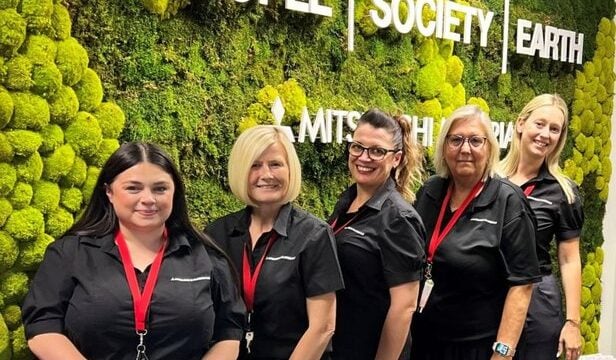
MMC Hardmetal Steps Up for Cancer Research
Team members from MMC Hardmetal UK Ltd are participating in the Shine Night Walk to support…
Mitsubishi Materials has developed three new grades of inserts dedicated to the machining of stainless steels. MC7115 for light cutting, MC7125 for general machining and MP7135 for heavy cutting applications.
When comparing stainless steels to other steels and cast irons, it has low hardness but is tough to machine and susceptible to work hardening. Due to these characteristics, turning inserts are prone to edge damage and weld chipping. Additionally, plastic deformation of the insert due to the heat generated makes stainless steel difficult to cut, resulting in unstable tool life.
The properties of stainless steels, such as corrosion and heat resistance vary greatly depending on the metallurgical structure and composition, and these small differences can make it appear is as if a completely different workpiece material is being machined.
Mitsubishi Materials has combined the coating and substrate technology to produce a series of grades to successfully machine stainless steels. The key feature of these new grades has been the simultaneous development of a new carbide substrate and a specific coating suitable for tackling the difficulties of finish, medium and rough machining of stainless steels. The three troublesome areas of notching, fracturing due to chip welding and plastic deformation all had to be combatted.
Each grade has its own unique combination of coating layers of TiN, Al203 and TiCN. However, the breakthrough needed to prevent the usual problems when machining stainless steel, was the proprietary technology that binds the layers together. Even the best coatings are ineffective if they don’t bind to each other effectively. Mitsubishi Materials have called these innovative binding layers as the Super-TOUGH GRIP for the upper coating layers and the SUB-GRIP for the base layer that binds it to the carbide substrate.
The MC/MP7100 series has a wide variety of both positive and negative rake inserts available. To complement this an effective choice of chipbreakers suited to each application can be chosen from a readily available stock. This choice enables finish machining at speeds up to Vc 255 m/min through to heavy and interrupted cutting when combining the MP7135 grade and the HM chipbreaker at depths of cut up to 10mm. Cutting tests revealed greatly extended tool life when machining 304L stainless steel and when tested on 316L stainless steel the effective tool life was almost doubled at cutting speeds of vc 150 m/min with a feed rate of 0.3 mm/rev at 1.5mm depth of cut.
Stay up to date with the latest industry news and events.
Be first to see all the updates from MTDCNC
Our newsletters frequency varies dependant on content
All the latest deals from the industry feature on our newsletters