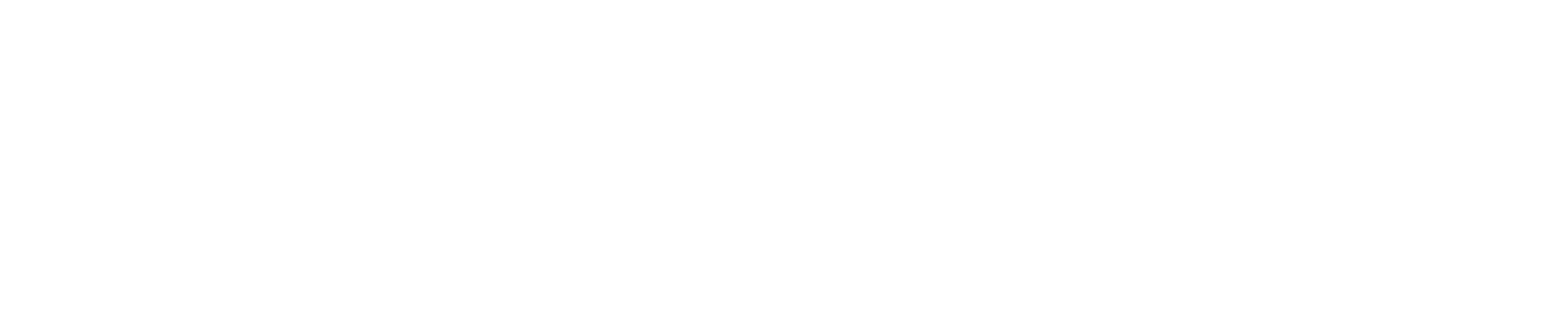
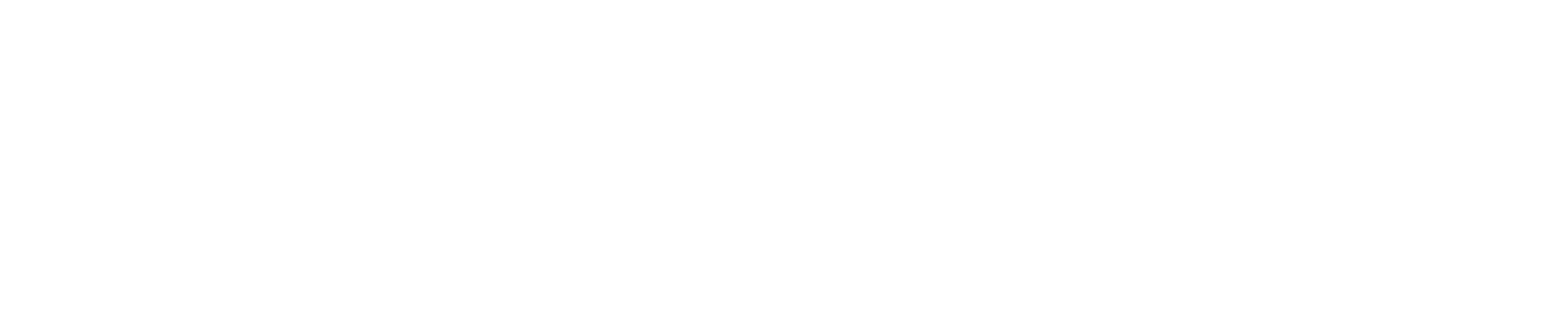
Cutting the chatter
Productive Machines is on a mission to provide a 15-minute turnaround from receiving data on its cloud-based, artificial intelligence platform to delivering a click-and-play machining protocol that enables manufacturers to machine the best part, faster, first time. John Yates talks to the spin-out team whose software-as-a-service is driving step changes in productivity and sustainability.
Walking along the second-floor corridor to the Productive Machines’ workspace in the AMP Technology Centre, Rotherham, Dr Erdem Ozturk stops to look through the window at the Rolls-Royce Factory of the Future, whose 3,000sq/m of machining workshops were his research and development laboratory for more than a decade.
Erdem led the Advanced Manufacturing Research Centre’s brilliant Machining Dynamics Technology Group, which grew in the innovation environment enabled by Dr Sam Turner and AMRC co-founder Professor Keith Ridgway which propelled the Factory of the Future to global leader in aerospace milling.
Their success was achieved by adapting and refining the fiendishly complex mathematical models of machining research pioneers like Franz Koenigsberger and Jiri Tlusty whose ideas were turned into game-changing operational manufacturing methods by their former students, and now professors in their own right, Yusuf Altintas, Scott Smith and Tom Delio.
Perhaps the AMRC’s biggest success came in 2014 when they applied these theoretical models to vibration control, cutting tool design, and residual stress management in a SAMULET project that was to revolutionise the manufacturing of Rolls-Royce aero-engine discs and shaft components.
The improvements in quality, alongside the time and cost savings achieved in the manufacture of the fan disc, have become folklore in the AMRC and the close-knit aerospace manufacturing community: a 50% reduction in cycle times and right-first-time production rates rising from 85% to over 99%. Coupled with cost-savings of £135m, this made UK jet engine production globally competitive, safeguarding 400 high-value-added jobs and unlocking a £300m investment in a North East plant.
Not content with this success, Erdem and his AMRC team, along with European partners, began harnessing the power of information technology to push the boundaries of the possible, creating state-of-the-art digital twins that combined machine tool dynamics, control loops, tool-path generation and machining processes, to boost productivity, extend tool life and eliminate chatter.
Productive Machines traces its lineage back to this remarkable pedigree. Formed in 2021, shortly before joining an elite group of start-ups on the ATI Boeing Accelerator programme – over 200 applicants from 44 countries were whittled down to just ten – the business was explicit from the start in its mission to maximise the productivity and sustainability of machine tools.
“We are using our unique digital twin to simulate millions of combinations of machine settings to arrive at the optimum feed rate and spindle speed settings for a given process before manufacturing. This eliminates chatter vibrations and provides machining optimisation, preventative maintenance and part quality that may not be achieved by a human operator even with years of continuous improvement,” says Erdem, who now leads a growing international team of machining physics developers and software engineers from their base in the heart of South Yorkshire’s Advanced Manufacturing Innovation District.
Having raised a cumulative £3m investment, the company launched its Feed Rate Calculator and Spindle Speed Calculator apps in October and November last year respectively. This was followed by an early access programme for a predictive maintenance service for spindle health monitoring in December.
In the next few months, they will be launching the fully automated cloud based system that achieves a 15-minute turnaround from receiving data on its artificial intelligence platform to delivering a click-and-play machining protocol that enables manufacturers to machine the best part, faster, first time.
“We saw there was a massive opportunity to turn our cutting-edge technology into a simple, straightforward Software as a Service (SaaS) product,” Erdem adds. “Using artificial intelligence and digital twins of the milling process, we can identify vibration-free parameters and automatically personalise the process to eliminate chatter. This opens up a future where cutting optimisation technology is accessible to all, regardless of the scale of operation”
One early client, Yorkshire headquartered Ficep UK, a leading supplier of structural steel and plate fabrication machine tools, has seen process productivity increase by 110%, with cycle times cut by 53% while reducing the magnitude of vibrations five times.
Other clients report reductions in machining design and set-up times of 20%; cycle times reduced between ten to more than 50%; operational and maintenance costs cut by 25%; and cutting tool costs reduced by 11%
An additional benefit of this software-as-a-service is the way it can dramatically reduce manufacturers’ carbon footprint. “By finally solving the age-old and frustrating problem of machine tool chatter, we calculate that our technology could save a staggering 2.5 gigatonnes of carbon dioxide emissions between now and 2050,” Erdem says. To put this into perspective, 2.5 gigatonnes is equivalent to the UK’s total carbon emissions – every factory, fire, car, flight and light – for six years.
While work continues in developing and refining the AI platform for launch in the spring, it’s fascinating to learn that an essential piece of kit in this operation is one of the oldest in the toolbox: the tap test. Used in aerospace engineering since the 1950s, the tap test relies on simple physics: the kinetic impulse of a hammer strike dissipated as vibration and sound.
However, where traditional tap testing relied on skilled individuals to interpret the sounds made by the struck object, such as a machine tool, today’s digital tap tests are much more sophisticated and precise. Instead of transmitting vibration responses to the ear as an acoustic sound wave, a digital tap hammer sends the vibration response as data to a computer for recording and analysis.
Specialist software then calculates the precise frequency response from those vibrations, considering parameters like the frequency, amplitude, and decay rate of the vibrations, and enables an exact analysis of that tool’s unique characteristics and condition.
From its origins, the age-old practice of tap testing has not only endured but has evolved into an even more powerful tool in the era of smart manufacturing, becoming a critical component of quality control, material characterisation, structural health monitoring.
“Digital tap testing, enhanced by AI, is ushering in a new era of precision and efficiency in manufacturing. It empowers manufacturers to optimise machine tool performance, reduce waste, and enhance product quality. It is democratising condition-monitoring and predictive maintenance, enabling even small-scale operators to benefit from data-driven technologies without costly investments in sensors or infrastructure,” Erdem added.
Although focused on the future, Erdem is also a keen student of machining history and one of his go-to authors is the American Quaker Frederick Taylor, best known for bringing the ‘scientific method’ to the early factory system making it more efficient and productive.
Taylor also wrote a book On the Art of Cutting Metals, published in 1907, which identified “chatter as the most obscure and delicate of all problems facing the machinist – probably no rules or formulae can be devised which will accurately guide the machinist in taking maximum cuts and speeds possible without producing chatter.”
Erdem smiles and says Taylor was absolutely right. “There were no formulae available to predict chatter vibrations until 1954 when Tlusty was able to formulate the absolute stability limit for chip width for turning operations. That meant if the process planner selected a chip width smaller than this limit, the process would be stable and there would not be chatter vibrations irrespective of the spindle speed used.”
Seventy years on since the formulation of Tlusty’s law for the identification of chatter stability lobes in turning processes, the Productive Machines team are coming very close to proving Frederick Taylor wrong by accurately guiding the machinist in making maximum cuts and speeds possible without producing chatter for machining processes.
That, I suspect, matters as much to this team as turning a profit.
It would certainly delight Keith Ridgway: “If I were starting the AMRC today, it would not be by constructing a huge machining research facility. It would be by harnessing the power of artificial intelligence, cloud-based data analytics and digital twins. Productive Machines are blazing that trail today from a small office on the very site where we set out on our journey.”

Subscribe to our Newsletter today!
Stay up to date with the latest industry news and events.
