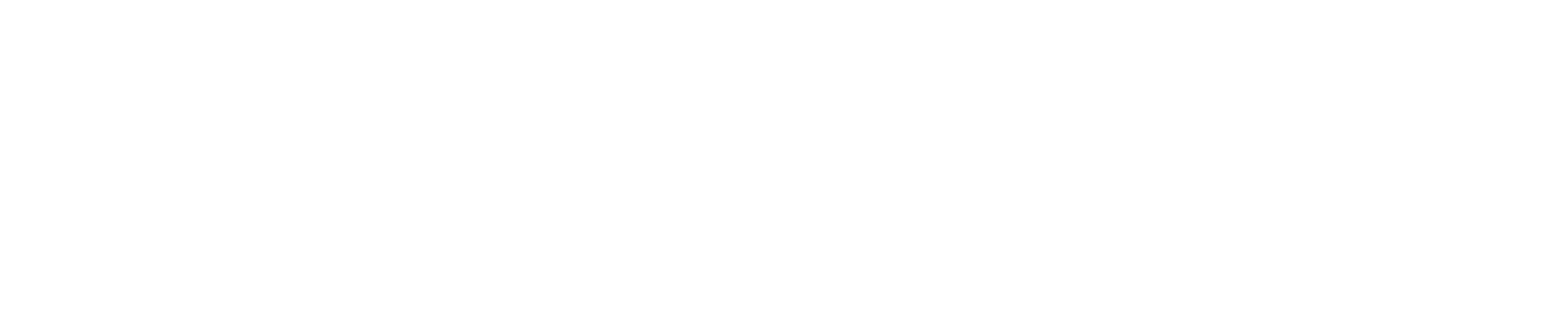
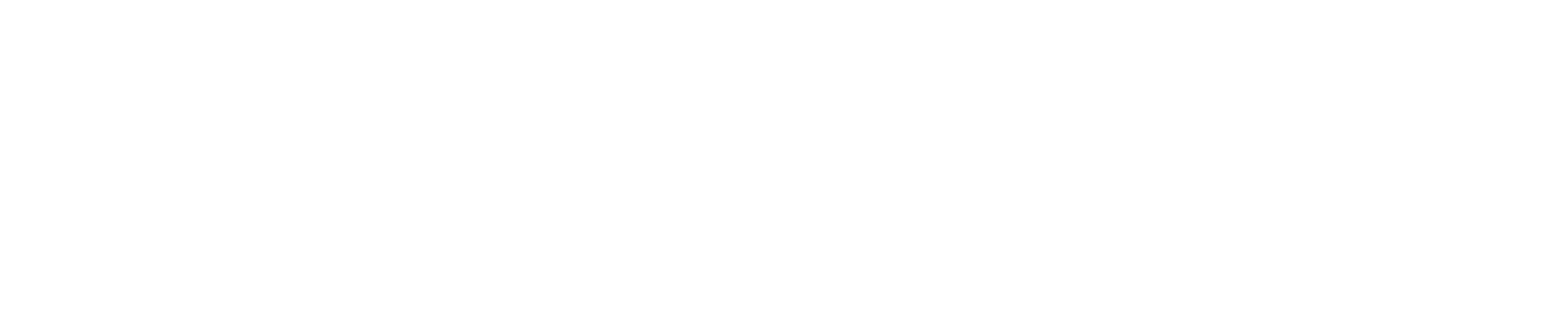
Se 1 | Ep 13
Factory 33 supported by Hurco from day one
Located in Carterten, Factory 33 is a family business headed up by Martin Krzywina, and Karina Ringer-Krzywina. With more than 10 years of experience in manufacturing precision components for the F1, aerospace, nuclear, medical and cryogenic sectors; this was immediately the target area for the engineers when they started the company in 2015. The journey started with two machines from Hurco.
Managing Director Marcin Krzywina says: “We make everything from aerospace to motocross parts and we also supply most of the F1 and Formula E Teams. These are typically high-precision critical components. The first two machines we bought were a Hurco TM8i lathe and a Hurco VMX30i machining centre. At the time of starting the business, the building was under construction, but we laid out the factory as a lean manufacturing facility.”
“We approached Hurco about a year before we decided to open the doors for business. So, we approached several machine tool suppliers but Hurco were the ones that really did take us seriously. They were on board with our concept and plans and they wanted to support us as a new business – other companies did not.”
Looking at the Hurco VMX30i machining centre, which was the first machine to land at Factory 33, Marcin says: “It’s a great piece of kit with a huge stroke in the X-axis and we have added a 4th axis unit to this machine. We have through spindle coolant and we can do a lot of great parts on this machine – it has all the bells and whistles like full probing, it has the full package. What you see with Hurco is what you get. The machine you see in the showroom will be delivered with the same specifications.”
Another machine the company specified was the full simultaneous 5-axis Hurco VMX30UDi, alluding to this, Marcin continues: “We needed this machine because our customer components were getting more complex and the 5-axis gives us the edge of making these parts quicker, more accurately and with a better finish. This is because the machine is a direct drive spindle with 15,000 rpm. Some machines are belt-driven, but this one in particular is a direct-drive machine that creates less vibration. With Hurco, the parts and the finishes are impeccable.”
The cleanliness of Factory 33 is incredible. Part of this is down to the Lean Manufacturing philosophy where every tool, collet and accessory has a storage place. However, it is also down to good housekeeping. As Marcin adds: “We have to keep our facility clean because when we are being audited by medical companies, we have to be on our best behaviour – it’s just what the industry demands. We are trying to operate on the level of Formula One. An extremely clean machine shop is our goal.”
Asking Marcin for his opinion on what makes a good machine tool, he tells MTD: “It’s all about the axes. Everything in a 5-axis machine shop is about the axes. On this 5-axis machine, we have a 250mm diameter capacity and we can get to the centre of the table rotation with only 125mm of the tool protruding from the spindle. This is excellent and ensures we will have no collisions whatsoever. When I’m looking for a machine, I am looking for the complete package – I want as much included in the package as possible. When you look at some brands, you could be missing an air gun, the coolant wash down or another feature – these are typically extras but with Hurco they come as standard.”
Alluding to what makes life easier, Marcin says: “When we are looking for machines, we want to see the retailer selling the complete package. It makes life a lot easier when everything is included – as much as it can be.” Looking at software, the Managing Director continues: “The software side of the machine also has to be straightforward. With the Hurco brand, everything is straightforward – we love the WinMAX control and the graphics. You can manipulate the graphics in any way that you want. The graphics don’t only show the solids, but also the tool paths. If you have any gouges on a component, you can go back to the control. If it’s simulated incorrectly on the control, that means you need to go back to your CAD/CAM system and fix it.”

Subscribe to our Newsletter today!
Stay up to date with the latest industry news and events.
