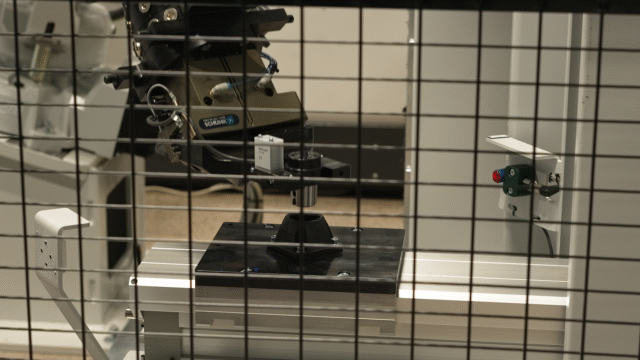
Unlock the power of flexible manufacturing with true end-to-end automation!
Think Fastems is just about pallet automation? Think again. In this exclusive walkthrough, Mika Laitinen of…
By our experience, the most common misconception around automating CNC machines is to consider one’s production of having too small volumes for automation. Most manufacturers recognize the need and benefits of automation in the mass-manufacturing context but surprisingly many are unaware of the huge potential flexible automation solutions offer in variable batch production (aka high-mix-low-volume) characterized by one to some thousands in single workpiece annual volumes.
This page defines what high-mix-low-volume manufacturing is, why it takes place and what are driving forces behind it. Furthemore, it explains how HMLV production can be automated to achieve both flexibility and profitabilty, elaborated by three case examples.
We approach the topic from the perspective of metalworking manufacturing, mainly focusing on machining and supportive processes. For further reading see the best practices of CNC automation page or jump directly to our guide:
How automation applies in different production settings?
What is high-mix-low-volume production and why it happens?
How to automate high-mix-low-volume production?
To understand HMLV automation, let’s first review the three classical manufacturing settings and how automation applies in each. Industrial manufacturing typically happens in one of these categories:
Below you can see an illustration of the above categories and how they are linked with suitable automation solutions. The matrix consists of two dimensions: workpiece variance and volume.
The vast majority of production within industrial machine building happens in the blue category, that can be characterized as make-to-order (MTO) manufacturing of batches. Oftentimes there is medium-to-high variability in workpieces, thus the name high-mix-low-volume (HMLV). A classical example is a machine job operating as a subcontractor in industrial machine building, like Kempf CNC Technik or a product-owner like Allmatic requiring much production flexibility. This kind of production is typically automated using flexible automation solutions.
In mass manufacturing, workpieces don’t vary, cycle times are typically short and production rarely faces unexpected changes like urgent orders needing to pass the queues. This is the category e.g. where auto-industry part manufacturing happens most of the time. The production is typically handled with ‘transfer-line’ automation that enables very efficient manufacturing processes in stable environment.
From the perspective of automation, the third category (sporadic one-offs) can be out of scope but that needs to be defined case by case. The biggest factors defining the automation case are the total volumes of all workpieces, their variability in physical dimensions as well as quality and lead time requirements. This category can include e.g. special spare part manufacturing or special workpieces for R&D or testing purposes.
The category of ‘high-mix-high-volume’ is inconsequential as if the individual workpiece volumes get high enough, the production is handled with dedicated automation lines and if not, one is in the world of high-mix-medium-volume where flexible automation applies.
HMLV means producing many different workpieces in relatively small volumes per workpiece. In practice yearly volumes per workpiece are from one to some thousands – extending to tens of thousands in some occasions. It’s a production setting very typical among various machine building and subcontracting industries that use (CNC) machining processes in their manufacturing.
A subcontractor or a product owner manufacturer can easily have thousands of unique parts in their manufacturing porftolio. The average batch size usually varies from one to some hundreds. It’s very important to pay attention not only to single batch size but how often batches repeat, because that creates the total demand for machining capacity.
At large, HMLV production takes place because the demand for each individual workpiece is volatile, sporadic and low-to-medium in quantity. Given the amount of product variants and ‘make-to-order’ (MTO) production strategy, the end result is obvious: batch production of variable quantities of workpieces
As an example, below you can see valve blocks manufactured in HMLV context by Sant Hydraulic. Read more about how automation helped them here.
The fundamental driver for economic HMLV manufacturing is the need for efficiency, flexibility and control in production setting that is intrinsically complicated, chaotic and sub-optimal. In our view, there are at least six key drivers driving the need for economic and flexible high-mix-low-volume production:
The below illustration, based on our four decades of automation experience, summarizes in principle how economic HMLV production can be achieved and also describes the factors that are creating the demand for it. It’s important to consider the whole manufacturing portfolio, not just a single or few workpieces and try to optimize their flow as that certainly won’t fix factory level issues. That is to say, high-mix-low-volume production needs more of total than individual workpiece level solutions.
FOUR STEPS ON HOW TO AUTOMATE HIGH MIX LOW VOLUME BATCH PRODUCTION:
As end result, flexible automation enables in HMLV context what LEAN philosophy calls flow and order-driven production: batch sizes, work-in-progress and stock decrease, lead times speed up and the whole production is more accurately be based on current demand vs e.g. trying to optimize set-up times by manufacturing over-sized batches to stock.
Use our solution finder to understand what kind of flexible automation solution could fit your CNC machinery set-up. You could also see if we have a ready-made interface for your CNC machine or take some time to understand the best practices of CNC automation. To see high-mix-low-volume automation in practice, keep on reading!
Kempf CNC Technik is a subcontractor working especially with hydraulic components. Their goal has been to achieve constant and low unit cost regardless of batch size. This means that as a subcontractor, they can offer pricing that is not determined by the order sizes. Sounds quite remarkable! See the case story and below video for more information.
Allmatic supplies machine vices. For them, automation enables long unmanned shifts and flexible production. See their agile manufacturing cell in practice in below video and read more in the case story.
SKF was looking for economic batch size one in turbine bearing manufacturing. With multiple integrated devices, highly standardized and optimal process, they are reaping the full benefits of intelligent automation.
Be first to see all the updates from MTDCNC
Our newsletters frequency varies dependant on content
All the latest deals from the industry feature on our newsletters