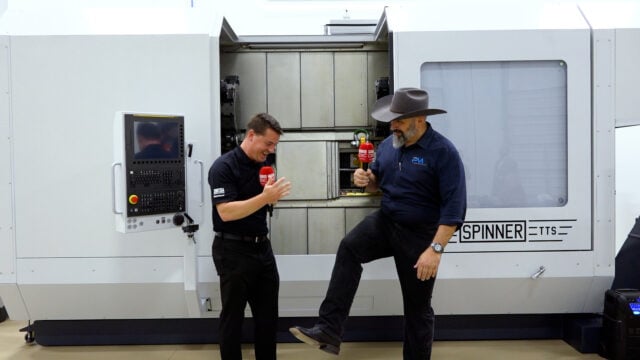
When the parts get massive, you need a machine that does more than keep up.
The Spinner TTS 85 is not just any turning center—it’s a precision beast with live tooling,…
In addition to traditional gear machining processes such as hobbing, gear shaping and broaching, skiving is a continuous machining process for soft and hard machining of internal and external gears [2]. The skiving process is characterized by the tool and workpiece axes arranged in a certain relationship to each other – the axis cross angle (Fig. 1). With the coupled rotation of workpiece and tool, a relative movement of the cutting edge in the tooth space is thus created. By superimposing a feed motion, both add to the movements to the feed speed and guide the cutting edge along the workpiece axis. In this way the tooth space is “peeled out” of the workpiece in several cuts (Fig. 2). The cutting speed results from the rotational speeds of tool and workpiece in relation to the axis cross angle. Significant for the skiving process is the short machining time (approx. 30 to 50 %) in comparison to the likewise flexible gear shaping and the ability to apply the gearing close to an interfering contour (workpiece shoulder). The smaller the axis cross angle, the closer towards the interference contour can be machined.
The main advantage of the process integration is that the components can be finished without or at least with fewer downstream machines. This eliminates a large part of the loading and unloading of the components, the intermediate transportation and the quality losses due to clamping faults in the subsequent machining processes.
Be first to see all the updates from MTDCNC
Our newsletters frequency varies dependant on content
All the latest deals from the industry feature on our newsletters