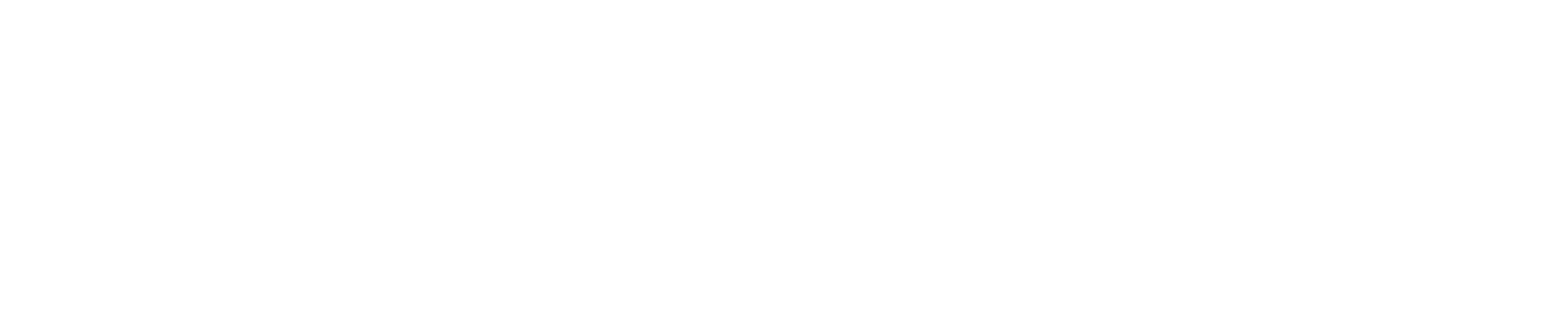
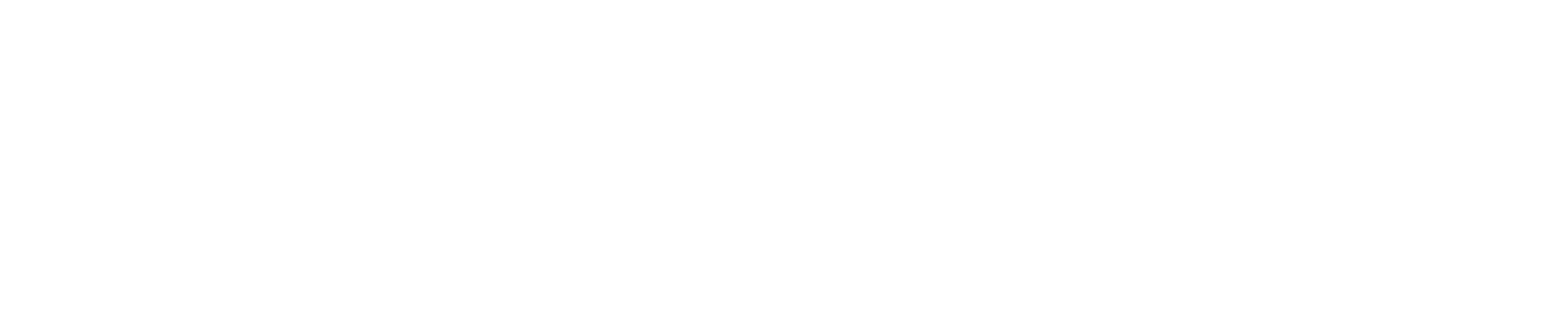
Se 1 | Ep 6
Automotive technology for aerospace
Machine tool manufacturer Zimmermann recently brought MAPAL aboard as a technology partner to design a turnkey solution for machining titanium aerospace parts. MAPAL’s line boring technology combined with a new generation of tools made this challenging project a resounding success.
F. Zimmermann GmbH is known for its large portal milling machines that are often found in the R&D departments of large aerospace corporations.
“We have always been craftspeople and not mass producers”, is how Steffen Nüssle, Head of Sales and Application Technology at Zimmermann describes the manufacturing philosophy. Multiple machines are already being deployed by an Asian aerospace part supplier. However, the most recent was for a highly customised gantry machine. A fixture was also needed to machine a certain part. In addition, Zimmermann was selected to commission the tooling for the special machining process.
The part is a 1.5m long mount with a row of twelve 17mm bores in the lugs, which are located over a space of 990mm to a tolerance of H7. Over the entire length of the part, the concentricity of the bores had to be less than 0.05mm.
Past Zimmermann turnkey projects involved wing spars for the Airbus A350 and countersinks and deep bores on fibreglass wind turbine blades. While employed for another machine manufacturer, Nüssle also worked with MAPAL. This involved machining bearing seats for crankshafts and camshafts for large diesel motors using line-boring technology. MAPAL has extensive knowledge of line-boring bars from the automotive industry. Now, this knowledge was required for aerospace parts whose lugs are similar to the journal bearings in the crankshaft bearing aisle of a combustion engine.
“This project challenged our technological knowledge in all realms,” asserts Sven Frank, Global Head of OEM Management at MAPAL. “We didn’t even have a sketch of the part to start with.”
The titanium alloy TA15m proved a challenge. “We knew what we were getting into, but even our full-fledged aerospace experts had never heard of this special alloy,” Steffen Nüssle admits. Jens Ilg, who works in the Aerospace & Composites segment at MAPAL, agrees: “The material was exotic for us, too.” The TA15m workpiece material is manufactured powder-metallurgically. The sintered material is re-densified in a special process, whereby the workpiece acquires the characteristics of a forged part.
While the machine was being constructed by Zimmermann, MAPAL began tool tests in Aalen, relying on a new generation of titanium tools for this purpose. To achieve high removal rates, the NeoMill-Titan shell face milling cutter was chosen. The 60 minutes that Bernd Scheurenbrand expected were exceeded. “Some of the tools were at work for almost seven hours.” This result was made possible due to the modern protective coating with good adhesion to the tool, an effective temperature barrier and a very smooth surface that reduced heat on the cutting area.
To clear pockets and cavities, MAPAL selected the solid carbide milling cutter OptiMill-Titan-HPC. When machining the gaps between the lugs, the trochoidal milling cutter OptiMill-Tro-Titan was able to show off its strengths with short contact times and optimal heat removal. “In tests, we were able to mill the lug down to a wall thickness of 3mm without it pushing away or vibrating,” Ilg reports.
Excellent cooling is essential when machining titanium. To remove the heat that developed, MAPAL MillChucks with integrated coolant supply was used. For the bores on the sides of the lug, MAPAL developed a custom tool with an angular drill head based on the MEGA Speed-Drill-Titan.
Line boring is an ideal way to create the main bore of the mount. The twelve lugs are arranged in four groups with three journal bearings. The first lug pack is initially piloted. The drill for machining the second lug pack is guided through these pre-machined bores.
The 685mm line boring bar with a diameter of 17mm has two adjustable inserts and is led between the lugs in guide bushes. The first insert bores the main bore, thus eliminating any offset that might have occurred during pre-machining. The second insert then completes the final diameter to H7 quality.
Subscribe to our Newsletter today!
Stay up to date with the latest industry news and events.
