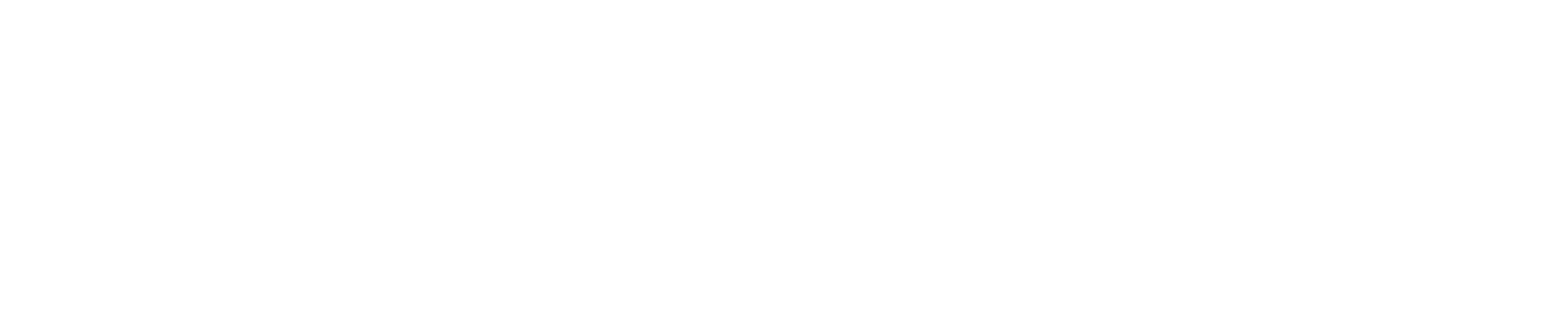
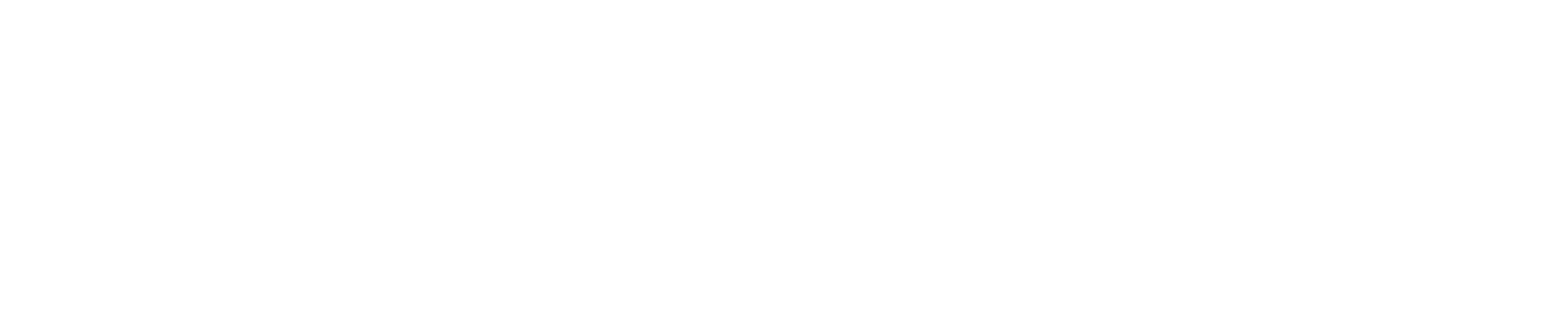
FGP Turbo’s through complex work with Mastercam
Made up of three main companies, the FGP Group is a specialist Tier 1 subcontractor that provides services from design and manufacturing to surface coating, heat treatment, assembly, inspection, testing and more. As one of the three companies in the group, FGP Systems Ltd typically produces prismatic components for the aerospace industry – it is here that the company utilises Mastercam CAM software.
Founded more than 45 years ago, the company bought its first 5-axis machine, a DMG MORI DMU 50 eVolution over 20 years ago – and 3 and 5-axis machining has since become the backbone of the Yeovil-based business. The company produces a vast array of components for aircraft and helicopters such as valve bodies, actuation parts and service components – with complex turbines increasingly becoming the mainstay of production on the shop floor.
Simon Griffiths-Hughes from FGP Systems Ltd says: “If we look back over 20 years ago, we had to stay competitive and to do that back then, the buzzword was 5-axis machining. We knew that was the future, so we decided to buy our first 5-axis machine. Our work is five-sided prismatic machining and we needed 5-axis machines to accommodate that. Since then, we have taken on more work like turbines – now we do a lot of turbines in various shapes and sizes.”
Discussing the complexities of machining turbines, Simon continues: “The complexity lies within the programming. A turbine, depending on its complexity has main blades and multiple splitter blades. This requires a lot of programming time and you must have safe and repeatable programming and machining strategies. To support what was the new 5-axis investment 20 years ago, we needed a CAM package to support that, and we chose Mastercam. We did our due diligence and went through a couple of CAM providers, but Mastercam were offering the full support we needed for full simultaneous 5-axis machining. We took the plunge straight into full simultaneous 5-axis machining from the off, and Mastercam was able to support us through that period.”
Alluding to the challenge of taking on both 5-axis machining and a new CAM system, Simon says: “At the time, we just had to get on with it, but the support from machine tool provider and Mastercam seemed to work very well – and this has grown with us as we have added to that portfolio of machines. We now have 15 5-axis machines with a total of 63 CNC machines across two sites, business has grown considerably down the years.”
Looking at how the workload has changed at Somerset-based FGP Systems Ltd, Simon adds: “If we look back 10 years ago, a customer came to us with the need to machine turbines of all different sizes and types. This ranged from scroll turbines and progressed to axial fans. The majority of those turbines at the time were cast and we were very keen to go to a billet solution, which makes it easier for us to start the process. The raw material yield from the casting is notoriously bad and if we go to billet form, it is far easier for us to work on that immediately to get a better yield and reduce cycle times. Once we machine the turbines, we can test them on-site with a spin test of over 100,000rpm.”
For the parts to perform, they have to be manufactured with impeccable precision. As Simon adds: “To get these turbines up to speed, they have to be balanced to within micrograms. If you look at a cast variant, it is very difficult and time-consuming to manufacture and balance with precision. The machining strategies we use on our CAM package, enable us to create a machining solution for titanium or aluminium turbines – and then migrate that solution across to the next turbine. The quality of our turbines is a cornerstone of what FGP Systems is about, and the CAM solution and machining strategies help with this.”
“Since we on-boarded ‘blade expert’ through Mastercam, that has taken our off-line programming time down from multiple days or even multiple weeks for complex multi-splitter turbines, down to just an afternoon’s work. It really is that simple to use. What this gives our business is improved turnaround times. The customers are always demanding shorter and shorter lead times. If we can off-line program a turbine in an afternoon rather th

Subscribe to our Newsletter today!
Stay up to date with the latest industry news and events.
