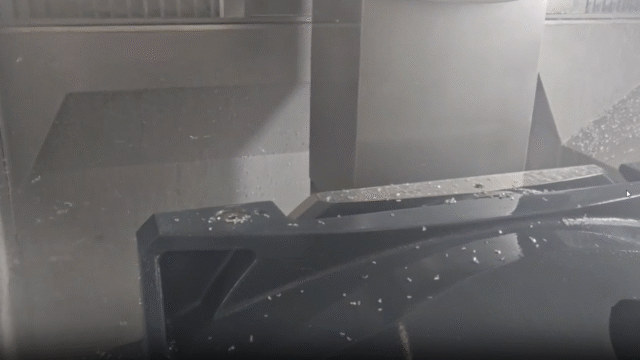
Do You Panic When You’re Machining Like This? 
That panic… you know the feeling. You’re watching the machine, hands hovering near the feed hold…
Milling, turning and CAD functions for daily CAM tasks
OPEN MIND has now launched hyperMILL® 2024, the latest version of the company’s CAD/CAM suite that now delivers new turning features and improved algorithms. With a wealth of new features, Version 2024 makes the digital process chain from CAD data through CAM programming to optimised NC code more efficient than ever before. Simplified rest machining and interaction with the machine are just a few examples of how the software has been further refined.
Existing versions of hyperMILL® already offer a broad range of functions and strategies for turning, turn/milling and mill/turning. However, the key extension in the latest version is hyperMILL® TURNING Solutions which provides extensive turret support for lathes. This also underscores OPEN MIND’s determination to push ahead with the integration of digital twins. Turning centres with one main spindle, one turret and a Siemens control system are now mapped with all tools true to the original machine with the help of hyperMILL®VIRTUAL Machining. Users can conveniently equip the turret with turret holders and tools in the Virtual Machine machining planner and use the resulting setup for NC code simulation.
Reading Back Measuring Points
Another useful application of virtual machining technology is the reading back of measuring points. This means that users can use the 3D model of a component to see at a glance which measuring points are outside the tolerance. As a result, it becomes much easier to analyse inaccuracies and tool wear after machining and then compensate for these in the CAD/CAM system. Moreover, the hyperMILL® SHOP Viewer makes this new function directly available on the machine tool.
CAD for CAM
hyperMILL® 2024 also offers various new features relating to ‘CAD for CAM.’hyperMILL® supports the import of PMI (Product Manufacturing Information) and MBD (Model-Based Definition) data in various formats such as STEP, CATIA V5, SOLIDWORKS, Creo and Siemens. Now, improved functions for surface modelling allow users to generate surfaces from a large number of grid curves. Another important CAD innovation is an improved electrode creation strategy that supports three-dimensional eroding.
5-Axis Path Correction
Comparable to the 3D radius correction to account for the tool wear or deflections, 5-axis path correction is now possible. Vectors are written to the tool contact point in the NC program to ensure precision correction on the machine control. The NC control uses the contact vectors to move the NC points by a defined adjustment value during machining.
A new algorithm for rest material detection ensures automatic complete detection of all rest material areas in both 3D and 5-axis machining. The algorithms for calculating the trajectory have also been optimised. The cutting-edge 3D strategy for machining punching tools has undergone several improvements. This includes the optimisation of collision avoidance when performing machining based on a reference job. Machining is carried out collision-free as far as this is possible for the given tool clamping length. The ‘Soft overlap’ option makes it possible to smooth the approach and retraction movements. A new algorithm also improves the toolpath calculation for 3D plane machining, resulting in even faster, more uniform machining performance.
To safeguard against long unattended machining cycles, hyperMILL® now allows tool breakage monitoring to be activated in the tool database to make it part of the machining program. This information is processed during NC generation on the virtual machine. The generated NC program includes the corresponding control macro call.
Tool Synchronisation with the Hummingbird MES
In the new version, tools from the hyperMILL® tool database can be synchronised with the Hummingbird MES at the touch of a button. This means that tools used for CAM programming are automatically transferred to the Hummingbird tool management system. All other processes such as machine setup, measuring, tracking and the use of tools in the machines are mapped in the Hummingbird MES, thus ensuring a consistent exchange of information within the company.
Strong for the Future
OPEN MIND has always been known for its pioneering CAD/CAM solution, which seamlessly combines CAD functionalities with CAM programming. Bringing these two elements closely together results in considerable time savings in workpiece processing and shows that CAM without CAD is no longer viable today. To make this even clearer, hyperMILL® will combine CAD and CAM under a single name from Version 2024 onward.
Stay up to date with the latest industry news and events.
Be first to see all the updates from MTDCNC
Our newsletters frequency varies dependant on content
All the latest deals from the industry feature on our newsletters