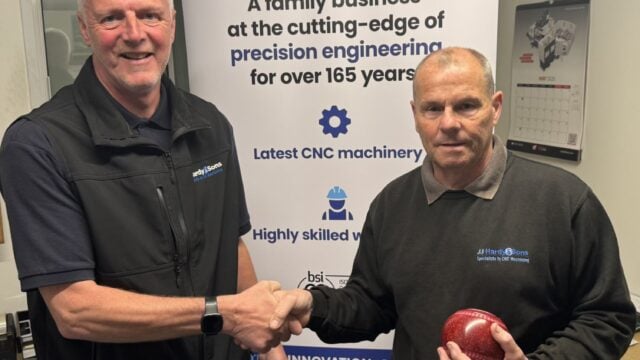
JJ Hardy & Sons Celebrates the Retirement of Long-Serving Team Member Archie
JJ Hardy & Sons, a renowned family-owned precision engineering firm established in 1856, announces the upcoming…
For manufacturers of medical devices, the speed at which prototypes are produced can make all the difference in seizing opportunities. Every facet of the machining process, from programming to cycle time to measurement, plays a crucial role. Often overlooked, however, is the impact of efficient inventory management on turnaround times.
Joseph Forsyth, Director of Advanced Manufacturing at Intech, a medical device manufacturer in Athens, Alabama, emphasizes the significance of quickly accessing accurate inventory data. It’s not just about having the necessary items on hand; it’s about answering essential questions related to tool availability, quantities, and precise locations.
Prototyping, in particular, demands a diverse range of tooling and workholding options. According to Forsyth, the challenge lies in managing the extensive inventory of tools required for CNC machining, with a single component potentially necessitating over a hundred different tools and supplies.
As Intech expanded its services globally, serving hundreds of customers, the complexity of its inventory grew. With more cutting tools, collets, and components than ever before, their traditional inventory management system proved inefficient. This led to the adoption of innovative solutions, including vertical lift modules (VLMs) from Kardex Remstar, tool vending machines from SupplyPro, and tool management software from ZOLLER.
The implementation of this new tooling management system, featuring Kardex Shuttle VLMs, not only streamlined inventory but also freed up substantial space, allowing for the incorporation of two additional CNC machines. The software provided by ZOLLER enables accurate tracking of tool life and usage, offering valuable insights into tooling decisions.
To cope with the growing complexity of its tooling inventory, Intech categorized tools into consignment, burn, and stock. The ZOLLER TMS software facilitated the cataloging of $1.3 million worth of items in just one year. The integration of Kardex Shuttles and ZOLLER TMS software significantly enhanced efficiency, particularly in pre-staging jobs. Operators can now easily retrieve required tools from the Kardex Shuttles, with the system directing the process based on job numbers entered into the ZOLLER TMS software.
This streamlined approach has drastically improved efficiency, with the pre-stage team easily handling production jobs for 70 machinists. The visibility into tooling inventory also revealed redundancies and overlaps, leading to a more cost-effective approach. Intech saved $100,000 on tooling costs, despite an increase in work.
Apart from cost savings and process streamlining, the new inventory system has become a valuable discovery tool. It has increased visibility into the vast array of tools available, encouraging employees to explore and enhance their knowledge. The organized trays not only store tools but also showcase them, contributing to a culture of curiosity and continuous learning.
Intech Athens plans to extend this solution to its assembly department, emphasizing the importance of organization in handling expensive assemblies. The implementation of Kardex Shuttles is seen as a foundational step, with ongoing plans for further optimization as the company continues to evolve and expand.
Original source MMSonline
Stay up to date with the latest industry news and events.
Be first to see all the updates from MTDCNC
Our newsletters frequency varies dependant on content
All the latest deals from the industry feature on our newsletters