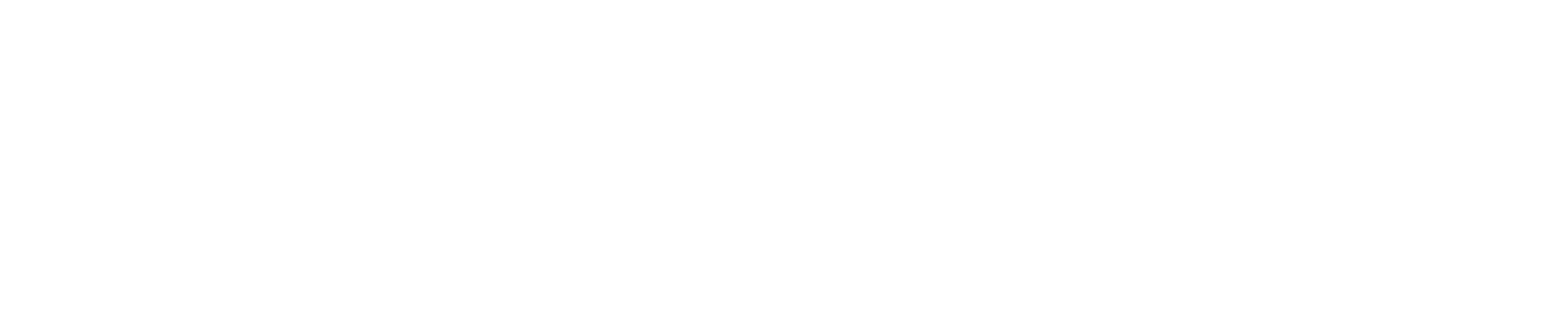
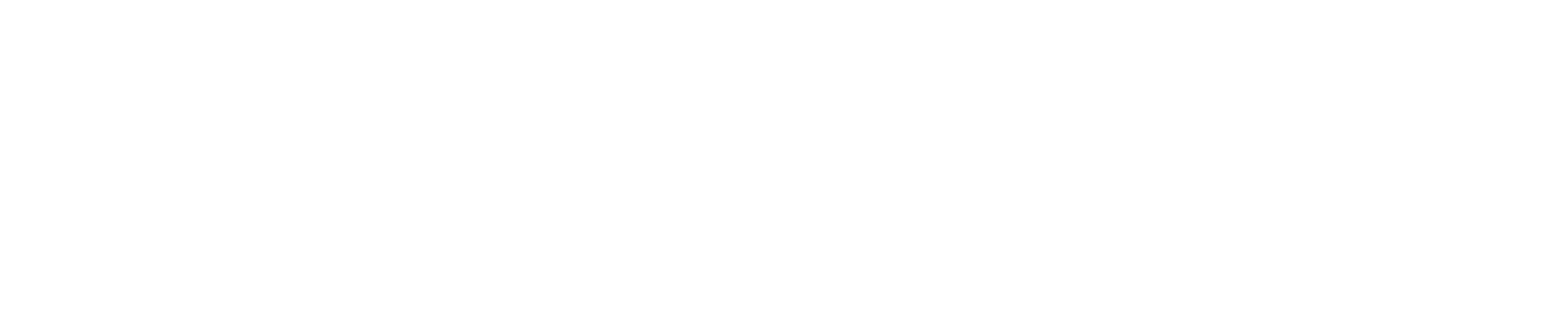
Prima Innovations are shear class
In the November issue of MTD magazine, we reported on our visit to the Prima Power factory in Seinäjoki in Western Finland. We toured the manufacturing facility and were absorbed by the efficiency of the plant. In this issue, we take a closer look at the ‘Tech Centre’ – the showpiece for the developments coming out of the Scandinavian facility of Prima Power. By Rhys Williams
In 2022, the MTDCNC crew were lucky enough to get an invite to the Prima Power headquarters in Turin. Like the architecture of northern Italy, that facility was incredibly impressive with multi-axis lasers, additive manufacturing and automation. It was truly like nothing we had seen before – that was until we landed in Prima Power’s Seinäjoki plant in Finland.
In our November issue, we noted how the state-of-the-art 20,000m2 Seinäjoki factory was the daily commute for 250 staff while another 150 employees would primarily work remotely from other parts of Finland or serving customers around the globe. The largest department in the Seinäjoki company is production, employing 40% of the total staff (including the installation group and customer training). The second largest department is R&D, pushing the boundaries of product development. The tech centre is the epicentre of that innovation.
As the centrepiece of the state-of-the-art Seinäjoki facility, the 7000m2 centre demonstrates a complete armoury of solutions. During our visit, this included the Laser Genius+1530 with the PSR (Picking and Stacking Robot) and the new EBe 2720 servo-electric driven panel bender that demonstrates the company’s latest API technology. The EBe 2720 panel bender in the facility forms part of a complete PSBB (Punch, Shear, Buffer and Bend) automation solution in the Tech Centre. At one end, this colossus automation system that stretches some 40m, has the Combi Genius CG1530 laser and punching machine that is fed by the Night Train Genius automation system that has more than 60 storage cassettes – each able to hold 3 tons of sheet steel.
Completely configurable to the demands of the end user, the impressive Night Train has the CG1530 at one end and at the other, a PSBB line including a Shear Brilliance 1530. Sheets fed to the Shear Brilliance 1530 are then transferred to a buffering station where sheets and parts can be removed, added or flipped over for transfer to the final station, the EBe 2720 panel bender. During our visit, the exceptional level of flexibility and automation was demonstrated with a complete kit of parts being manufactured for an office furniture assembly.
Taking a walk around the Tech Centre with Prima Power UK General Manager, Mr Barry Rooney, he showed us the new EBe2720 (Express Bender) servo electric panel bender. The standalone EBe2720 is one of several models that vary to support different sheet dimensions. Capable of loading automatically from the loading table with precut blanks or being connected to a PSBB (Punch, Shear, Buffer and Bend) for complete automation, the EBe2720 has evolved to deliver low running costs, low maintenance requirements and most importantly in today’s current climate, very low energy consumption.
With the machine having a seamlessly endless number of options to maximise flexibility, the EBe2720 offers a complete array of tooling designs to accommodate complex profiles. Here, the additional tools and bending blades for small and/or special bends allow small parts to be bent and corrected from a sheet with particularly narrow channels. It is here that the Advanced Profile Inspection (API) technology, a relatively new advancement from Prima Power stands above the innovation of its rivals.
Describing the API technology, that is available on a number of the Prima bending machines, Barry Rooney says: “The API system is not completely new, but it is well proven. The API system has a light source and a camera, it uses the light source to see the shadow of the part very accurately. It determines from that what the measurement actually is and then corrects the part. It is like a visual recognition where the machine can identify a measurement and apply a correction. When the system applies the correction, it then watches for spring back and other deviations, so it may do two or three corrections before it gets the right angle. Once it has that angle, it knows what the cumulative correction factor is – and it uses a correction factor again for the next bend. So, it may take two or three strikes at the first bend and the intelligent system will then apply the correct K Factor (ratio between material thickness and the neutral fibre axis) to subsequent bends. When it comes to the second bend, the system intelligently knows the K Factor, but still measures the bend. The time it moves on to subsequent bends, the machine intelligently knows exactly what factors to apply. Once this is in place, an operator can set the machine to check every fifth or tenth part, for example, to ensure it is adhering to quality-control factors. Our system is unique, other solutions may use a process that checks the measurements, but these rival systems don’t learn from the material and processes. We have a patent on this technology, which can measure and correct the part in real-time.”
Alluding to the UK customer uptake for machines with these new features, Barry says: “We have a lot of customers that want the API technology for its automated quality assurance whereas the DNP is a game changer for companies producing small, narrow profiles such as frameworks and edgings alongside other, larger parts. Other features that have been added to the machine are typically generational updates such as the control system and process optimisation.”
Shear Brilliance
Upstream from the EBe2720, is a buffering in balancing station. Here, parts can be removed, added or flipped over before processing on the EBe2720. This balancing station is necessary for the technical centre, as upstream from the EBe2720 is the Shear Brilliance SB1530 – a punching and shearing machine that can churn through the work with a strike rate of 1300 holes per minute.
Launched at the Euroblech exhibition last year, the Shear Brilliance machine in the tech centre has 30 turret stations, 30-tonne punching force and a staggering 210m/min axis speed. As Barry adds: “Both the Shear Brilliance and Shear Genius are machines that are so quick, they are typically embedded with our automation solutions. You have to have automation for the high number of parts that can be produced in such a short time – otherwise, customers would be continually loading and unloading material, so the machines are designed and optimised for an automated environment.”
“As our high-performance machine, the Shear Brilliance can punch 1300hpm at a 1mm pitch and has a 30 station turret. This exceeds the 16 and 20 stations on the Shear Genius machines. On 16-station turrets, a large index tool and/or multi-tool can be allocated to each position whereas on the 20-station turret, only every other position can accept an indexable multitool. However, on the 30-station turret on the Shear Brilliance, we do things differently. We have a larger number of stations and every other position will be up to size D indexable multitool and the smaller positions accommodate single tools, however, as with the 20 stations on the other machines, we can put multi-tools in the small positions.”
“We can hit the correct tool as the intelligent RAM will work with the multitool to select the correct punch inside it. The intelligent RAM and an indexing multi-tool will work together to optimise positioning and maximise productivity. A fixed non-indexable station can also accommodate a multitool – you may not be able to turn the tool, but you can turn the RAM and this will select whichever tool it needs. The overriding aim is to create optimal flexibility for all scenarios, thereby eliminating tool changeovers except for sharpening. On many of our competitor’s machines, they don’t have this flexibility so they need to frequently change tools. Some machines rely on tool changing, or tool changers to create the capacity – on our machines, the tooling is in the turret at all times and ready for use. This means we can sit with customers and work out what their production requirements will be and set up the turret around the customer.”
The Brilliance and the downstream EBe2720 are both fed by the Night Train automation system. Discussing this, Barry adds: “On the system in our Tech Centre, the Night Train works with our TULUS user interface software and the NC Express CAM software. TULUS is the user interface and office software that comes in many guises, so customers can select production and process monitoring, it can be interfaced to an ERP system via the TULUS office that offers different levels of connectivity. TULUS can work with an ERP system to do all the scheduling and the programming, so when it comes to production – everything has been done and the CAM software has prepared all of the parts and the nests.”
“The Night Train and connected machines interface into that system and it will then know what parts it will produce on specific dates and times. The system can even be set to schedules where it can run filler parts in between production runs to maximise utilisation and minimise scrap. You can literally automate the system to connect to the customers’ ERP and the CAM software and TULUS can take care of everything from scheduling and nesting to material management, process tracking and production reporting. Furthermore, the Night Train is a storage system – so it can drastically improve factory layout and inventory management. We have one customer that has bought the Shear Genius and he has opted for a tower system, as this will take all of his material off the floor and optimise his floorspace.”
Set parallel to, and working in conjunction with the Night Train was the Combi Genius 1530. Utilising the same technology as the punching machines in the Prima Power portfolio, the CG1530 incorporates indexable forming, tapping and marking to increase process possibilities. The fully servo-electric machine is equipped with a 3 or 4kW fibre laser head and this enables the CG1530 to utilise the laser to replace conventional slitting tools to increase material yield using common edge lines, or allow more complex geometries to be cut. “The Combi Genius is an extremely popular machine due to its flexibility and capability, which is emphasised in the configuration of the tooling turret.
Standing alongside the Combi Genius 1530 in Seinäjoki was a 2D Laser Genius LG+1530. We reported on this high-performance 2D fibre laser machine during our visit to Prima Power Turin last year. However, the Laser Genius LG+1530 in Seinäjoki was connected to the latest Picking & Stacking Robot (PSR). As Barry continues: “The PSR isn’t anything new for our company, but the PSR connected to the Laser Genius+ has been newly developed for that machine. Essentially, the materials are sorted and passed through the tower and then out to a station where parts are picked and stacked from laser-cut sheet. What we are doing is taking the cut sheets away from the system. This works outside the laser, so the laser can continue cutting whilst the PSR sorts the components, takes the skeleton sheet back to the tower, and then gets ready for the next sheet. If there is any issue that prevents a part from being lifted from the skeleton, the intelligence of the system sees this as it detects the sheet being lifted with the part. If the part does not separate from the skeleton, the PSR will shake the skeleton to separate the part. After a preset number of attempts, if the part is not separated from the skeleton, the PSR will move on to the next part – but the machine will know that the part has not been cut correctly and it notifies the operator that the part is still in the skeleton.”
The Future
Looking to the future, Barry says: “The current trend in the global marketplace is a scarcity of manpower, skilled manpower is even more scarce. Furthermore, energy and raw material costs are increasing and the quality of the material supply isn’t necessarily what it used to be. We are incrementally removing the need for highly skilled staff to alleviate our customers of this very real concern. Our full range of integrated solutions optimise processes, automates production, enhance efficiency, and support growth through modular and scalable solutions. Our technology is continually being developed to be more environmentally efficient whilst delivering productivity and cost benefits – we have been at the forefront in delivering technology to support these market requirements for more than a generation, and as you can see, this pace of evolution is only accelerating.”

Subscribe to our Newsletter today!
Stay up to date with the latest industry news and events.
