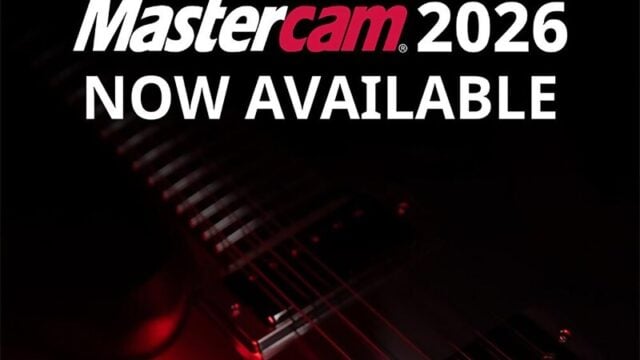
Mastercam 2026 Launches with AI-Driven Tools and Enhanced Machining Capabilities!
Mastercam has unveiled Mastercam 2026, an advanced release packed with productivity-boosting tools, AI-powered CAM intelligence, and…
Is the landscape of injection mold production poised for a transformation? Presently, mold cores and cavities are crafted using CNC machining centers, meticulously milled from tool steel, and this conventional method is expected to persist for the foreseeable future.
However, a novel approach to creating cores and cavities has emerged and is now fully available in the market, courtesy of the California-based startup Mantle. Dubbed the “TrueShape” system, this innovative method still utilizes a modified CNC machining center but introduces a unique twist: it begins with steel in paste form and leverages 3D printing technology.
Here’s how it works: Mantle’s proprietary metal paste is 3D printed and CNC machined in a single operation. Through controlled sintering, the paste transforms into a fully dense steel mold core or cavity, equivalent in material quality to H13 or P20. This streamlined process eliminates rough milling, EDM, and drilling of cooling lines, which can now be 3D printed conformal to the tool geometry.
The performance of tools created through the TrueShape process matches that of traditionally made molds, with one molder, Tessy Plastics, successfully exceeding 1.65 million cycles with a TrueShape mold. The key difference lies in the significantly accelerated pace: printing and sintering a core and cavity takes a mere two to three days, compared to the several weeks typically required for conventional injection molds.
Mantle’s cofounder, Ted Sorom, notes that while TrueShape competes favorably against conventional moldmaking in terms of both cost and time, it is the time savings that are driving adoption and potentially reshaping tooling development practices. For large OEMs producing plastic parts, tooling costs are already expected, but the increasingly uncontrollable lead time for molds impacts their agility and innovation speed.
Chief Commercial Officer Paul DiLaura emphasizes that TrueShape’s rapid production tooling eliminates the need for prototype tools, blurring the line between production and prototype tooling. This not only streamlines validation processes but also “de-risks production,” ensuring that if the part design works, production can commence with the same tool.
Furthermore, the predictability and accuracy of the TrueShape system make it an effective estimating tool, simplifying job quoting for users. Beyond these tangible benefits, TrueShape also enhances the capabilities of individuals involved in moldmaking, allowing them to focus on higher-value tasks by streamlining the overall process.
In essence, Mantle’s TrueShape system represents a paradigm shift in injection mold production, offering a faster, more efficient, and more predictable alternative that empowers manufacturers to innovate with greater agility and precision.
Original source mmsonline.com
Stay up to date with the latest industry news and events.
Be first to see all the updates from MTDCNC
Our newsletters frequency varies dependant on content
All the latest deals from the industry feature on our newsletters