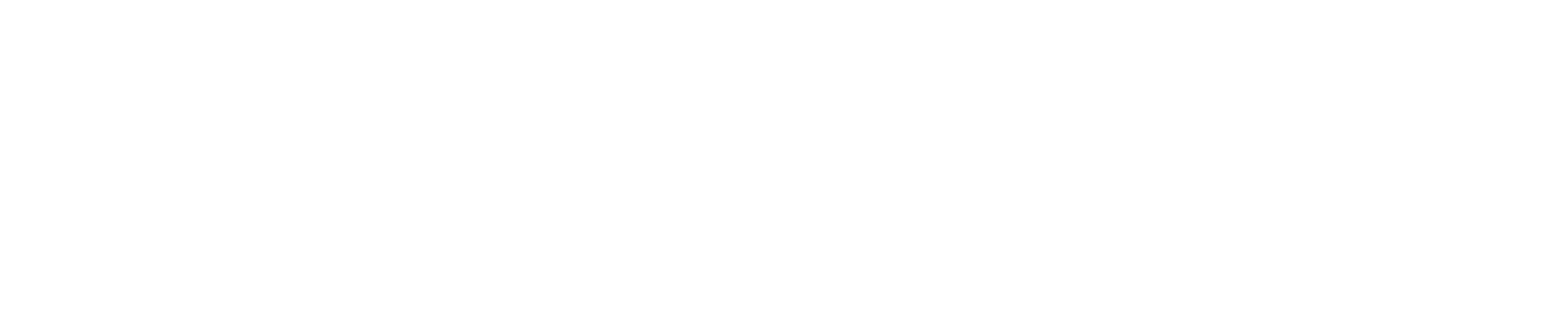
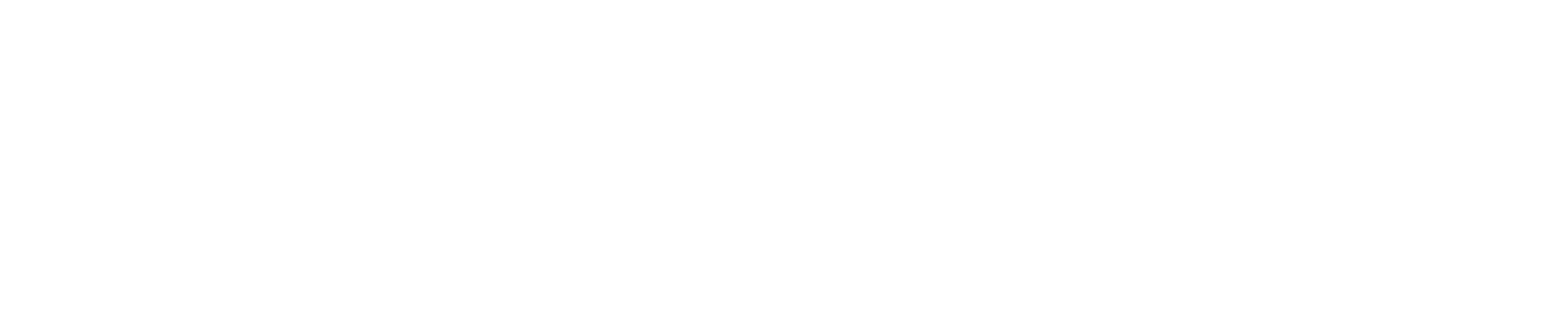
Se 1 | Ep 2
What is an industrial metrologist?
In the previous issue, metrology expert Ian Wilcox introduced us to the three types of metrology as defined by the Bureau of International Weights and Measures (BIPM). In the article, Ian detailed the three types of metrology – Scientific, Applied and Legal Metrology. In this follow-on feature, Ian delves into the implementation, effectiveness and value of metrology to a manufacturing business.
Metrology is a science-based system that as stated by BIPM ‘includes all theoretical and practical aspects of measurement, whatever the measurement uncertainty and field of application’. We all use the same units of measurement, standards, calibration and traceability and estimations of uncertainty.
But the key point was how Industrial Metrology though supposedly in the metrology gang, living as it does within Applied Metrology, has other overriding motivations that undermine pure metrology and create interruptions in how it is applied or even subdue it all together.
I invited you to ask yourself as manufacturers what regulation/legislation you must adhere to regarding actual measurement, not overall quality. I contrasted the limited requirements seen in manufacturing with that required by Calibration Laboratories that have to comply with ISO:17025 and its rigorous audits.
Finally, I observed that most organisations based on those three types of metrology, exist to create a metrology-related output, it is their ‘raison d’etre’. Whereas industrial manufacturing’s reason for being is not metrology, but product output and productivity.
There is no question in my mind, driven by years of observing, tackling and teaching Industrial Metrology, that industry would benefit from treating metrology as they see lean and general productivity improvements. It is a vital tool to drive productivity and an enabler of continuous improvement.
The challenge as I see it is that most companies are starting from a historic low. With no or very limited regulatory or contractual imperative, technology advances alone dominate management dreams of productivity, skills shortages, an oversimplification of specialist skills, and of course decades of boom and bust that crushed indirect roles, including strategically productive ones. With all that going on, is it a surprise understanding is low?
Industrial metrology for me, is all about managing the risk of bad data that you can make key decisions on. The risk of variation in data causes confusion and distrust between production and measurement teams, there is also the risk of overspending on measurement. Especially the risk of waste due to poor, over-resourced processes, and unsuitable technology purchases.
Each company will have its list of risks and you must quantify them. If you have the skills, use tools to assess individual impacts and their probability – and consider your tolerance levels to those risks. A proper review related to poor practices should be undertaken. I mentioned companies being at a low point in understanding, we only know what we know right? But as a quick test, try this simple tool that indicates if metrology could be an issue.
It has no granularity just your appreciation, whether you are in management or measurement. Mark where you think your company sits based on the combined scales. Estimate how high up the chart you sit based on how much you spend on metrology and measurement. Then move your pen across from left to right until you think it represents your level of quality issues/quality-related measurement waste. That’s where you make your cross.
Without benchmarking, it is your assessment and therefore subjective. Indirect costs are always too high, right? Test yourself.
Quality/Metrology costs:
• calibration requirements.
• Lots of new measuring equipment or no capital spend for a decade.
• Capability tests of equipment and operator.
• Do you employ a metrologist or at least have someone responsible?
• Do you have lots of quality engineers/controls to firefight quality issues or are you under resourced?
Quality issues/waste:
• High or low scrap/rework percentages
• Hours of firefighting product process control issues (not all will be measurement issues, but sometimes not attributed when they are)
• Disputes/mistrust between production and quality teams
• Disputes between suppliers/customers
Remember this is an indication, but if accurate and your cross is in the top right box, you should ask more questions and look into why. With high costs of quality/metrology and yet still lots of quality issues and waste, something needs fixing.
If the bottom left, with low issues and costs you seem to have it in control. But to be sure, try to put some numbers to your appreciation, as numbers will give better reassurance.
The top left box is good news with regards to issues but there are still savings to be made. Having a lot of resources can mean a lot of firefighting and short-term fixes that continually flare up, but you can quash them. Good quality/metrology should reduce issues and drive down resource needs. This is again a risk tolerance question and would benefit from closer investigation.
Lastly, the bottom right is almost as bad as the top right, as your business is leaking profit. From experience, many companies live happily here. If you are here, you do not survive long unless your customers do not have supply options and so must accept that poor-quality percentage and loss.
A metrologist is a key person within a company, using their skills across the company to enable confidence and cost efficiency in the numbers that a company measures and reacts to. But how?
I cannot lay out every nuance and tool that metrology can offer. I write to create a foundation of knowledge, spark thoughts and touch on key terms and tools that can then be researched as required. How I break it into two sections. Spreading and mentoring good practice and applying metrology tools to monitor capability.
Spreading good methods
An effective metrologist should champion and spread good practice to all those that measure. Teach them the correct selection and use of equipment, the understanding of the causes of variation and the importance of good measurement.
Set up a couple of measurement champions that can help spread good practices. It also helps with succession planning should your metrologist leave.
More people in a manufacturing company pick up measuring equipment and measure than most would appreciate, often making a production decision based on their results. If the measurement is ‘wrong enough’ with no oversight, then quality issues will follow at assembly, or in the field.
Measurement equipment
A good metrologist should understand the science of the measurement equipment and its sensor technology. Measurement variation can be heavily influenced by the misapplication of technology. Measurement equipment needs care, not only when in use but general maintenance and cleaning. To get long and reliable life from any equipment, simple maintenance and cleaning schedules can pay their way.
Measurement technology has moved on in the last 30 years. When you need to replace your equipment, like-for-like isn’t always the best option. But be careful, new doesn’t always mean better, a metrologist will evaluate measurement capability and help evaluate the cost versus benefit. When it comes to coordinate metrology, equipment will be a capital purchase. Buy right, use it well, look after it and monitor its capability.
Calibration
This is one area that is almost always specifically mentioned in supplier contracts and associated quality management systems. Calibration tethers your equipment to the standard unit it outputs, a process of traceability to the relevant international standard unit. Knowing capability over time can mean calibration cost savings but also may show your intervals are too big, adding the risk of errors.
Managing risk through monitoring and evaluating
Measurement is like any production process, the capability of output (the measured value) will vary, and so process capability needs to be monitored by testing. When you first introduce new equipment, the supplier can only offer you generic accuracy and repeatability data. Often evaluated in better conditions than you will use the equipment, certainly with experienced operators and on a test piece or calibrated artefact. The reality of your environment is that novice operators and your component characteristics will all invariably add to the equipment specifications.
Measurement System Analysis (MSA) is a big topic, a toolbox of measurement capability tools, offering options to best fit the circumstances and needs. Many will have heard of GR&R, one of the tools, and the companies that often apply them as part of supplier quality requirements. But I make a bold but confident assertion when I say that over 80% that I have seen applied, has been poorly applied. Mainly due to a lack of understanding of MSA.
The minimum practice is to test new equipment and problem manufacturing processes, even if only to be assured there is low risk in metrology terms. Ideally, all measurement processes should be evaluated, but a recognition of time and resources will always make this a case of prioritising your effort. There are many other tools that metrology can apply based on circumstance and benefit in pursuing productivity.
I hope I have at least awakened an interest and provided some basic understanding of how metrology can add value to a manufacturing company when applied correctly. Though Metrology is not your business’s output, metrology is a key part of driving your productivity. Enabling the reduction of scrap and rework, providing reliable data for continuous improvement, and cost reduction both in manufacturing processes and even measurements of own costs. Consider it.
Subscribe to our Newsletter today!
Stay up to date with the latest industry news and events.
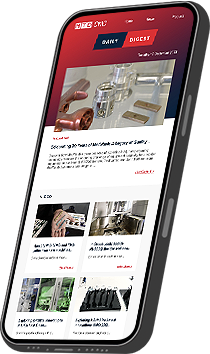