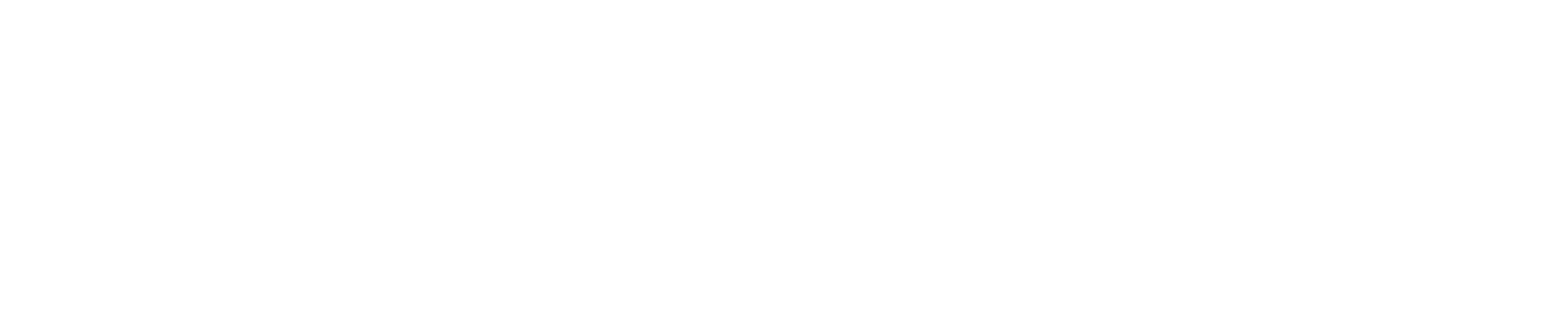
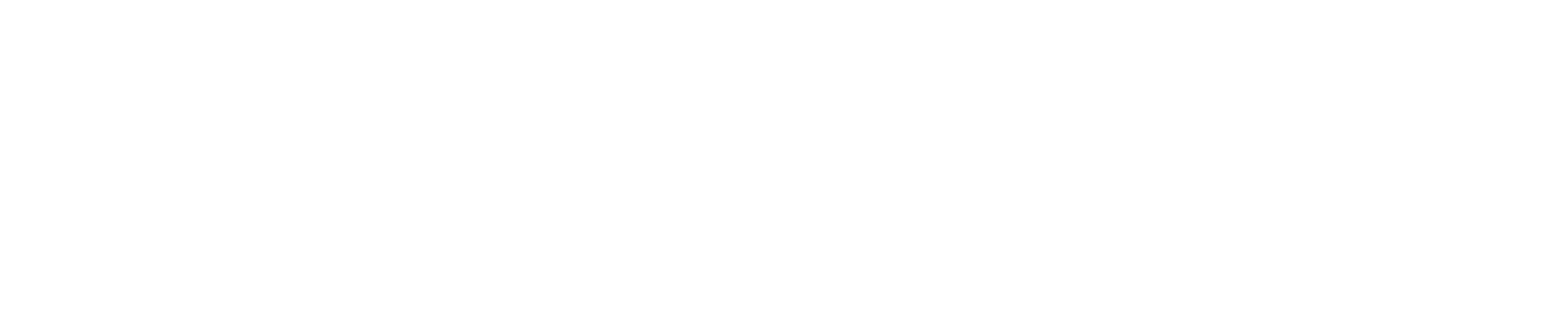
Se 1 | Ep 10
Standing still is not an option
Last month MTD magazine had the privilege of being invited to the Horn Technology Days event in Tubingen, a short drive south of Stuttgart. The threeday event from the 14th to the 16th of June was a genuine masterclass in cutting tool innovations – a fact underlined by the event drawing more than 3,300 visitors from 37 countries. By Rhys Williams
The Horn Technology Days event was the first event in four years following the Covid hiatus. The eighth Technology Days event had more innovations than ever before and these were well received by the 3,300 registrations that were added to by a post-event weekend of festivities at the company that saw an additional 3,000+ staff and their families in attendance. With expert lectures, live machining demonstrations, factory tours, industry-specific application and demo areas and 35 co-exhibiting technology partners, Horn executed the event with the same precision as its products – giving eight technical seminars in four languages and 19 live machining demonstrations across three of its factories.
The theme of the event was ‘Mastering Processes’ and under this slogan, Horn provided a series of in-depth technical presentations. The eight technical seminars included HiPIMS – a quantum leap in coating technology, Lead-Free – machining brass and steels with complete process reliability; Polygon Turning, High-Speed Whirling and Turning; Gear Teeth and optimal processes and the buzzword on most manufacturers’ lips – ‘E-Mobility’ and the solutions available from Horn. Other presentations included Enquiry to Delivery in 7 Days – tools for profile grooving & broaching; Turning, Milling and Drilling – and how to achieve the right result with ultra-hard grades and finally, Expertise in Sliding Head Turning.
To underpin the overall theme of ‘Mastering Processes’ and the company’s expertise in each of the disciplines, Horn provided a range of fascinating machining demonstrations – and to really capture the imagination, a gallery of displays from projects the company has played an integral role in. During a press conference where Sales Director Andreas Vollmer and Joint CEOs Matthias Rommel and Markus Horn paid tribute to the company’s late CEO Lothar Horn who sadly passed away in February, the new board of directors were keen to underline Lothar’s slogan of ‘Standing Still is Not an Option’. Emphasising that the family business founded in 1969 has the ‘same values with new approaches’, the directors discussed the company’s strategy for continued growth. This included an insight into the implementation of process automation and product configuration through the Horn Tool Configurator (HTC), Industry 4.0, increased shop floor automation, additive manufacturing, new coating technology and the April opening of a new Horn facility in Thailand.
Looking at how Horn is implementing the late CEO Lothar Horn’s slogan of ‘Standing Still is Not an Option’, the board alluded to its new automated grinding cells. The ‘Grinding Cell 2.0’ has been introduced in the production facility with new grinding technology, a new operating concept and new workpiece changers that are unique to Horn. This has been instigated to deliver maximum automation output and flexibility. New automation technology has also been introduced to the toolholder production department with a series of robot-loaded DMG MORI machine tools that deliver fast workpiece setup and changeovers with flexible workpiece handling. Both the shopfloor automation systems fit seamlessly with the company’s drive to introduce customers to the HTC and the Horn Machining Solution (HMS).
The free-to-use software enables manufacturers to rapidly configure special tools with automated drawings, quotations and production documents. The digitalised process flow through product configuration with a linked CAM programme, streamlines the process for manufacturers to configure special tools with a faster turnaround time than ever before. The system also automates feature recognition, and process assignment and generates a full NC programme to simplify the experience for customers.
Horn has also invested extensively in new coating technology with seven new CC800 HiPIMS coating machines recently installed in Tubingen. With a total of 12 HiPIMS machines (10 in Tubingen), the coating centre has increased the flexibility and variation of available coatings. The company has also made a significant investment in additive manufacturing. Currently utilised for prototype tooling for future catalogue items as well as component production for its manufacturing facilities, Horn is forecasting that 3D printing will play an increasingly important role in the production of future tooling lines.
Following the press conference, journalists were given a tour of the production halls and witnessed the new advancements first-hand. As part of the tour, cutting tool demonstrations were provided to show how the latest innovations were being applied to machine tools from technology partners such as Index, Citizen, CHIRON, DMG MORI, GROB, Tornos and Mazak among others. In complete synergy with the seminar programme, parts such as automotive drive shafts, medical bone pins and screws, electrical connectors, jewellery and mould tools were all produced via live demos on the respective machine tools. Whilst supplementary exhibits included three supercars, plug-in hybrid Mercedes engines and headlamp housings, aerospace engine components and even a Prometheus combustion chamber for the Ariane 6 rocket. Other exhibits included an ambulance stretcher, vets’ tools, wedding rings and clocks and much more. It was here that Horn emphasised the importance of ‘Mastering the Process’ to achieve maximum performance with the tools applied.
Not only is Horn ‘talking the talk’ with regards to ‘Mastering the Process’, but the Tubingen manufacturer is also ‘walking the walk’, leading the way on research projects in a wide range of industry sectors. One such project the company has undertaken is the BMBF German government-funded ZykloMed medical research programme. Set up to improve the functionality of medical implants through novel synchronised machining processes, Horn worked with Index, Tessky, BEUTTER Precision and the Karlsruhe Institute for Technology to develop an eccentric turning process for the creation of oval-formed bone pins that will prevent potential pin movement in the patient post-surgery. By synchronising the rotation of the workpiece and the tool to turn the external profile of the bone pin, the polygonal form has been achieved along the length of the pin.
Discussing this government-funded programme in one of the technical seminars, Horn UK’s Andrew Tipple explained how Horn was also instrumental in developing the tools and process for machining polygonal screw heads – a complex polygonal turning process with a machining time of just 9 seconds with thanks to Horn’s innovative tooling developments. With the workpiece and tool axis in parallel, the workpiece and tool rotation is synchronised at a fixed speed ratio with an offset between the workpiece and the tool axis. This research project overcame the challenges of the interfering contour, the chipping and relief angle variation, the setting range of the radius and the cutting speed challenges.
On the same bone screws, Horn was instrumental in creating a variable pitch thread profile where the crest width at the external diameter of the thread remains constant. The reason for a variable-pitched bone screw is to increase or decrease the tension placed upon the bone during fixing. Implementing a high-speed thread whirling operation with a pre-cutting and finishing tool, this process again had to overcome the challenge of toolholder interference, the chipping and relief angle variation and also the long overhang of the screw.
A true allrounder
As the above medical project and applications exemplify the ingenuity of Horn, the company is recognised as an industry leader in everything from sliding head tooling, grooving, parting, broaching, reaming, threading and turning to special application products. Speaking with Horn specialists at the event, it became evident that the company which has a manufacturing facility in Ringwood on the South Coast, is a prominent manufacturer of indexable milling technology. This was emphasised by the recent launch of the new System 409 tangential milling series that was introduced at the Moulding Expo in Stuttgart in May. The new patented M409 tangential milling system incorporates rhombic form indexable inserts that are highly polished for the machining of aluminium alloy materials in the ISO N group.
Shifting up a gear
In a truly global marketplace, it can be acknowledged that customers in the UK may have different product requirements from manufacturers in other regions. With upwards of 60 Horn UK customers attending the three-day event, it was clear that many were attending the technology days in search of a specific solution. Broaching, gear skiving and threading were three key areas of interest for Horn UK customers – many visitors were intent on finding (and subsequently found) a solution at the event. Discussing why these key areas were prominent in the UK, Horn UK’s General Manager, Mr Mike Green says: “We have a huge number of enquiries that are coming from a wide spectrum of customers from small and medium manufacturers up to large OEMs. In the past, a lot of these manufacturers have had to send components out for specialist machining of gears and splines. A lot of our growth is from the aerospace industry coming back with a bang, as is the medical industry with a requirement for very small broaching applications for joint production. There are also excavation companies that make their engines and gearboxes in the UK, and if they are doing R&D projects, they will produce 2 to 3-offs where they can generate gear forms on their own machines.”
“The upturn in this side of the business is down to the companies realising that with a suitable turning centre and software, there is no longer a need for specialist skiving machines. There are customers out there that don’t realise they have machines capable of undertaking skiving operations. Machine tool manufacturers are now using the capability of turning centres to undertake skiving and promoting it as a sales tool – and we are operating off the back of that. We have been very successful in many industry sectors with skiving, but there is much more to go at.”
Another of the eight technical seminars at the Technology Days event on gear machining and optimal processes was presented by Horn UK’s Alex Brown. Alex provided an insight into the product range that includes profile insert tools, full profile mills, circular milling cutters, deburring mills, broaching tools and of course gear skiving tools. The gear skiving series incorporates the WSA series of solid carbide tools, the WSX screw-in type tools and the indexable insert WSR that extends from 22mm up to 300mm in diameter.
The same presentation provided an overview of the slot, profile and gear broaching solutions for producing external and internal profiles, broaching by gear shaping, conventional broaching and broaching with driven tools on CNC machines.
Alluding to the broaching technology, Mike adds: “We have a new product from France and it is the Rolls-Royce of broaching. Two years ago, we did trials in Germany with every manufacturer’s product, and ours came out on top by a long way in terms of speed, productivity, accuracy and length of stroke. It really is faster than anything else on the market.”
Giving an overview of the business performance in the UK, Mike says: “Last year we bounced back to 2019 growth levels after a challenging time during the pandemic. We are now on an upward trajectory with a projection of up to 11% growth this year. There are inevitably obstacles in the way such a skilled staff and material shortages.”
“Originally, we were an internal and external grooving, turning and milling company, but it has grown significantly from there. The special side of our business now accounts for nearly 30% of our turnover. This is down to the nature of the UK market that specialises in high-value low-volume components. With our special’s division, we can create the drawings in the UK and manufacture some of the tools in the UK with others being made here in Germany. Our turnaround time for delivering parts to customers can be as little as two weeks, which blows most of our competitors out of the water. We have also recently opened a facility in Thailand that specialises in MCD tools that can create a mirror finish on components, providing the machine tool and environment are stable. That region of Asia produces 80% of the world’s spectral lenses and our tools are eliminating polishing by creating a mirror-like finish for manufacturers in Asia – this is another area that will deliver future growth for us.”
Subscribe to our Newsletter today!
Stay up to date with the latest industry news and events.
