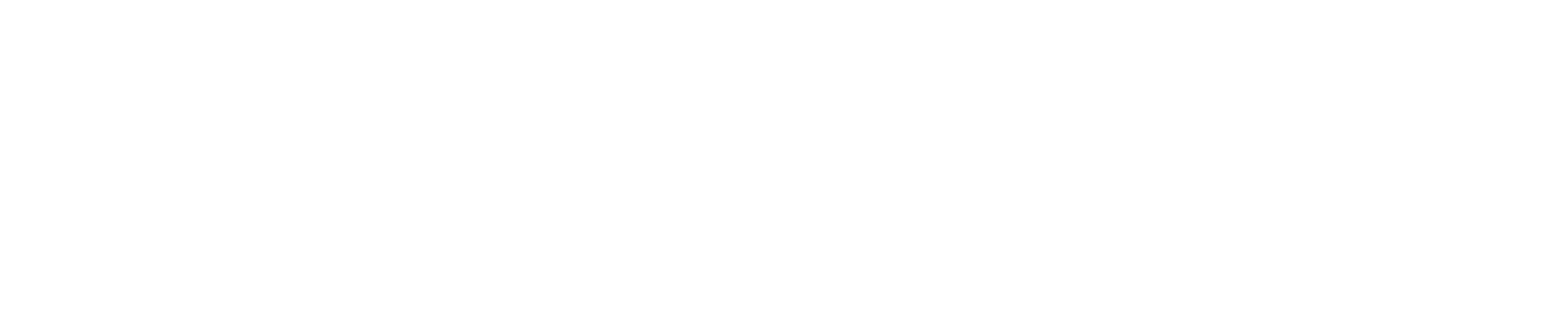
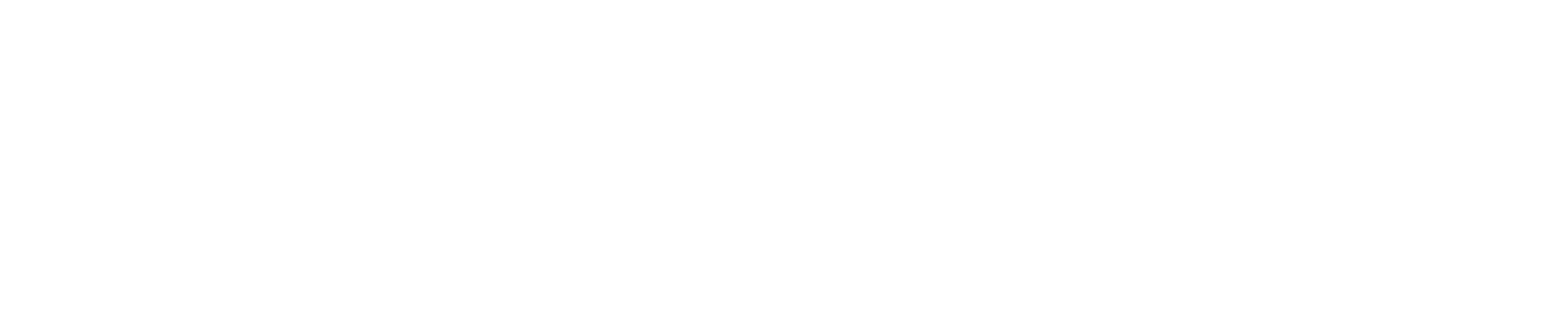
Se 1 | Ep 1
Renishaw breaks the ‘glass ceiling’ on encoders
When Renishaw targets entry to a new marketplace, convention is not a path it travels. Renishaw looks at how existing manufacturers develop products and then completely rewrites the script. After over 30 years of producing ‘open optical encoders’, Renishaw instigated the development of ‘enclosed optical encoders’ for machine tools. The outcome is the FORTiS™ encoder and the results are ground-breaking. By Rhys Williams
With the majority of Renishaw’s repertoire of products being symbiotic to the machine tool industry, the UK manufacturer sensibly set about applying its expertise in open optical encoders to enclosed optical encoders for machine tools. The concept has been 10 years in the making, but Renishaw is about to turn the encoder industry on its head with the arrival of the FORTiS encoder.
If you are somewhat naïve about the technical merits of encoders in machine tools, don’t worry – before visiting Renishaw my understanding was equally limited. In the simplest terms, ‘glass linear scales’ are found on an increasing number of machine tools, providing direct linear position feedback from the X, Y and Z axes to the CNC control, thus helping to improve the level of position certainty and repeatability. This is not far away from Renishaw’s own modus operandi in simple terms, but I also wondered why a glass scale would be inside a machine tool – surely it’s susceptible to damage in a harsh environment?
It would appear that with the FORTiS encoder range, Renishaw investigated the market, and identified the pain points of the industry that span from maintenance and changeovers, to performance and longevity – and it has found a completely new solution with the FORTiS product. They have also done away with the ‘glass scales’.
MTD magazine spoke with Corrie Fearon, Product Manager at the Encoder Products Division at Renishaw plc in New Mills, Gloucestershire to find out more. Corrie told MTD magazine: “Renishaw is a big name in non-contact encoder products used in electronics assembly, semiconductors and general motion control. However, we decided to get involved in encoders specifically for machine tools and other harsh environments. We looked at what was available and spoke to a lot of companies that would be potential customers of ours. We asked what was good and bad about existing encoders and what the pain points were. The response from the industry was that existing linear encoders are very good for metrology, but they have three key problems.”
“The first issue is that they are really difficult to install, the second issue is that they always leak and the third is that if you shake them a little, they will fall apart. In essence, the installation requires technician-level skills and tools, the sealing has several opportunities for improvement, and the levels of vibration sometimes found in machine tools can impact positional measurement or cause internal parts to be shaken out of alignment. So, Renishaw approached it from a different angle. We found that existing suppliers all follow a similar format. If you open the encoder, you have a sprung-wheeled carriage that runs along a glass scale. We could see this design had just evolved over the last 40 years and instead of following that route, we looked at how we could utilise today’s technological advances. We wanted to eliminate the sprung carriage and all the issues that it brings to encoders. We took the measurement technology from our existing RESOLUTE product and we looked at how we could package it into an enclosed application.”
“We also wanted to do away with the glass scale and have a steel scale instead, as glass is always liable to fracture. We also looked at seal technology, and we spent about five years working with our seal supplier to come up with a seal material that provides a nice combination of low friction and better elastic response. So, if you move the readhead, you want the seal to close up as quickly as possible; something that traditional seals weren’t particularly good at, especially when it gets cold. We also wanted our seal material to work with the ever-increasing range of coolants, as there are many chemical additives and heavily chlorinated fluids that can be very aggressive against seals. We wanted to develop the most resilient and tough encoder in the marketplace, and with FORTiS encoders, we can take it far beyond the realms of current products on the market.”
So, who is this innovation for? Well, Renishaw is clearly making OEM machine tool manufacturers sit up and pay close attention to the benefits of FORTiS encoders. However, Renishaw is also targeting the tens of thousands of worldwide manufacturers with machine tools on the shopfloor with ‘linear glass scale encoders’. If these glass scales on high-end machine tools (or 5–10% of all machines as Corrie estimates) break, cause maintenance issues, or otherwise disrupt the performance of your machine tool then, in many cases, they can be swapped out with FORTiS encoders.
Have you ever witnessed poor surface finishes that you struggled to rectify? Whilst you may have been adjusting your machining parameters from the countless combinations of different speeds and feeds, changing your cutting tools and programming strategies – it could have been that you hit the natural frequency of your glass scale encoders. What if you could easily change them out for the Renishaw FORTiS encoder and eliminate the issue?
Relieving the Pain Points
To address the pain point of installing enclosed encoders, Renishaw designed the system so that specialist knowledge, tools or equipment are not required to install the FORTiS encoder. Renishaw’s patented readhead set-up LED and ADTa-100 Advanced Diagnostic Tool, which provides a user-friendly display of advanced encoder diagnostic information, ensure intuitive and right-first-time installation. During our visit, the MTD team managed to install a FORTiS encoder on a test rig in 45 seconds – the current record is held by an engineer who installed a FORTiS encoder at the IMTS exhibition in just 13 seconds! To do this on a working machine tool and including the time taken to access the linear axis, Renishaw estimates that an encoder can still be installed in less than 15 minutes.
Not only are the encoders designed to be simple to install, but Renishaw has also introduced its patented LED system that indicates signal strength. So, a blue LED showing maximum signal strength will confirm the correct alignment of the encoder’s body and readhead whilst an axis is traversed. This reduces the skill requirement and mitigates the risk of rework or unplanned machine downtime caused by incorrectly installed encoders. As Corrie says: “The installation technique we developed means that FORTiS encoders self-align with the transit brackets. This is advantageous when it is first installed on the machine builder’s production line, or at the machine dealer’s facility. It also helps throughout the lifetime of the machine tool as it removes the need for technician-level skills and tools, which are often in short supply. For example, you do not need to use a dial gauge with the FORTiS encoder, although you can if you wish, as we have built that into the system. We have made it so simple that if everything is done right, the LED turns blue, indicating that the job is done correctly. Equally, it also tells you when it has been done incorrectly.”
Tuned Mass Damping
From the beginning, Renishaw realised a major pain point for machine tool OEMs was the impact of machine tool vibration on positional measurement. The solution involved developing several features to improve robustness against mechanical vibration and to stop high-amplitude disturbances from entering the position control loop. These include mounting tuned mass dampers (TMDs) to the encoder readhead to strongly damp resonant vibration. The TMDs are designed to counteract vibration around the vertical and horizontal axes. It is claimed that FORTiS enclosed encoders are the first to use TMDs in this way. Renishaw undertakes vigorous sine sweep vibration testing and random vibration testing on the FORTiS encoders to demonstrate vibration resistance when compared to conventional enclosed optical encoders.
To demonstrate this resistance and durability, Renishaw showed us a test lab with a ‘shaker’ machine capable of working up to 37g. FORTiS encoders have spent more than 16 hours running at 37g (at the encoder’s natural frequency) with no issues. In comparison, the leading competitors will specify that encoders are not to run at the encoder’s natural frequency. Of course, Renishaw wanted to push this further – so they invested in a much larger 75g shaker that also tests the encoders.
As Corrie adds: “The TMDs strongly dampen the vibration at the encoder’s resonant frequency and enable the FORTiS encoder to maintain impressive positional stability and long-term dependability that improves process control. If you read into the documentation of our competitors, they often have ‘get-out’ clauses stating that they must not be used at the resonant frequency of the encoder. You also have to carry out tests on your machine to prove that you are not going to do that. The reality is, if you are machining, you cannot predict the frequency of the machine vibration. The vibration depends upon the size of the tool, the type of material cutting, the number of inserts on the tool, the cutting depth and many more parameters. There are situations where the machine tool will not be working as expected. You could be fly-cutting aluminium and receiving a poor surface finish and thinking you may have hit the resonance of the machine – that good design would normally mitigate against. In reality, what you may have done is hit the resonance of the encoder and that is what you are seeing back in your control loop.”
“We have one customer that was seeing several e-stops per week on a machine on an automotive manufacturing line that was disrupting production. They changed from a rival encoder to the FORTiS encoder, and they haven’t had a single e-stop since.”
Additional vibration mitigating features built into the FORTiS encoder include the non-contact design and light steel scale that is fixed along its full length to the inside of the enclosure body. Conventional enclosed optical encoders feature a sprung, wheeled carriage that supports the read-head body as it runs along the encoder scale. The FORTiS non-contact design isolates the read-head body from the encoder enclosure, thus eliminating multiple sources of resonant vibration.
The issues around the performance, contamination and excessive maintenance of enclosed optical encoders has long pained both machine tool builders and their customer base. Here, Renishaw has put in significant research with technology partners – the fruit of that labour has now arrived.
Seal of Approval
Encoders are subjected to extremely harsh environments with the ingress of swarf, coolant and grease all having the potential to impact the performance of the encoder. To this end, high-quality lip seals are necessary to ensure long-term reliability. However, with a machine tool having a life expectancy of 20 years or more, insufficient lip seal toughness can result in deterioration, leading to maintenance concerns. Add in the chlorinated additives used in many cutting fluids and it’s clear that lip seals present a multi-faceted challenge for material scientists.
To counteract this, Renishaw worked with their supplier for more than 5 years to develop the DuraSeal™ material specifically for the FORTiS encoder’s lip seals. This robust material reduces seal degradation, and at the same time provides a tighter seal around the readhead blade. The improved sealing reduces air leakage from the air purge, resulting in lower operating costs and greater system longevity. Compared to conventional enclosed optical encoders, the air purge requirements for the FORTiS encoder are reduced by 70%.
As Corrie continues: “We did a lot of work on the lip seals. To provide an idea of how well it works, when you put an air purge on competitor systems they will leak air at between 7 and 10 litres per minute, whereas the FORTiS encoder will leak air at 2 litres per minute. This is a considerable reduction in purge air consumption and correspondingly facilitates an energy saving over the lifetime of the machine. To achieve even greater improvements, we’re working with OEMs to optimise the air purge efficiency by recommending lower air purge pressure on axes mounted further from the machine chamber. The result is that the machine user can get all the reliability benefits of a clean air purge, but at a greatly reduced cost.
In the worst case, if something happened to cause the encoder to be accidentally flooded with coolant or oil, Renishaw have another ace up their sleeve. “The readhead is completely sealed” says Corrie, “so if the encoder were to be flooded, it can be removed, the scale and readhead can be cleaned and then the encoder can be refitted to the machine. To prove how good the sealing is, we even took a readhead and threw it into the famous lake in front of Renishaw’s Mill building, in the height of winter, to see how it would react. Despite air temperatures down to – 7⁰C, the readhead still performed perfectly after being submerged in the lake for 2 days!”
Renishaw may be the first to have broken the ‘glass ceiling’ and they did it with steel (scales) and determination.
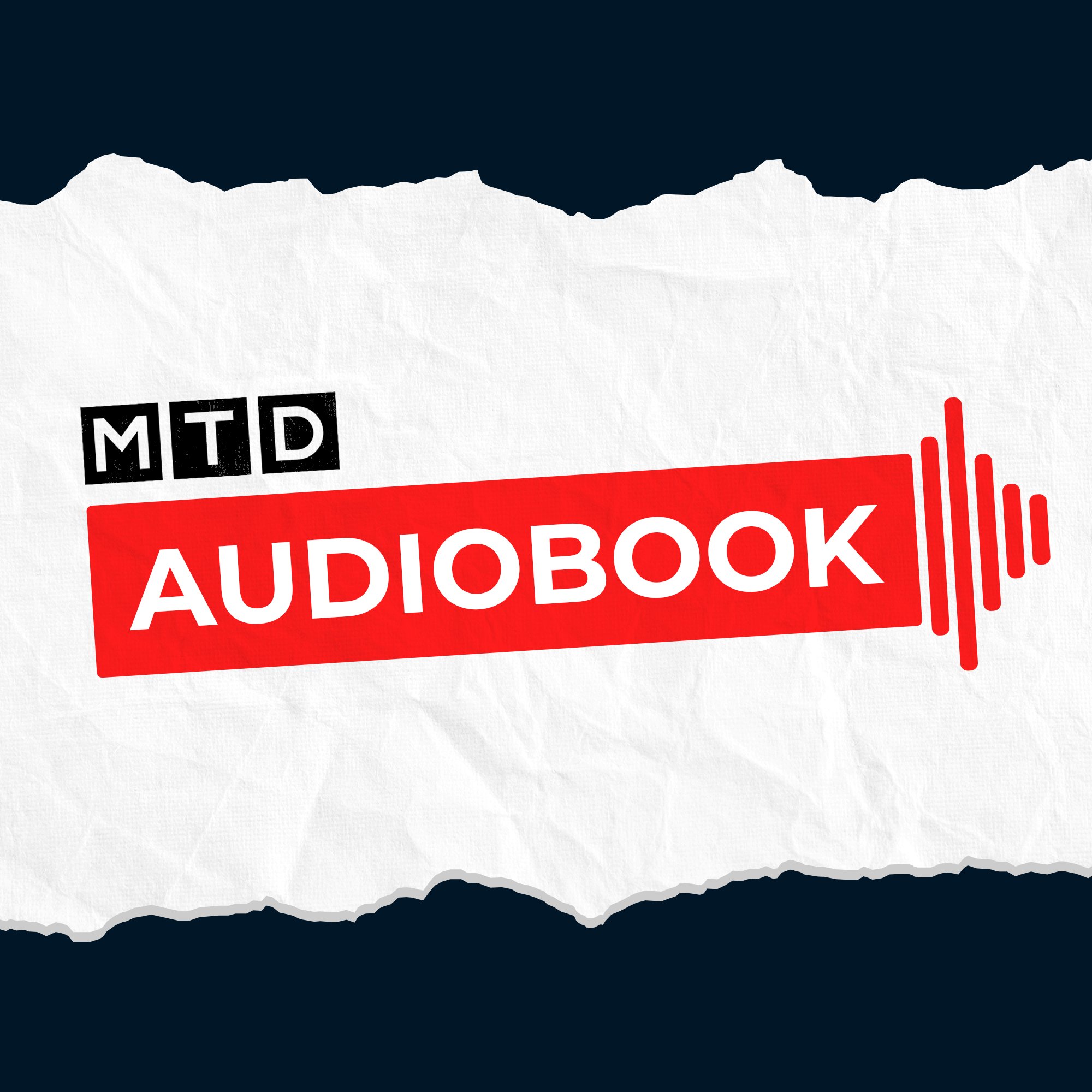
Subscribe to our Newsletter today!
Stay up to date with the latest industry news and events.
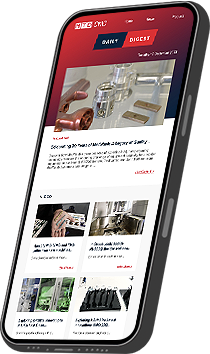