doubled, which may result in a significant time and cost saving over a long production run.
The QUANTiC encoder series combines leading-edge filtering optics and interpolation technology to create a high performance, super-compact, incremental, open optical encoder.
QUANTiC encoders feature exceptional installation tolerances and excellent dirt immunity due to an advanced photodetector design and coarser 40 µm-pitch scale. For instance, readhead installation rideheight and yaw tolerances are now ±0.2 mm and ±0.9⁰, respectively.
Faster machine calibration with less maintenance
The time taken by a skilled operator to install and calibrate multiple encoders on a machine represents a significant cost. By designing the encoder to be simple and intuitive to install and calibrate, such that a semi-skilled worker may perform this task, labour and time costs are reduced.
QUANTiC encoders feature unrivalled ease of set-up and calibration, and are supported by the Advanced Diagnostic Tool (ADT) combining both ADTi-100 hardware and ADT View software components. The ADT acquires comprehensive real-time data from the readhead to assist with quick and easy encoder installation, and in-field fault finding, potentially saving time and reducing installation and maintenance costs.
During scheduled and preventative maintenance, this off-line diagnostic tool can test key performance parameters of a QUANTiC encoder system, such as signal strength, readhead pitch and Lissajous output.
QUANTiC encoders also offer end users a lower total cost of ownership due to robust design features, such as higher dirt immunity and wider operating tolerances, which may decrease the downtime required for scheduled maintenance.
Design flexibility
Designers can specify a range of QUANTiC encoder options including resolution, signal output, scale type, reference marks and cable lengths.
One benefit of the QUANTiC encoder design is the elimination of additional bulky external interfaces, which is particularly useful for space-constrained applications. This innovative approach was first used for Renishaw’s advanced VIONiC™ encoders.
QUANTiC readheads now offer digital or analogue outputs and are compatible with linear, partial arc and rotary scales. The choice of either a digital or analogue signal output enables direct manipulation of the signal inside the controller, which may be preferred for highly dynamic applications where refined velocity and acceleration control are required.
In rotary applications, customers can choose between either taper mount (A section) RESM40 rings for high accuracy applications or thin (B section) RESM40 rings for low inertia applications. The QUANTiC rotary encoder also addresses applications with wide through-bore requirements.
Available linear scale options include RTLC40 for mounting on FASTRACK™ carrier track and self-adhesive RTLC40-S: both simplify thermal error compensation by allowing independent scale expansion relative to the substrate.
QUANTiC encoders are also compatible with RKLC-40S encoder scale, which is highly flexible and can be used in both linear and partial arc applications. RKLC is a substrate mastered linear encoder scale that is designed to adopt the thermal behaviour of an underlying high thermal-mass substrate to enable passive thermal error compensation. It features a proven, robust stainless steel tape scale design with immunity to solvents, coilability for easy storage and cut-to-length convenience.
In higher speed applications, the encoder can operate at linear speeds of up to 24 m/s and rotational axis speeds of up to 8,800 rpm (at a resolution of ≥1 µm).
Summary
QUANTiC encoders are designed to help to increase the throughput of high-volume production lines and offer potentially significant time and cost savings for OEM customers. End-users also benefit from a reduced cost of ownership because less downtime is required for servicing and maintenance.
Be first to see all the updates from MTDCNC
Our newsletters frequency varies dependant on content
All the latest deals from the industry feature on our newsletters