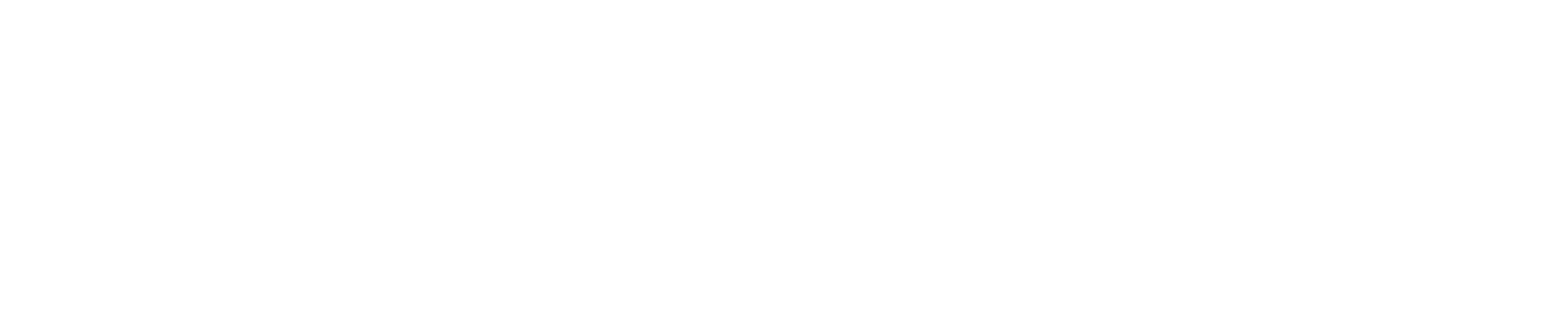
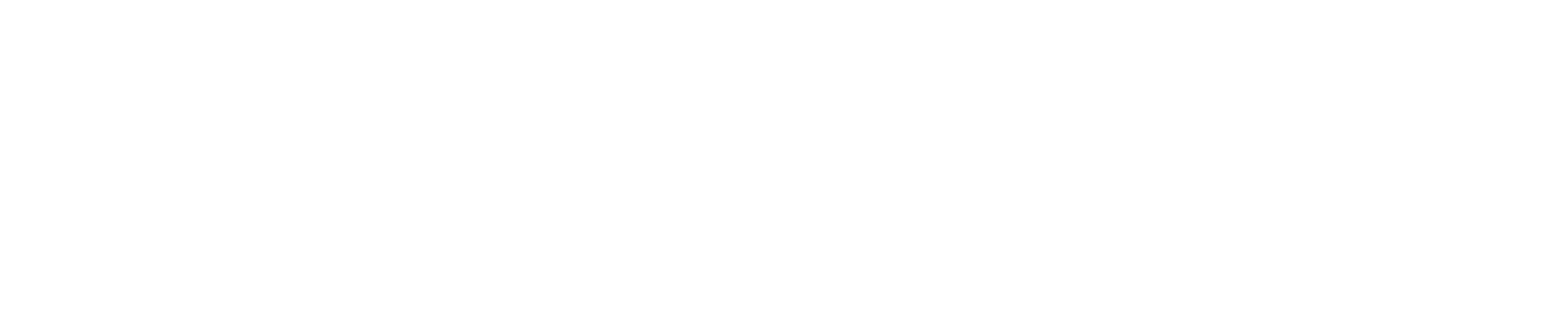
Se 1 | Ep 4
Vintage restorer soars with Mazak
Founded in 1991 and nestled in the heart of Bedfordshire, Kennet Aviation specialises in the renovation and servicing of historic aeroplanes. Over the last 30 years, the company has restored 15 aircraft, including a Supermarine Seafire used in World War II. The company restores aircraft to the stringent standards required by the Civil Aviation Authority (CAA) – to do this the company has invested in Yamazaki Mazak machine tools.
“It has always been difficult to source parts to restore and service old aeroplanes,” explains Tim Manna, Director at Kennet Aviation. “Components can be found in barns, sheds and museums across the UK, but machining parts to order is often the best way forward.”
The company has traditionally faced issues around the scarcity of parts available to refurbish historic planes. Now, Kennet Aviation can make its parts, but the CAA’s strict rules require Kennet to follow rigorous manufacturing requirements.
This includes following original drawings, using original materials and adopting traditional methods when making older parts. With many drawings now lost to time, some original materials no longer being made and traditional methods proving challenging to reproduce, the company was reliant on general subcontractors to machine crucial parts to order.
“We had long identified that the need to outsource the machining of certain components to outside contractors was a pain point for the business,” explains Tim. “Because we only require very small batches for a limited number of planes, the prices were very high. It simply was not economical to continue, so we looked into bringing the machining in-house.”
As quality and accuracy were non-negotiable, the engineering team at Kennet recommended Mazak as a potential option. “Any working aircraft we restore has to qualify for a CAA permit to fly, so we needed to choose a high-performing machining centre that could create extremely precise parts. Fortunately, one of our engineers had previously worked with Mazak and could vouch for the quality of their machines. We decided to invest in a turning centre to produce parts ourselves and save money.”
Following consultation, Kennet invested in a Mazak QUICK TURN 250MSY CNC turning centre that was installed in September 2020. Suited to demanding workpiece applications, the QUICK TURN’s integrated main spindle provides high accuracy, performance and hugely reduced lead times.
The success of the QUICK TURN prompted the purchase of a VCN-530C vertical machining centre to further expand capacity. Combined with the adaptability gained through its 12,000-rpm spindle speed and durable linear roller guides for X, Y and Z-axis machining, the machine has enabled the company to produce all parts in-house.
“By adding in-house machining capacity through the addition of both the QUICK TURN and VCN-530C, we can restore planes faster and more cost-effectively. But this has not been the only benefit – we have been able to expand our order book machining parts for other vintage aircraft, alongside taking on added general subcontractor work. Our success in providing aircraft parts for other aircraft has grown our reputation to a point where other historic plane owners and restorers have been recommending us to source manufactured parts for their aircraft. This uptick in business means we may potentially be in the market for another machine to satisfy the growing demand. Our excellent experience with Mazak means they would be our first port-of-call for any further investment,” concludes Tim.
Subscribe to our Newsletter today!
Stay up to date with the latest industry news and events.
