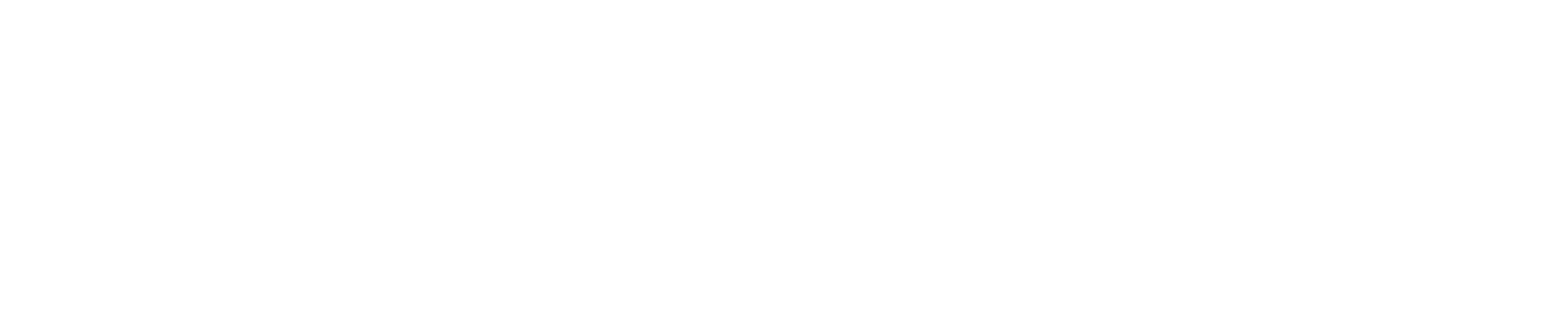
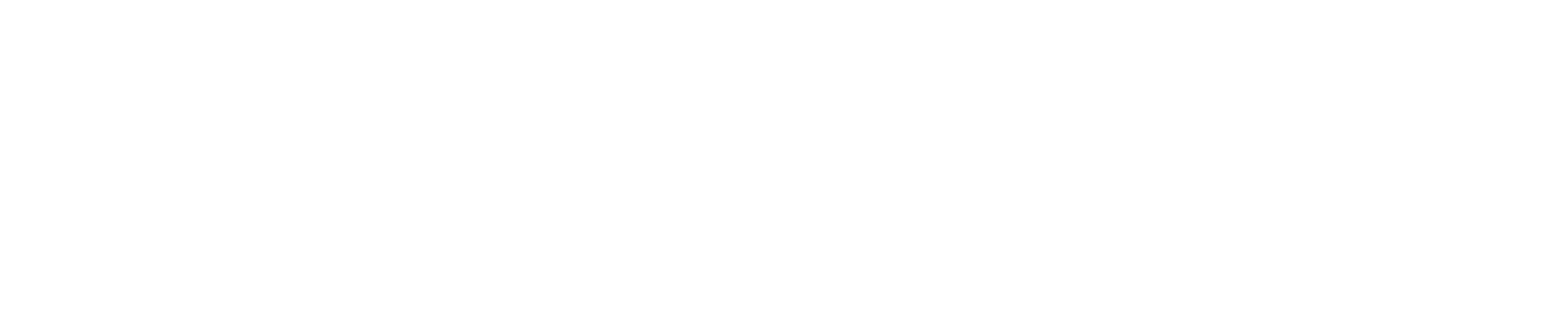
Se 1 | Ep 13
In safe hands with CMZ
Founded before the First World War, Tybro Bros (Sutton in Ashfield) Ltd has evolved over the last century. Formed in 1914, it has progressed from a business with motor and electrical engineers to precision engineering. The company has a reputation for its excellent standards – something underpinned by its investment in machine tools from CMZ.
A family business spanning more than four generations, the Kirkby-in-Ashfield company is a typical subcontractor that serves all industry sectors. With a customer base that boasts brands like Thorntons, OTIS, the UK Atomic Energy Authority and Transport for London, the company was instrumental in the redesign of the stop switches on the London Underground and the contract remains in place more than 40 years later. In fact, it was the father of the current Managing Director, Mandy Tyler who designed and developed the London Underground stop buttons.
Describing the business, Mandy Tyler, Managing Director of Tybro Bros Ltd says: “We specialise in machining, fabrication and assembly; manufacturing components for critical industries – we push the boundaries of those industries. We are producing components that have never actually been made before from drawings that have never been designed before, and that is why there is so much skill involved in our business. We also need the machinery to support our skilled engineers.”
The company purchased its first CMZ machine in 2011 and the relationship has continued from there, as Mandy adds: “The first machine was a single spindle lathe and as the years have progressed, we have gone from single spindles to sub-spindles and Y-axis machinery. This progression has been based on the type of components that we manufacture.”
Adding to this, Mandy says: “We deliver to key industries that demand critical parts, so we absolutely need the machinery to be robust and reliable for us to deliver to our customers on time. I have great confidence in the CMZ machines as they hold tolerances very well – and this is critical, as the drawings we work to have very tight tolerances. We machine a variety of materials from plastic through to mild steel and superalloys, and when it comes to materials like Inconel, it is very handy to have the extra power of the CMZ TA Series.”
Mandy continues: “Since investing in our first CMZ machine in 2011, we found that the brand has just worked for us, so we have invested time and time again. Our most recent purchase was a CMZ TD35 turning centre that was bought purely to keep up with customer demand, as we are busier now than we have been in the last six years.”
The TD35 is a CNC lathe that allows multiple configuration options that can be adapted to the demands and particularities of each production process. All models have a turret with a built-in motor offering 12,000rpm driven tools and integrated spindles. Laser compensation is also a standard feature on all TD Series machines with automation of both short and long batches possible via the GL20 and GL100 Gantry robots that will lift to 100kg.
“One of the unique features of the CMZ machine is the turret design. It has a 12,000rpm driven motor, which has 13kW of power. So, when you cut materials like nimonics, the Y-axis is like a machining centre with incredible power. Tybro now has four machines from CMZ and this is due to the accuracy and performance over a prolonged period. This is important to Tybro, as the company specialises in machining difficult materials for critical industries,” says a member of the CMZ team.
As Mandy concludes: “As the demands have grown in our turning department, and since we bought our first CMZ machine, our machinists have found CMZ machines to be fantastic to use and very intuitive. For this reason, we have invested time and again in CMZ machines, so that we can have standardisation in our factory.”

Subscribe to our Newsletter today!
Stay up to date with the latest industry news and events.
