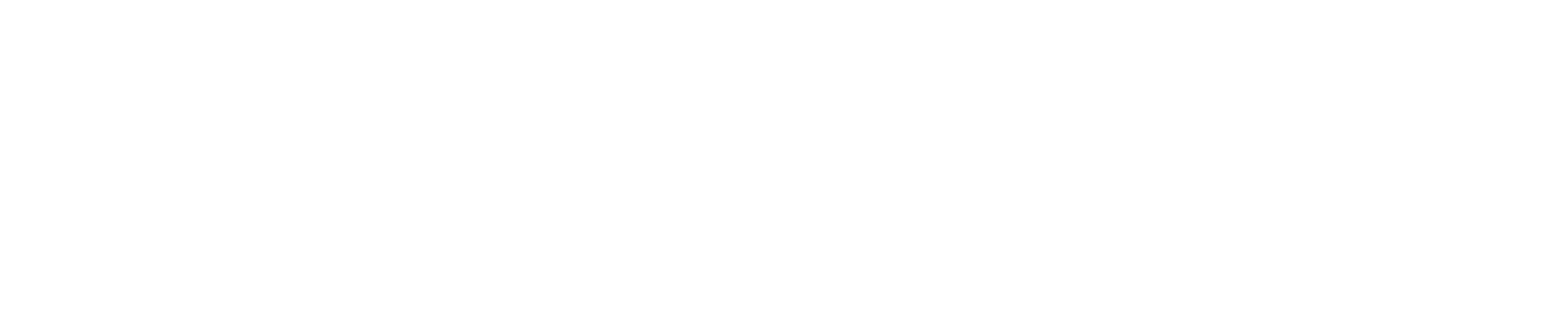
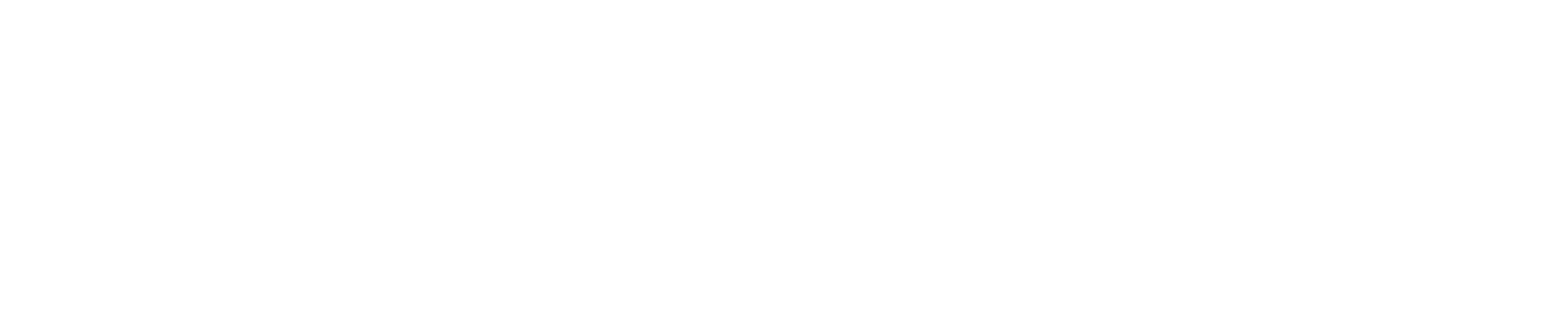
Se 1 | Ep 8
Thread of ingenuity
Founded in 2011, Interface Precision Engineering Limited (IPEL) is a specialist subcontract precision manufacturer based in East Sussex. When it comes to increasing productivity and reducing cycle times, IPEL relies on the most advanced cutting tools in the marketplace – that is why the company is working closely with Vargus for its threading applications.
The St Leonards-on-sea manufacturer specialises in machined, fabricated and pressed components for a diverse range of industry sectors. Steve Elliot, the Production Manager at IPEL says: “We mainly make parts for vacuum systems as well as a vast range of diverse work for other industry sectors, this includes flanges, parts of oil preps and we also do quite a lot of connectors for the oil and gas industry that require lots of different size parts and threads.”
Looking at an oil and gas connector part manufactured from 304 stainless steel that required an M12 thread 25mm long, Steve says: “We do large quantities of these with different sizes and threads. We spoke to Paul Smith from Vargus; he suggested using the Vargus Mach TT range. We trialled the tool on our Doosan Puma 2600 SYII turning centre and we reduced the thread cycle time from 29 seconds to 11 seconds. This was achieved by increasing the feed rate and doing a lot fewer cuts.”
Discussing the application in more detail with Paul Smith from Vargus, Paul adds: “We have the Mach TT insert and tool holder that is piped up to the high-pressure coolant system on the Doosan machine. We did one run with a standard tooling product and it took 15 passes and around 29 seconds. We managed to drop that down to four passes with a spring pass and we got it down to 11 seconds.”
Alluding to whether it impacts tool life, Paul adds: “Running at higher parameters doesn’t affect tool life. With the new rigid system on the Mach TT that has a dovetail system, it is super rigid, so we can push the tool harder.”
Referring to the challenge of cutting stainless steel, Paul adds: “304 stainless is not an easy material to cut, but with the tool being piped to the high-pressure coolant, the fluid is getting right to the cutting edge. For manufacturers to get the best performance, they can use the Genius software which is free to download at www.vargus.com or we have got a team of engineers that are all time served that cover the whole of the UK and also, we have got the products which are ready in the country for next day delivery.”
Looking at threading applications in the milling department, Steve Elliot from IPEL says: “I think the main headaches are threading operations and putting taps into parts, we do a lot of stainless and exotic materials. In the past, using taps could be risky on these materials, particularly when they are low volume high-value parts. We don’t have any facilities in the house to remove broken taps, so we would probably have to end up subbing it out to someone to get it wire eroded out. This is a lot of cost and there is a lot of added lead time to that, which is what we are trying to avoid.”
.
With this scenario being a common occurrence for subcontract manufacturers, IPEL moved many processes to thread milling. On one specific part that had 18 threaded holes, IPEL converted to a Vargus threading process from a standard process, Steve explains: “On this part, we were starting to use thread mills as opposed to tapping, but it was increasing the cycle time. I spoke to the guys at Vargus and they recommended their new Mach TM tool. It immediately reduced the cycle time significantly. We have gone from about 10 seconds a hole down to 2 seconds a hole. This is all completed in 1 pass, so we are winning all round. In the tooling trails, the tool life is looking great as well.”
Discussing the thread milling process, Paul Smith from Vargus says: “We applied the Mach TM system and managed to drop from 10 seconds to 2 per thread with just one pass instead of two. The operator was blown away.”
Alluding to operator concerns regarding running the machine at such high speeds when threading at such high speeds, Paul says: “We have the Genius software and it will guide machinists through the process and ultimately, at the end give you a part programme ready to use with the tool.”
Vargus UK Managing Director Graeme Troughton commented: “ The new Mach TT and TM product ranges are a genuine step change in the market, they are products our competitors cant challenge as yet. My advice to customers who cut threads in mass either milling or turning is you will almost certainly see huge benifits from testing and then using this product range. We invite UK manufacturers to challenge us and trial this fantastic new range of tools”.
Subscribe to our Newsletter today!
Stay up to date with the latest industry news and events.
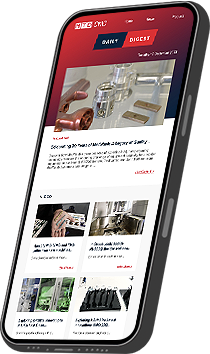