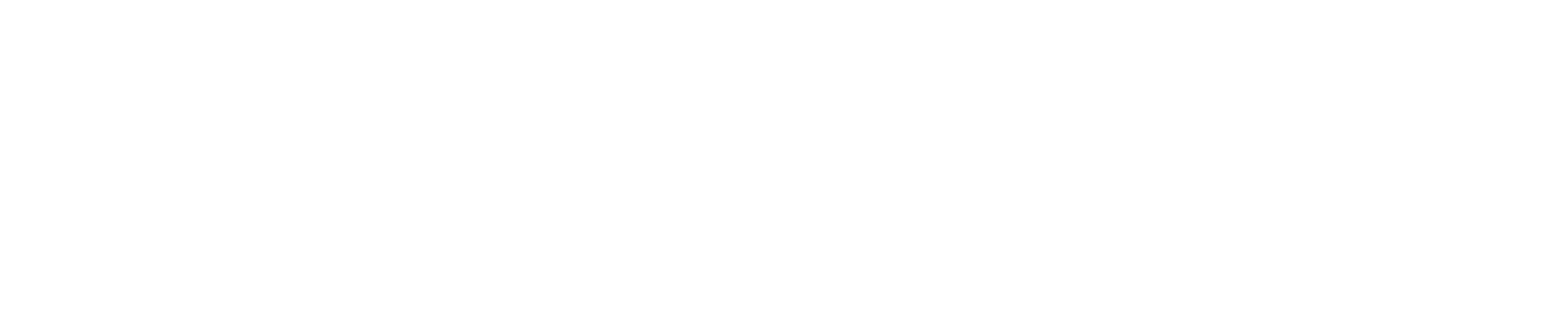
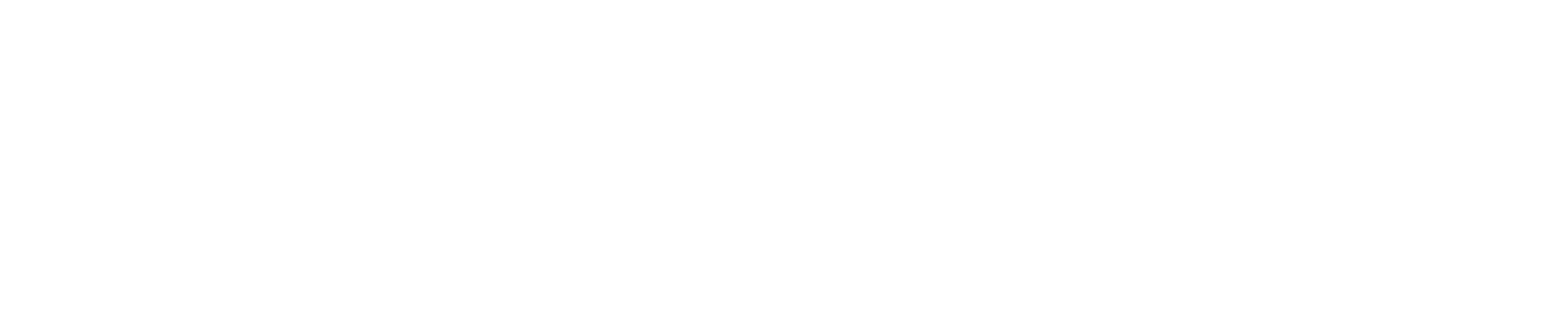
Insert evolution continues to take shape
The introduction of the ISCAR HELIMILL in the 1990s marked a significant milestone for milling tools. It revolutionised the design of milling tools with indexable inserts, establishing a new approach that would shape the industry for years to come.
This breakthrough was achieved using a parallelogram-shaped carbide insert, featuring a helical cutting edge formed by the intersection of the insert’s helical side and shaped top surfaces. The HELIMILL concept offers several advantages.
Firstly, the consistency of the rake and relief angles along the insert cutting edge when mounted on a tool reduces cutting force variations and ensures a smooth cutting action. Secondly, the uniformity of the insert cutting wedge enhances its strength. Lastly, the helical cutting edge’s proximity to the imaginary cylinder generated by a rotating tool improves accuracy compared to the straight edge found in previous-generation milling inserts. These advancements elevated milling performance to new heights.
Over the years, continuous improvement has led to significant changes in the classical HELIMILL inserts. The helix of the cutting edge has become more aggressive and the top surface topology has become more intricate. Combined with advanced carbide grades, these new designs have ushered in a new level of performance. However, the parallelogram insert shape limits the number of indexable cutting edges to two.
To maximise the efficiency of cemented carbides, a new round of insert development was initiated. The successful adaptation of the helical cutting edge to triangular inserts addressed this limitation. The triangular insert concept not only provides three cutting edges but also offers additional benefits. When compared to other shapes with equal cutting-edge lengths, the triangular shape provides a wider central area. This allows for an increase in the central bore size, enabling the use of a clamping screw with a larger thread. As a result, the insert security is strengthened, contributing to the overall durability of the milling tool assembly. Additionally, the triangular shape enhances the ramping-down cutting capability.
Overall, the introduction of the ISCAR HELIMILL and its subsequent advancements have advanced the milling tool industry. The use of helical cutting edges and triangular inserts has significantly improved performance, accuracy, and durability, pushing milling capabilities to new levels.
A proximate successor to the HELIMILL is the HELI-3-MILL, a family of milling tools introduced by ISCAR in the last decade, featuring triangular indexable inserts. The advantages of the ‘helical triangle’ highlight why this family has gained popularity in the market. However, it is important to note that this does not mean the triangle shape will completely replace the traditional parallelogram contour with helical cutting edges any time soon. The parallelogram shape still possesses its competitive edge.
Paradoxically, the narrow width of the parallelogram-shaped insert, which is considered a drawback when compared to the triangular shape, also offers certain advantages. Firstly, a narrower insert allows for an indexable design suitable for smaller tool diameters. Secondly, this insert geometry reduces the depth of the chip gullet, strengthening the cross-section of the tool body. This feature is particularly important for extended flute cutter designs where higher strength and rigidity of the body are crucial.
The parallelogram insert structure also permits increased corner radii. Additionally, the classical shape is well-suited for high feed milling (HFM) inserts, which can be mounted in existing pockets, effectively transforming a 90-degree tool into an efficient HFM cutter. Moreover, the ‘helical parallelogram’ has a smaller overall length compared to the ‘helical triangle’ for the same cutting length. Therefore, it would be premature and incorrect to dismiss classical parallelogram inserts.
As a result, the development of 90-degree indexable milling cutters harmoniously combines both approaches, utilising both triangular and parallelogram-shaped inserts. While the triangular insert concept dominates modern designs, the parallelogram insert principle remains relevant. The HELIMILL platform continues to be updated with new advantageous products. ISCAR’s recently developed products related to milling cutters with parallelogram-shaped inserts demonstrate that the traditional design approach remains effective and capable of meeting the demands of modern manufacturing. Milling high-temperature superalloys and titanium (ISO S group of applications), as well as difficult-to-cut austenitic and duplex stainless steel (ISO M group), present challenges. Effective coolant supply, particularly pinpointed high-pressure cooling (HPC), can significantly reduce the heat load on the cutting edge, enhancing lubrication and chip removal.
This, in turn, leads to higher cutting data and enables larger radial engagements, resulting in a higher metal removal rate (MRR). Moreover, HPC facilitates the production of tighter curled chips, allowing for tool designs with smaller chip gullets and higher tooth density. Taking these factors into consideration, ISCAR has expanded its HELI2000 family (the latest version of the HELIMILL) by introducing new tools that incorporate the HPC option within the tool body. The design of these tools has been optimised using computational fluid dynamics (CFD). They are available in both integral-body configurations and as relatively small-sized exchangeable heads with indexable inserts, which are compatible with ISCAR’s modular systems MULTI-MASTER and FLEXFIT.
HELI2000 integrates the HELIMILL and HELIPLUS families, combining their latest developments into a single portfolio. This includes the introduction of two new highly efficient carbide grades: IC5600, designed for machining steel (ISO P group), and IC716, specifically tailored for cutting titanium. Additionally, the insert range has been expanded with new cutting geometries. This includes inserts with a high positive chipformer for milling titanium, chip-splitting cutting edges for productive roughing and other designs. Furthermore, the range now includes inserts with reinforced cutting edges for high feed milling of hard materials up to HRC 60 hardness.
These new products are also part of ISCAR’s HELIALU family, which consists of milling tools with parallelogram-shaped inserts for machining aluminium alloys (ISO N group). The expansion of this family includes indexable endmill heads with threaded adaptations for both MULTI-MASTER and FLEXFIT systems providing the option for HPC. The screw-in design configuration of the heads significantly enhances the customisation capabilities of HELIALU tools, allowing for a wide range of MULTI-MASTER and FLEXFIT shanks, adaptors, extensions and reducers to be utilised. Therefore, the development of the ‘helical parallelogram’ has not ceased, and the traditional HELIMILL continues to gain momentum. This development follows a gradual upward helix, revisiting past turns but at a more advanced stage, much like in dialectics.

Subscribe to our Newsletter today!
Stay up to date with the latest industry news and events.
