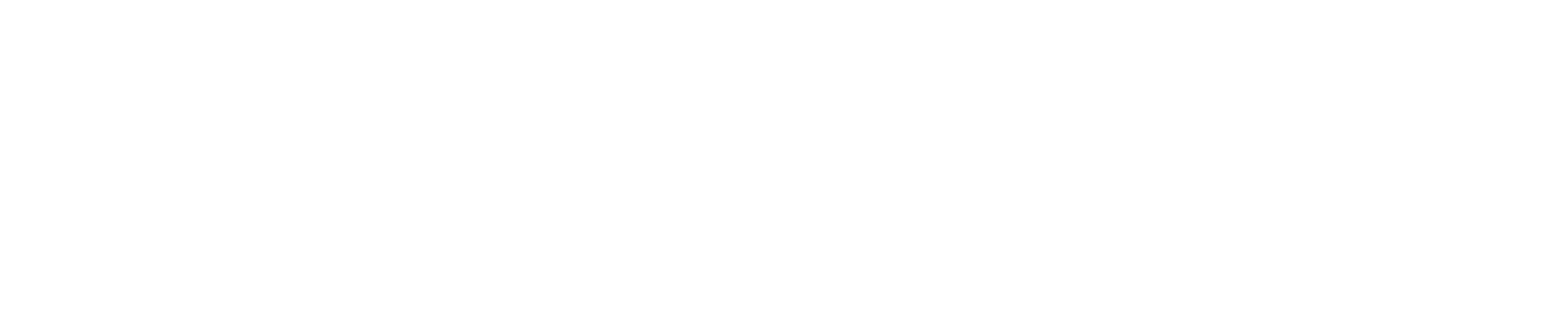
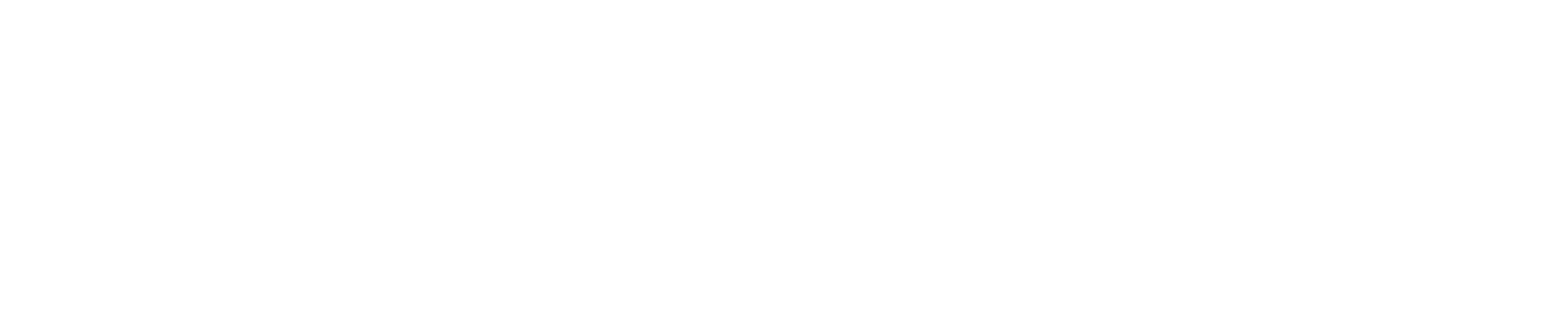
NCMT celebrates 60th anniversary at MACH 2024
NCMT is celebrating its 60th anniversary this year. In 1964, it was one of the first companies to sell CNC machine tools into the UK and Irish markets when it won the sole agency to sell and service Makino machining centres. Twelve years later, a second agreement was reached with Okuma, another Japanese manufacturer.
In 2005, Makino-NCMT Grinding Division was established to develop and sell throughout Europe Makino machining platforms for creep-feed VIPER grinding of nickel alloys. Since 2015, NCMT has also been the Europe-wide agent for photo-activated adhesive workholding systems manufactured by Blue Photon in the US.
NCMT has now signed an exclusive distribution agreement with Tritone Technologies, an additive manufacturing (AM) technology specialist in metal and ceramic applications. Typical AM parts will be available with representation on Stand 130 in Hall 19.
Rigid, thermally stable construction protects the Okuma Genos M560-V-e VMC from deformation, resulting in high machining performance for an entry-level machine. At the show, the 3-axis machine will be equipped with a Cellro X20 robotic.
The M560-V-e has a 1,050 by 560 by 460mm working envelope and a maximum table load of 900kg. The 15,000rpm BT40 spindle moves in the X and Z axes, with the table moving in Y. A 32-position tool magazine is provided. Software can be added, including Machining Navi to minimise chatter by finding the best cutting conditions. It employs a microphone to detect the onset of vibration and feeds information back to the control.
The popular Genos M460-5AX VMC will also be at MACH and will be one of the first Okuma machines to be exhibited in the UK with the manufacturer’s new OSP 500 control. It was the original 5-axis machine in Okuma’s economical, series-built Genos range. The trunnion with a rotary table and 5-axis simultaneous control gives the machine the ability to produce highly complex components. The BT40 spindle is rated at 15,000rpm 22kW, which is served from a 48-position tool magazine. Features such as Okuma’s 5-axis auto-tuning system that accurately fine-tunes the geometry of the machine for ultra-high precision, and Okuma’s Absoscale linear encoders in the X, Y and Z axes, are all part of the standard specification.
The competitively priced Genos L3000-e-MYW lathe from Okuma will be at MACH, fed automatically with shaft-type parts by a Cellro CoMate cobot. Maximum turning diameter is 300mm and the rotational speed of the 22kW spindle is up to 3,800rpm, all in a compact footprint of 2.5 by 1.9m. The turning centre has a sub-spindle and a 12-station turret with Y-axis and live tooling.
With a 240-degree swivelling B-axis head and HSK-A63 (optionally Capto C6), 12,000rpm 22kW spindle for turning or milling components up to 1,500mm between centres, an Okuma MULTUS U3000 multi-tasking lathe will be demonstrated on the stand. The tool magazine has 40 stations as standard but is optionally available with a capacity of 80 tools.
The machine is fitted with Okuma’s linear scales for high-accuracy positional feedback. Servo motors deliver feed rates of up to 50m/min in the X and Z axes, 40m/min in the 250mm Y-axis. Together with the C-axis on the main spindle, the machine is capable of fully interpolative, 5-axis (X, Y, Z, B, C) machining of freeform surfaces.
Next-generation Okuma control
The OSP-P500 CNC system, manufactured in-house by Okuma along with virtually everything else on its machines, will be on show for the first time in the UK. It combines highly productive and precise machining with ease of use, energy efficiency and safety features to protect against cyber-attacks. Particularly well suited to high-speed machining applications and achieving top-quality surface finishes, the CNC has twice the computing power of conventional machine control, shortening cycle times by up to 15%.
An on-machine Digital Twin facilitates high-precision simulation of machining processes, reducing set-up times and speeding production. By performing these simulations on the machine itself, production can start immediately afterwards.
Ultra-fast 5-axis
In a space on the shop floor of less than 3.3sq/m, the N2-5XA horizontal machining centre from Makino is capable of very high-speed machining of components up to 300mm diameter by 270mm high and weighing a maximum of 30kg, including fixtures. The machine is ideal for fully interpolative, 5-axis machining of complex components.
Within its working volume of 300 by 300 by 230mm, the horizontal spindle design ensures that gravity assists swarf removal, prolonging tool life by avoiding the recutting of chips that are frequently harder than the parent material.
The show will also mark the first UK appearance of the Makino DA300 5-axis, trunnion-type, VMC configured as a production cell with 40 pallet positions on five levels for extended periods of lights-out running. Maximum workpiece size is 360mm diameter by 300mm tall for the eight positions on the top row of the store and 280mm tall on all other levels. Maximum payload per position is 60kg. The automation package includes an integrated chuck, pallet interface and Single Pro6 graphically-driven cell controller, via which it is easy to manage the machine and pallet system.
Makino’s U6 H.E.A.T. Extreme wire-cut EDM centre will be on show. In addition to using standard wire from 0.1 to 0.3mm, it is optionally possible to run the largest diameter wire of any machine on the market at 0.4mm. The wire is coated and distinct from the uncoated brass wire that is commonly used in industry.
Part of Makino’s popular U-Series wire EDM machine platform, the U6 H.E.A.T. Extreme uses Bedra copper core wire with a double-layer coating having controlled zinc donation. It has been optimised for use with Makino’s generator and is exclusive to the new machine, promoting fast cutting at a reduced wire speed, leading to lower manufacturing costs. Areas of application include aerospace and medical component machining, separating additively manufactured parts, machining tall moulds and dies and tackling tough nickel alloys.
The Makino EDAF3 die-sinking EDM machine on the stand features a rigid, precise structure and integral thermal cooling of the Y- and Z-axis cast components to ensure long-term accuracy. Table size is 700 by 500mm and the dielectric reservoir is built into the base casting of the machine to improve stability and minimise the footprint. The machine uses Makino’s latest Hyper-i control, which can be factory-ordered mounted on either the left or right, facilitating easy integration of one or more machines with a variety of commercially available electrode and work pallet handling robots.
Exhibited on the stand will be the Blue Photon photo-activated adhesive system. The method is ideal for securing awkwardly shaped parts to allow maximum access to tools for tight-tolerance machining or inspection. The process involves applying an adhesive that is cured by ultraviolet light via an LED spot-curing system. After machining is complete, the adhesive contact points can be sheared to free the workpiece by rotating the gripper pins in the fixture plate with a spanner. The residual adhesive can subsequently be removed by the application of hot water.

Subscribe to our Newsletter today!
Stay up to date with the latest industry news and events.
