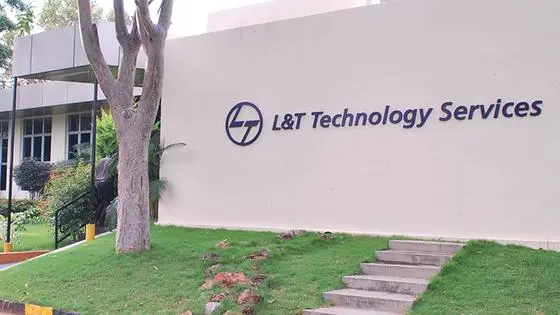
L&T Technology Services and thyssenkrupp Steering Forge Strategic Partnership to Launch Global Software Hub in Pune, India!
thyssenkrupp Steering, a global leader in steering technologies, and L&T Technology Services (LTTS), a prominent player…
Reader Query: We’ve been exploring automation options for several of our machines to enhance production efficiency. The company we’re collaborating with offers various choices including robots, cobots, pallet systems, and robot-loading pallet systems. Can you assist us in distinguishing between these options and identifying where each would be most suitable?
Miller’s Response: Among the many advancements in our industry, the proliferation of automation stands out as particularly intriguing for shops. What was once primarily for high-volume manufacturers is now available in compact, adaptable solutions that work with any platform or controller type.
Traditionally, methods of presenting work to spindles have remained constant in the automation space. Whether for high-volume manufacturers or others, there were typically two options: a transfer system moving workpieces on dedicated fixtures through multiple process steps, or a robot handling one part at a time on a machining center. To simplify this decision for your shop and frame future automation choices, there are essentially two types of automation solutions: workpiece handling and pallet handling.
Workpiece Handling versus Pallet Handling
A workpiece-handling solution involves automation loading raw material directly into a common workholding device. This could be achieved through a robot arm, a gantry arm, or even a bar feeder, while the machine side would feature a chuck, air vise, or a custom hydraulic/pneumatic solution to process the material.
On the other hand, a pallet-handling system transports workholding, already loaded with workpieces, to the machine via a common connection type. This is often done using retention studs that securely hold the pallet to the machine, ensuring consistent work offsets from one load to the next.
A workpiece solution requires attention to part loading, coordination between machine and robot, and chip control. However, a collaborative robot offers flexibility for a shop handling a mill one day and a lathe the next. A pallet-handling solution may entail higher initial costs due to extra workholding, similar to filling a tool magazine on a new machine, but these pallets remain set up indefinitely and are available as needed.
Both types offer distinct advantages, making them appealing options for shops. To make the best decision, consider the broader shop context and weigh setup time against run time. For instance, a robot may need time to fine-tune motion and logic for each run, while a pallet system requires time to establish work offsets for each incoming pallet but only once. Both activities take away from cutting metal, so the productivity benefit of investing time in them should be considered.
If your work primarily involves longer runs suited to a common workholding system, such as vises for Op1 and soft jaws for Op2, a workpiece-handling solution makes sense. This offers automation productivity without the added expense of extra pallets and associated workholding.
On the other hand, if your work is diverse with short runs, like in a prototyping shop, a pallet system is more suitable. Setting up a robot for each run in this scenario may feel cumbersome, but setting up common workholding solutions once on a series of pallets ensures repeatability, significantly reducing setup times for future projects.
Consider your shop’s preferred implementation method as well. Modern pallet systems are compact and tightly integrated into the machine’s controller, making them easy to learn. Similarly, modern robots can adapt grippers easily and are programmed in a straightforward manner. Thus, two shops with similar incoming work may find equally productive and profitable solutions in their own way.
An advantage of modern automation is its flexibility. Decisions made to address current constraints can be adapted or redeployed for future needs. A workpiece solution can easily transition from machine to machine, while a pallet solution can handle high-volume or high-mix work with simple workholding changes.
Original source mmsonline
Stay up to date with the latest industry news and events.
Be first to see all the updates from MTDCNC
Our newsletters frequency varies dependant on content
All the latest deals from the industry feature on our newsletters