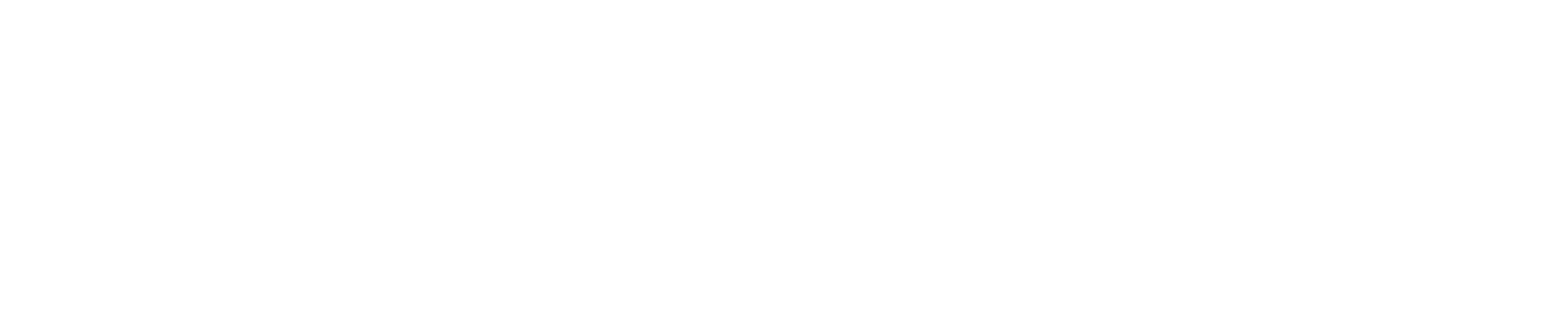
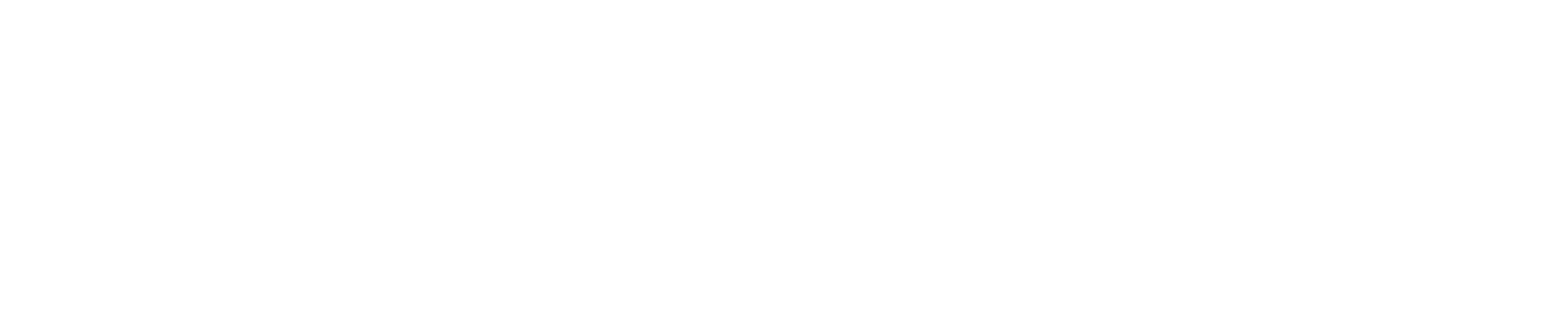
Se 1 | Ep 13
Embracing a ‘one-stop-shop’ supplier
Full 5-axis capability plays a pivotal role in Maycast-Nokes’ production processes. Situated in Halstead, Essex, the company invested in their initial 5-axis machine over two decades ago—a HAAS VF-2 vertical machining centre equipped with a trunnion unit. Sales Director at Maycast-Nokes, Mr Dave Blower explains: “This marked our first investment with HAAS. Although initially intended for a specific project, it had a tremendous impact on our entire machine shop.”
Adding to this, Dave says: “At the time, we did not possess any other 5-axis machines on-site. However, we found the transition to be seamless, and the HAAS control system proved to be highly intuitive. Opting for a 15,000rpm spindle reduced our cycle times by 50% when combined with the 5-axis.”
Since the 1950s, Maycast-Nokes has functioned as a foundry and progressively evolved into a comprehensive engineering business through gradual technological investments. Financial Director Derek Redgwell states: “Our workforce now comprises 120 individuals, including ten apprentices working across various departments.”
All ten milling machines in Maycast-Nokes’ facility are HAAS CNCs, with seven of them being UMC Universal Machining Centres. Dave proudly shares: “We purchased one of the first UMCs in the UK, and it perfectly suits the majority of our component requirements. We were so impressed that we continued to invest in them.” The UMC-750 models utilised by Maycast-Nokes boast a 15,000rpm spindle, a 40+1 side mount tool change capability and simultaneous 5-axis machining.
Dave further adds: “With each new machine, we have observed ongoing upgrades and refinements from HAAS. They consistently strive to enhance their products. For example, the door size has been redesigned to allow more natural light into the workspace, the control position has been optimised for improved user-friendliness, and the addition of a touchscreen has proven to be highly convenient.”
HAAS 5-axis machining has been enhanced with the introduction of TCPC (Tool Centre Point Control) and DWO (Dynamic Work Offsets). TCPC allows the machine to precisely control the position of the tool’s centre point, ensuring accurate machining regardless of the part orientation. It eliminates the need for manually calculating offsets, greatly simplifying programming.
DWO dynamically adjusts work offsets in real time during the machining process, compensating for any machine or fixture deflection. This capability ensures consistent part quality and reduces the need for manual adjustments or recalibration. With TCPC and DWO, HAAS 5-axis machining has become easier than ever, allowing operators to achieve intricate geometries and complex machining tasks with confidence and precision.
“We’ve just taken delivery of a UMC-500 and UMC-1000. The footprint of the UMCs is the reason we can fit so many into the workshop. With the speed of the machines, we can be more competitive in our quoting, which brings in more work, enabling us to invest again. It’s a circle which is very successful for us.”
Given the precise nature of the castings, primarily targeted for the aerospace and defence sectors, maintaining tight tolerances is paramount. Dave explains: “Each casting has full dimensional reports and needs to pass inspection before it leaves us, so repeatability is essential. The HAAS machines are great for consistency and accuracy.”
Over the years, Maycast-Nokes has nurtured a strong relationship with their HAAS Sales Manager. Dave comments: “Don Cole is always willing to visit us whenever we need anything. He has assured us of unwavering engineering support, and that is precisely what we get. We chose HAAS for their competitive pricing, but it is their exceptional service that has fostered our loyalty.”

Subscribe to our Newsletter today!
Stay up to date with the latest industry news and events.
