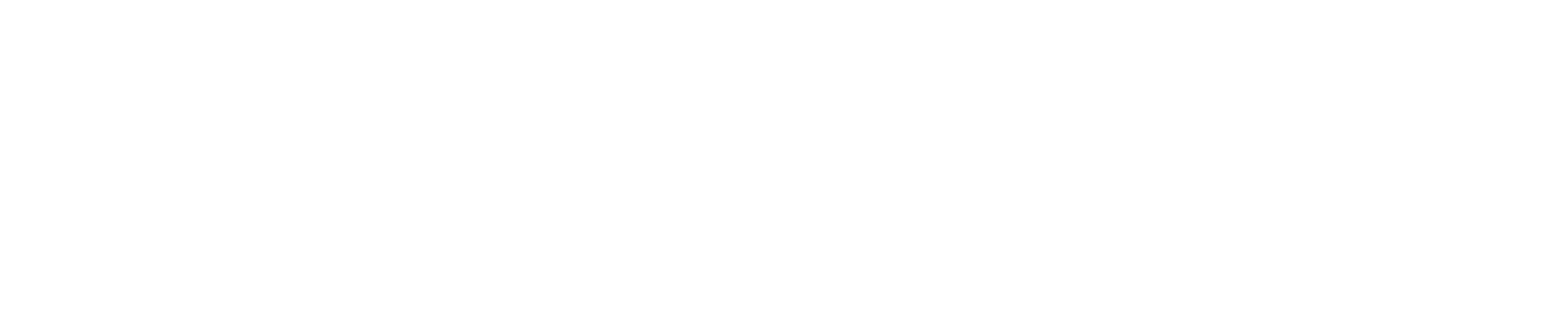
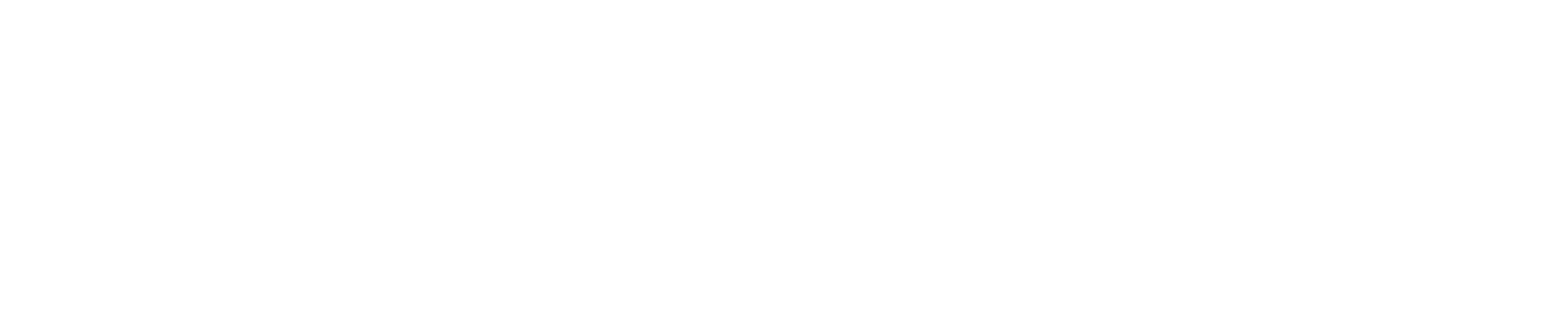
SME reorganises its entire production processes
As a Swiss SME that has thoroughly examined its production from a digital perspective, Sistag AG has recognised the potential of bits and bytes. The company has modernised its facility with a Flexible Manufacturing System (FMS) from Fastems and this approach is yielding interesting results with new experiences and ambitious plans.
The globally active Sistag AG, headquartered in Eschenbach in the Canton of Lucerne, manufactures isolation valves for a wide range of industries. This includes pulp and paper, food and beverage, wastewater treatment and biogas/chemical plants. “In addition, we specialise in knife gate valves, known under the brand name Wey Valve. These valves are used in the petrochemical, oil production, and mining industries. Our mechanical production here employs around 165 employees, producing approximately 25,000 to 30,000 knife gate valves annually,” says Manuel Schmidlin, Head of Manufacturing at Sistag.
Like many other Swiss SMEs, Sistag faces high manufacturing costs. Manuel Schmidlin notes: “Land is expensive and labour costs are high. Moreover, finding skilled workers for production is challenging, so we have increasingly focused on in-house training.” To economically produce and manufacture, machines at Sistag must run almost non-stop. “We also have the advantage of being particularly strong in the field of special valves. Due to the relatively high level of automation here at Sistag, we can also compete in terms of pricing,” adds Schmidlin.
The housings, a core component for knife gate valves, are manufactured on two horizontal machining centres. In 2005, the company invested in an FMS from Fastems, specifically a Multi-Level System (MLS), initially connected to an OKK HM 630. In 2010, the system was expanded to a total length of 35m, with a second OKK machine of the same type added.
In 2022, Sistag decided to modernise the MLS. Manuel Schmidlin explains: “The electronics were still running on 32 bits, and the system was essentially at ‘End of Life’ with no replacement parts available. During the upgrade to a 64-bit system, we conducted a complete retrofit, both in terms of controls and mechanics.” As Sistag has been pursuing a consistent digitisation strategy for about four years, the FMS was not only updated with the Manufacturing Management Software (MMS) from Fastems but also placed a significant focus on digitising the entire production facility.
According to Manuel Schmidlin, the company has primarily grown historically in its 60-year history. Sentences like ‘We’ve always done it this way’ has been heard by the production manager many times.
“Our projected business has significantly increased. When a customer orders valves today, it’s not three or four, but immediately 400 or 500. With our existing infrastructure, we were not able to plan such large orders efficiently from start to finish. We had great difficulty keeping our machine capacities and we had no overview of what was happening at what time and where the priorities were. Therefore, our goal was to control our entire production with MMS as a central MES (Manufacturing Execution System).”
‘The Terra Incognita’ of A Manufacturing Organisation
The MMS from Fastems provides all the prerequisites for this digitisation approach, as it is currently one of the most powerful solutions for planning, running and monitoring automated machining production. The MMS automatically plans production up to 96 hours in advance while considering all necessary resources, such as raw materials, NC programs and tools, including their tool life.
Manuel Schmidlin is fully aware that for consistently planned production, standalone machines, manual workstations and inspection stations must eventually be included in the whole digitisation process, in addition to the automated equipment. Not an easy task, as these areas are often still a ‘Terra Incognita’ in a usual manufacturing organisation. Nevertheless, this situation is set to change at Sistag with the implementation of a Fastems MES solution for non-automated equipment – Work Cell Operations (WCO).

Subscribe to our Newsletter today!
Stay up to date with the latest industry news and events.
