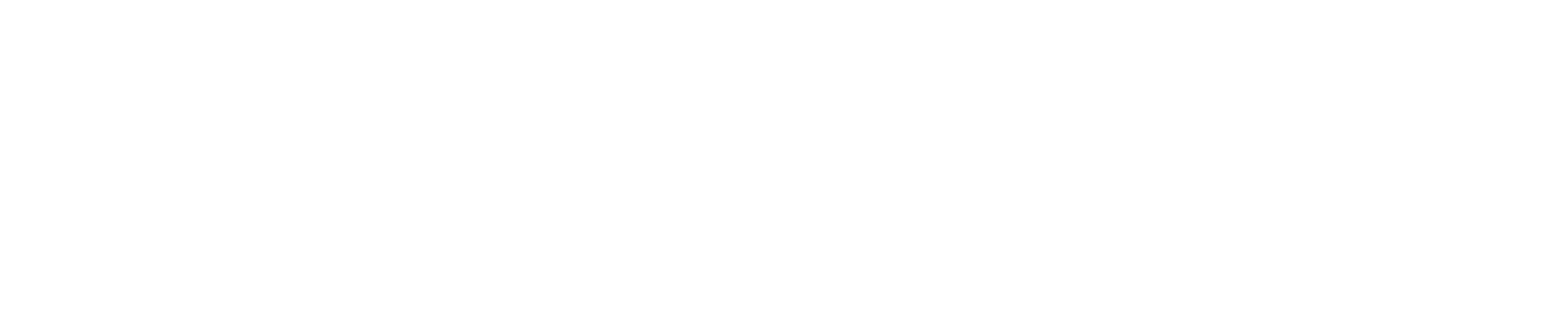
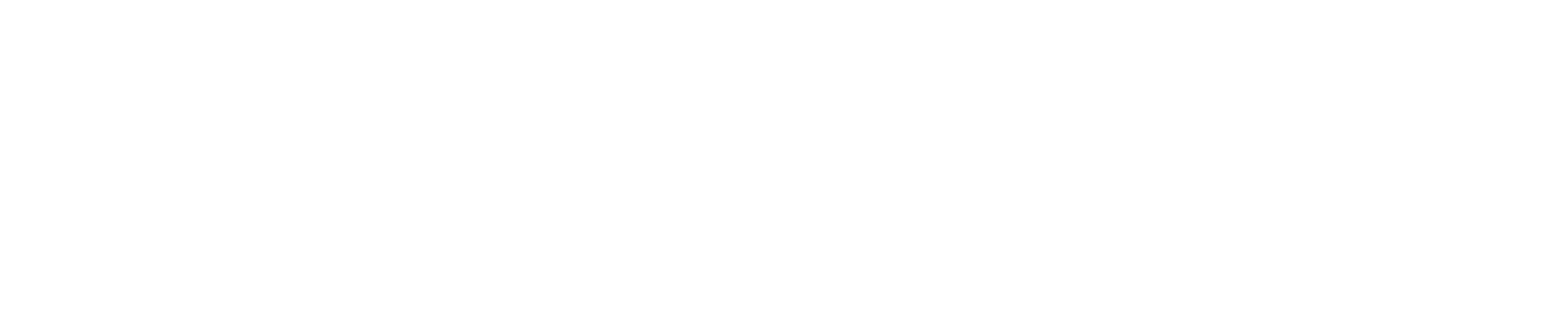
Collaborative R&D helps take the weight off civil aerospace
Engineers’ obsession with weight and strength is reaching new heights in the aerospace sector. A range of technologies are being developed for manufacture, many with research centre support, that are designed to cut weight and carbon in aviation. By Will Stirling
It was a good landing at the end of 2023. Commercial aircraft orders and deliveries are flying high, and up in 2022 by some eye-catching margins. It seems like aerospace production is back to pre-pandemic levels. According to aerospace group ADS, 2,430 total aircraft orders have been placed globally to 6th December, a 43% increase on the same period in 2022. Single aisle aircraft account for just over 80% of orders placed this year, demonstrating the rapid recovery in the domestic and short-haul travel industry post-pandemic.
Airbus had recorded 1,395 net orders (gross orders minus cancellations) by the 30th of November, beating its full year 2022 orders (1,041) by 350 aircraft with a month to go. Deliveries to date are 623, again set to beat FY 2022 deliveries of 663. Boeing booked 114 gross orders in November, taking orders to 1,207 by 13th of December. The US plane-maker has delivered 461 aircraft to date – orders and deliveries both up on 2022 numbers. Boeing’s official backlog goes from 5,239 last month to 5,324 as of November 30th and like Airbus, its single aisle aircraft – in particular the 737 family – are the most popular type. To show the comparison with Covid and pre-Covid demand, Airbus has not had such a strong order book since 2014 (1590 orders) while in 2020, it received just 373 orders, about one quarter of 2023. The two main primes are chasing a production rate of about 65 aircraft a quarter, in fact Airbus has stated it wants ‘rate 75’ by 2026.
In November the government announced an Advanced Manufacturing Plan with £4.5bn of funding for sectors including automotive and aerospace, for five years starting in 2025 – a bit sneaky to project the cash forward, given that a new government will have to honour this future spending pledge. £975m is earmarked to support the development of energy-efficient and zero-carbon aircraft technology.
Primes and tier ones are straining to develop low carbon technologies in aviation such as lighter but equally strong parts, sustainable aviation fuel, hydrogen, lighter wing skins, 3D printed structural parts. These endeavours are backed by the Aerospace Technology Institute, a government agency that has granted funded £1.9bn to aerospace companies, near-match-funded by industry, which has a new drive to cut carbon in aerospace called Destination Zero – see below.
Here are some exciting low carbon programmes and components in 2023.
First transatlantic SAF flight
On 28th of November, the first flight by a large passenger aircraft powered only by sustainable aviation fuel (SAF) completed a flight from London Heathrow to New York’s JFK airport. Hailed a success, observers remarked the shortage of SAF supply is a barrier to adoption and more lightweighting and propulsion technology will be needed to hit emissions targets.
50% lighter landing gear
Think of the incredible forces that go into landing gear when aircraft land – the huge mass of the plane, hitting hard into the ground at speed. Now remove half the weight in the landing gear. That’s what TISICS Metal Composites of Farnborough have done – in one key component of the gear, to begin with. It uses metal composites, a blend of titanium or aluminium with a ceramic matrix, to remove up to 50% of the weight but retain the component’s full strength. This year, TISICS won an Aerospace Technology Institute (ATI) award for the product.
Part of a project backed by £2.5m in R&D funding from UK Research and Innovation (UKRI) and Innovate UK, in collaboration with Safran Landing Systems, with its UK base in Gloucester, Light Land is the world’s largest metal composite component for commercial aircraft. Currently, aircraft are made of 50% metal components, but replacing these metal components with TISICS’s lightweight and high-strength metal composites, aircraft can become lighter and more fuel-efficient.
A TISICS composite part weighing the same as a packet of crisps (36g), will be able to carry an astounding 5,000kg. The metal composites technology, applied to landing gear, claims to reduce carbon emissions by 9m tonnes annually, and save airlines £650,000 in fuel costs per aircraft per year. TISICS says that by replacing more traditional metal components with metal composites, the aerospace industry can slash carbon while creating 240 UK jobs by 2028.
Wing of Tomorrow’s 17m wing skin
Since 2018, a team of engineers at the National Composites Centre (NCC) in Bristol have quietly toiled away on a new composites deposition process: a fully automated, wing skin lay-up using novel high-rate deposition technologies. By the end of 2022, they had achieved a world-first, full scale 17 metre integrated wing skin infused in a single step. This is part of Airbus’s Wing of Tomorrow programme.
Composite materials enable wing components to be fully weight-optimised and produced with heavily reduced or eliminated sub-assembly and post-manufacturing costs. They also enable faster production cycles. The NCC was tasked with developing technologies and processes to produce three, full-scale, wing cover demonstrators.
The new deposition technology was designed to specification and supplied by UK automation integrator Loop Technology with collaboration from Güdel and Coriolis. It comprises two bridges, weighing 45 tonnes and 24 tonnes, 7m high by 13m wide, running along a 26m track. These bridges position automated end-effectors to enable cutting and deposition of dry fibre materials to high levels of quality and speed.
The automated process begins at a 20-metre table positioned inside the cell where an ultrasonic cutter profiles the carbon fabric to shape. An algorithm then selects the correct end-effector to pick the material up and then lay it onto the tool. Once lay-up of all the plies, processing and integration is complete, the component can then be infused with resin and cured.
For Wing Cover 3, the complete ply stack of dry fibre piece parts – approximately 170 individual dry fibre pieces – was deposited using the NCC’s Ultra High-Rate Composite Deposition, with no manual intervention. The real wings that will use this process will be incorporated in the next generation of single aisle aircraft, the timing of which is unknown.
Recyclable fibre tape for more sustainable composite manufacturing
The Multipurpose Fibre Reinforced Thermoplastic Tape (FRTT) Development Cell at the University of Sheffield Advanced Manufacturing Research Centre is being funded by a £1.7m grant from the Engineering and Physical Sciences Research Council. Such a material has huge potential. While aircraft are using more composite materials to reduce weight, their recyclability has remained frustratingly low. Sustainable thermoplastic composites are exciting due to their ability to be recycled, re-moulded and reused time and time again – once perfected.
“With regards to recycling, thermoplastics can be ‘remelted and remoulded’, making it far easier to recycle these materials over thermosets. You usually keep the fibre in the polymer, as it provides the strength,” said the FRTT cell project lead at the AMRC.
ATI’s Destination Zero
The ATI launched its Destination Zero programme in 2021 to achieve net zero carbon emissions for commercial aircraft by 2050, supporting the industry in sustainable design, manufacture, assembly and operations of future aircraft. Its three pillars are to focus on developing 1. Overt zero emission flights, using new propulsion like hydrogen, 2. ultra-efficient aviation, using existing engines that are more efficient, such as Rolls-Royce’s UltraFan engine platform, and 3. enabling technologies, capturing lightweight components etc.
Recently the ATI launched two new programmes, a hydrogen capability network and – of special interest to MTD readers – a new SME Programme to assist smaller companies – see below.
Elsewhere, Airbus has developed and recently manufactured a cryogenic superconducting electric propulsion system purposely built to aerospace specifications, that should transfer more current and therefore power in an electric powertrain. And Rolls-Royce recently completed a successful run of its UltraFan technology demonstrator at maximum power at its facility in Derby, using 100% SAF fuel.

Subscribe to our Newsletter today!
Stay up to date with the latest industry news and events.
