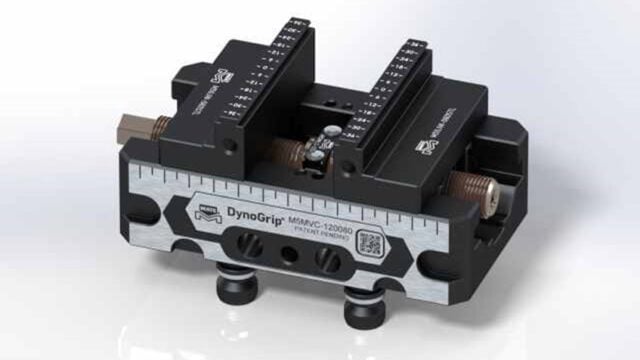
Leader extended zero-point offering with Mate Precision Technologies
Following a recent partnership agreement, the full range of Mate Precision Technologies’ high precision zero-point fixturing…
In-process gauging is an ancillary system that can measure the part while it is being ground and, in real-time, automatically control the in-feed of the grinding wheel so that every part produced by the machine is in tolerance according to the manufacturing specifications (see the picture below). It provides a 100% production validation check that can even automatically compensate for wear on the grinding wheel. Due to the harsh machining environment found in the grinding process, the gauging operation is performed with the gauge’s fingers in physical contact with the workpiece; it is the only way to get a reliable diameter measurement in such conditions. Over the decades this solution has increased in reliability and robustness, and today a few vendors, such as Balance Systems, are recognised as offering great solutions.
The cycle time for a mid-size part on regular OD manual grinders can be around three to six minutes. With this type of machine tool, the dimensional accuracy of the part is subject to human error as the operator must measure the diameter of the workpiece, calculate the residual overstock, and then proceed with the next machining step. In order to reduce the risk of scrapping any parts, operators tend to be conservative and remove less material than necessary. So, a vicious loop that increases the cycle time is established which, in turn, increases the labour costs. By using an in-process gauging system, this process is done automatically by the machine with a ramp-up of production volume achieved.
It’s clear to see how it would be worth investing in such a solution: A 6-minute versus 1-minute cycle time, without and with an in-process gauging system respectively, is a very powerful argument. Whether you need to produce medium volume batches or extended volume runs, the ROI of an in-process gauging system is extremely attractive. What could your company do with six times the production capacity?
Be first to see all the updates from MTDCNC
Our newsletters frequency varies dependant on content
All the latest deals from the industry feature on our newsletters