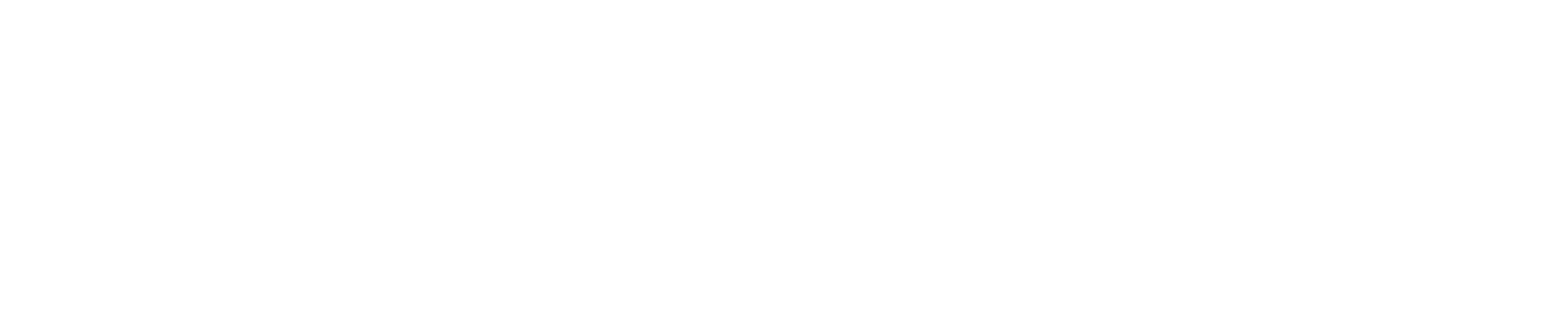
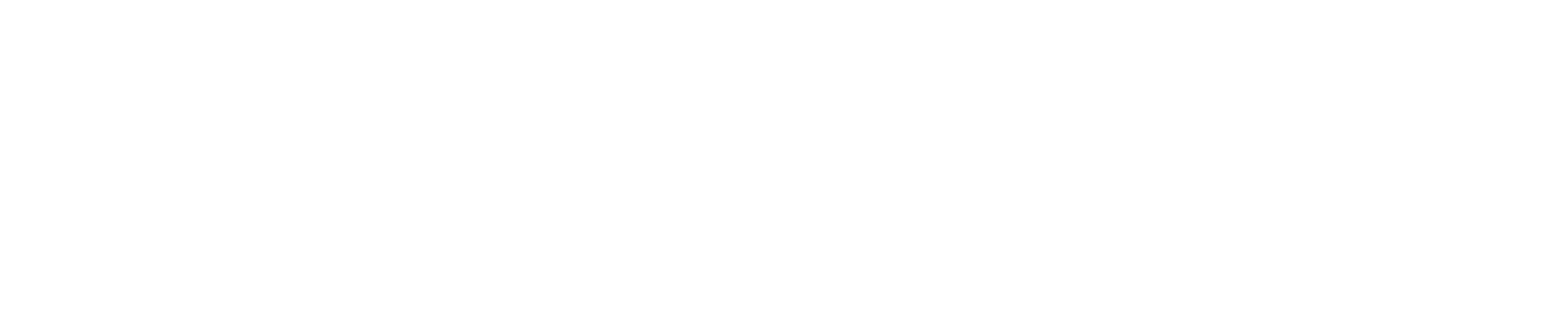
Se 1 | Ep 13
The right tool for the right CNC
The history of computer numerically controlled (CNC) machines dates back seven decades. During the 1950s, CNC technology was difficult to introduce due to manufacturers’ scepticism. Today, it is hard to imagine the world of manufacturing without CNC machines. In material removal processes, a CNC machine has become the central link that determines the functional capabilities of a manufacturer.
CNC machining centres are complex machines that continue to evolve and improve. The advancement of CNC technology is based on the progress in various fields such as the main spindle and its bearing units, machining slideways, high-velocity drives, computer engineering, hydraulics, electric motors, robotics, sensors and much more. When compared to a conventional machine with mechanical parts, the share of modern digital CNC machines is significantly higher.
CNC technology will continue to be the backbone of machining methods in the near and far future. The development of CNC machines is intended to increase the versatility, productivity, stability, reliability and accuracy of a given machine. These targets are ongoing milestones that assure contemporary machining results. The leap forward relates to machining centres that combine subtractive and additive technologies that are both CNC machined and 3D printed. At the same time, a complete rethink of CNC advancements has been brought about by Industry 4.0 and the concepts of smart manufacturing. In a smart metalworking factory, there is a continuous information exchange between the real world of CNC machines and the virtual world. This world functions according to the features of the machined parts and their respective theoretical characteristics. Smartly balancing on the boundaries of these worlds and analysing the real-time information is the ability to make decisions and corrections that are made by computer-controlled units.
One element that is much smaller, substantially cheaper and considerably less complicated when compared to a CNC machine tool, is a cutting tool. The tool is the link that directly removes material from a workpiece and closes the process loop of ‘machine and workpiece’. Due to objective reasons, the cutting tool element is subjected to less fundamental changes and the cutting tool is frequently identified to be the weakest link in the processes. Something that also limits system capabilities. Therefore, appropriate upgrading of cutting tools should be considered as an integral part of the progress of CNC technology.
A conventional approach to making cutting tools relates to designing innovative cutting geometries, using advanced cutting materials and applying leading production technologies that are intended to improve tool life, ensure greater material removal rate (MRR), provide higher accuracy, and increase reliability. Nevertheless, Industry 4.0 trends in the development of CNC technology are placing ever greater priority on the digital component of the cutting tool.
Information has constantly accompanied cutting tools even before Industry 4.0. Catalogue data, tool drawings and recommendations regarding applications were provided in printed formats and later in electronic formats and these continue to be essential for the typical metalworking machine shop.
Computerisation has affected customer support by providing expanded capabilities in the form of data. Various software applications have enabled the selection of optimal tools and the ability to estimate tool life under specific machining conditions. The combination of ISCAR’s NEOITA and its Power Consumption applications enables a quick calculation of cutting forces, bending load and power consumption. It also enables the user to find suitable cutting material grade, the right tool for a specific application and provide an analysis of competitors’ products alongside other useful functions. Customers can easily access data and related information through computers and mobile devices, but now, advancements in network communications have introduced the world of metal cutting to the virtual electronic world.
Digital twin technologies complement manufacturing processes. Machining modelling, collision checking and process optimising to find the best cutting strategies are only some examples. In a smart factory, the digital twin is the most significant brick of the foundation. Understandably, only a tool having its digital twin is acceptable for the smart factory’s toolroom.
The progress of CNC technology leads to new demands for cutting tools. A tool manufacturer is expected to be a provider of a product that ideally combines a cutting tool as a material object, its real-time digital twin and an appropriate software environment. This allows the seamless incorporation of the tool data in the CAD/CAM and virtual manufacturing environment, directly transmitted by Internet of Things (IoT) networks – tool packages and virtual assemblies.
To make tool representation clear for various computer systems, the ISO: 13399 standard was developed and ensure the platform’s independence. This standardisation is necessary for other digital components of the tool package to unify data related to tool life, calculated loads, machining conditions and lots more.
ISCAR’s digital tool component, which is based on the ISO: 13399 standard, includes the following characteristics:
- E-catalogue with various search functions, updated promotion information and reference data.
- The .p21 file (a STEP file) includes a product identification class for a comprehensive tool data representation and exchange.
- 3D tool representation for computer modelling and CNC programming in accordance with the ISO: 10303 standard (STEP).
- A 2D tool representation in DXF format for planned process documentation, drawings, tool layouts and setup sheets.
- Virtual tool assembly options for turning, milling and holemaking tools intended for generated digital assembly twins in both 3D and 2D representations.
- NEOITA – ISCAR Tool Adviser, an expert system that recommends optimal tooling solutions for a specific application.
- The machining calculator and the cutting material grade optimiser software applications.
A rapid pace of industrial digitising takes CNC technologies to new heights. This gives a boost to appropriate changes in the product range of a tool manufacturer and demands strong links between a cutting tool and its virtual digital component.

Subscribe to our Newsletter today!
Stay up to date with the latest industry news and events.
