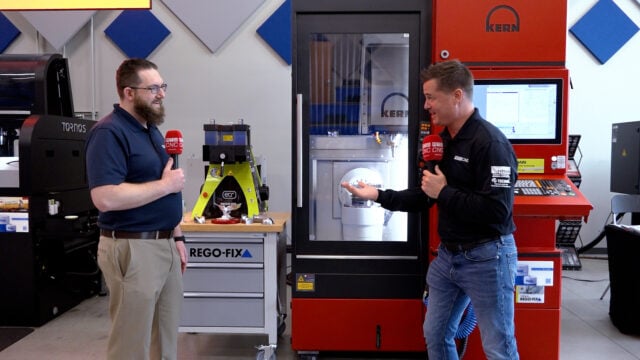
10 hours saved? Same machine, just smarter software!
Tony Gunn of MTDCNC teams up with Josh Proctor from OPEN MIND Technologies to show how…
Trumpf has unveiled a cutting-edge service for TruLaser Center users in the United States, known as Remote Operations Support. This service connects highly skilled Trumpf experts located in Neukirch, Germany with U.S.-based customers, offering real-time support for the autonomous laser-cutting process. Aimed at maximizing uptime and efficiency, the service ensures TruLaser Center machinery continues production seamlessly, even in the absence of onsite operators.
The TruLaser Center, a comprehensive laser cutting solution, automates every stage of the process—from loading sheet metal to cutting, part removal, and sorting. However, fabricators may face challenges if a machine halts during an unsupervised night shift or when an operator is unavailable due to illness or vacation. Remote Operations Support addresses this by allowing Trumpf experts to monitor machine operations, diagnose issues, and intervene as necessary to keep production flowing.
“Many of our customers rely on automated production during off-hours, hoping to start each day with stacks of completed parts. With Remote Operations Support, we can ensure this by actively monitoring the TruLaser Center machinery and intervening remotely when issues arise,” says Christine Benz, TruServices Director at Trumpf. “This service empowers fabricators to optimize machine uptime and reduce dependency on local operator presence.”
The Remote Operations Support team leverages advanced remote connectivity tools to diagnose and resolve machine stoppages quickly. The typical response time to resolve a machine standstill is under fifteen minutes, with over half of all downtime issues being resolved remotely. This significantly reduces idle time and ensures high throughput, even during extended, unattended production runs.
Additionally, the Remote Operations Support platform incorporates data analytics to identify and predict potential issues, allowing the support team to preemptively address concerns before they lead to stoppages. This proactive approach aligns with Trumpf’s commitment to intelligent manufacturing solutions, ensuring customers achieve consistent output, minimized downtime, and greater operational flexibility.
The introduction of Remote Operations Support highlights Trumpf’s dedication to leveraging digitalization and connectivity to enhance productivity in automated laser cutting. By providing remote monitoring, rapid troubleshooting, and proactive maintenance, Trumpf empowers U.S. fabricators to boost their operational efficiency and confidence in automated production, ultimately supporting their business goals with uninterrupted precision manufacturing.
Stay up to date with the latest industry news and events.
Be first to see all the updates from MTDCNC
Our newsletters frequency varies dependant on content
All the latest deals from the industry feature on our newsletters