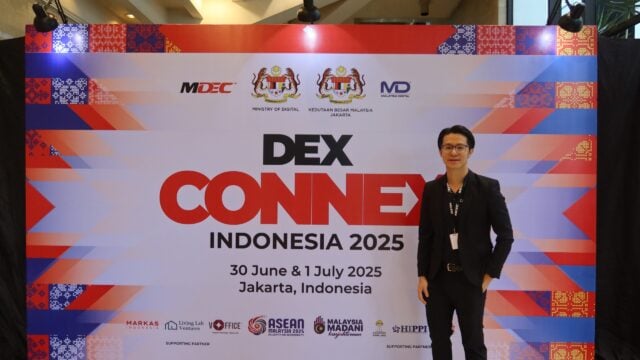
Tapway Expands into Indonesia with Three Strategic Channel Partnerships!
Tapway Sdn Bhd has announced its expansion into the Indonesian market, forging partnerships with three leading…
Many fabrication shops performing TIG welding are considering automation as a viable option. Understanding the benefits and drawbacks of this switch is crucial, with advantages significantly outweighing the disadvantages.
Manual TIG welding demands skilled welders due to its need for precision and consistency. Robotic TIG welding offers a solution to this challenge by providing consistent welds once programmed correctly, leading to increased productivity without welder fatigue or waste. Cincinnati Inc.’s EZ Weld cell, a pioneering TIG welding system, is leading the charge in this automation revolution.
The process involves 3D printing metal paste and CNC machining it in a single operation, followed by controlled sintering to create fully dense steel mold cores or cavities. This approach ensures precision and cleanliness, crucial in industries where aesthetics are paramount.
By integrating 3D printing into manufacturing and welding processes, aerospace component production is achieving superior quality outcomes. The technology facilitates accurate feeding of electrode wire and precise alignment of components for welding, leading to increased arc-on time and consistent wire usage.
The UR5e cobot, boasting six axes and a seventh axis for better reach, maximizes robot arm usage and allows movement in tight spaces with ease. Additionally, the welding cell autonomously detects sheet metal deformation without operator intervention, ensuring uniform welds across the material.
Safety is a top priority in developing the robotic TIG welding cell, with the UR cobot equipped with preset safety features that can be further customized. Dual work zones enable welding in one area while operators safely handle parts in another, enhancing overall safety and efficiency.
Cincinnati Inc.’s decision to develop robotic TIG welding equipment reflects its commitment to helping customers succeed. The system offers substantial productivity increases, ease of deployment, and faster return on investment (ROI), simplifying production by automating labor-intensive tasks.
In conclusion, the transition from manual to automated TIG welding presents significant benefits, including increased productivity, precision, and safety, making it a compelling option for fabrication shops.
Original source www.fabricatingandmetalworking.com
Stay up to date with the latest industry news and events.
Be first to see all the updates from MTDCNC
Our newsletters frequency varies dependant on content
All the latest deals from the industry feature on our newsletters