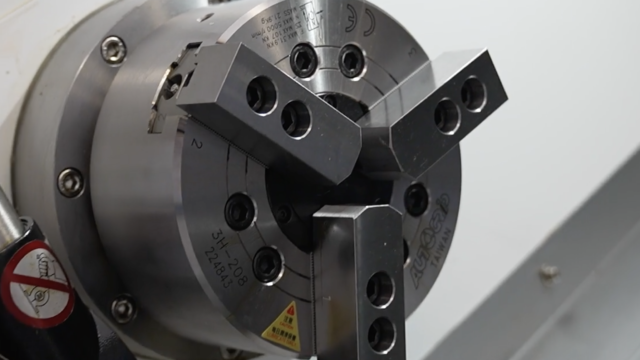
Special offer – multi axis turning
This Leadwell turning centre available from WH Lead comes with swarf extraction, toolsetting arm, parts catcher…
Established in 1988 and employing over 150 staff, family-owned Irish manufacturing firm PB Machine Tech (www.pbmachinetech.ie) produces more than 5,000 customised hydraulic cylinders per week at its factory in Bagenalstown, County Carlow. To boost production capacity, in November last year (2021) the company purchased its third Taiwanese-built Leadwell V-40iT 5-axis vertical machining centre (www.wh-lead.co.uk/machine-tools/v-40it).
Supplied by sole sales and service agent in Ireland and Britain, Towcester-based WH-Lead, the 12,000 rpm BT40 machine was required due to increasing demand for the hydraulic products from manufacturers around the world in the agricultural, access platform, construction, environmental and materials handling sectors. More than 80 percent of output from the Bagenalstown factory is exported.
Ray Kehoe, General Manager – Component Division at PB Machine Tech said, “We introduced one-hit manufacture in our factory some years ago following heavy investment in turn-mill machines. The benefits in terms of speed of production, reduced lead-time and better accuracy were immediately apparent.
“We were therefore keen to replicate this on the prismatic machining side of our business. We started that process in June 2018 by augmenting our 3-axis VMC capacity with the purchase of our first 5-axis machining centre, a Leadwell V-40iT.
“From a quality point of view, the ability to guarantee the geometry of parts is really important. Previously, we designed jigs to try to ensure good geometry, but that approach was reliant on proficient operator training and execution.
“With one-hit machining, perfect components are produced easily every time. Multiple sequential clampings on several machines are a thing of the past, as is the manufacture of expensive fixtures.”
He added that another benefit to PB Machine Tech is shorter throughput times and hence reduced work-in-progress, which allows the company to respond promptly to urgent orders. After production starts, partial deliveries of components can begin almost immediately, if necessary, to allow the hydraulic cylinder manufacturing process to keep going.
After seeing the benefits in terms of raised quality and reduced lead-times resulting from installation of the first V-40iT, its capacity was quickly filled, prompting investment in a second at the end of 2020 and now a third. Control is by a Fanuc 0i-MF Plus that, in the case of the machines supplied to Bagenalstown, is able to interpolate four CNC axes simultaneously, although full 5-axis operation may also be specified.
4+1 capability, which is more economical than full 5-axis control, is ideal for PB Machine Tech as its machining cycles are not particularly complex. A variety of rectangular blocks needs to be machined on multiple faces and a vast majority of cycles are therefore 3+2, with the rotary table and swivelling trunnion positioned and locked for XYZ machining.
Mr Kehoe provided an interesting insight into why a trunnion-type vertical machining centre was chosen rather than another configuration, such as with a swivelling B-axis spindle. In his opinion, the trunnion gives the operator a large overall usable working volume, as the XYZ axes are allowed their full traverses, in this case 846 mm, 635 mm and 488 mm respectively. This is important to the hydraulic cylinder manufacturer, as some parts require deep hole drilling at various angles and good tool clearance is vital.
The material machined on the Leadwell VMCs in cycle times ranging from 10 to 40 minutes is almost exclusively S355J2 low carbon steel in the form of sawn flat bar or oxy-fuel-cut pieces. General tolerance is ± 0.2 mm but can be as tight as 0.05 mm and batch size ranges from 10-off to around 400 pieces. Programming is mainly carried out manually offline on a PC or at the machine control, although some blocks within in a cycle, such as thread milling and high-feed milling, are generated with the aid of Autodesk Fusion 360.
As to the company’s repeated purchase of Leadwell machines from Taiwan, rather than VMCs from other, perhaps better known sources, Mr Kehoe commented, “We first became aware of this make of machine from a subcontractor using them to manufacture parts that it supplies into our hydraulic cylinder plant
“On their recommendation and from our research, we discovered that the machines are robust, reliable, spacious, capable and good value for money and our experience has certainly confirmed this. Additionally, the 200 kg table capacity means we never run into issues machining large, awkward parts.”
He added that the training and service back-up provided by WH-Lead have been excellent, including practical hands-on programming, setting and running. Notes are well written, with plenty of examples and further questions after training are promptly addressed.
His concluding remark was that PB Machine Tech is happy to recommend both Leadwell machines and WH-Lead as important partners in addressing the current economic challenges facing Irish and British manufacturers.
Be first to see all the updates from MTDCNC
Our newsletters frequency varies dependant on content
All the latest deals from the industry feature on our newsletters