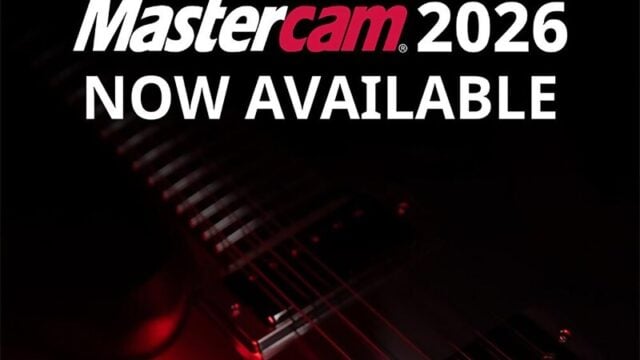
Mastercam 2026 Launches with AI-Driven Tools and Enhanced Machining Capabilities!
Mastercam has unveiled Mastercam 2026, an advanced release packed with productivity-boosting tools, AI-powered CAM intelligence, and…
At Eastec 2025, Open Mind Technologies introduced the HyperMill 2025 CAD/CAM Software Suite, a powerful solution designed to elevate machining productivity and precision. With enhanced programming capabilities and advanced machining strategies, HyperMill 2025 is ideal for five-axis and mill/turn machining, offering manufacturers the tools they need to optimize their workflows and produce highly accurate parts with greater efficiency.
One of the standout features of HyperMill 2025 is its five-axis automatic tool orientation mode, which ensures optimized machining by providing efficient and reliable tool paths for the most complex molds and components. The software uses a pre-analysis algorithm to evaluate the entire tool path, calculating machining sequences for simultaneous and indexed tool movements. This reduces the number of inputs required for five-axis machining and significantly saves time when programming intricate and challenging parts, making it easier to achieve precision even in complex geometries.
This automatic tool orientation mode is particularly beneficial for manufacturers working with complex molds, where minimizing programming time and optimizing tool paths can result in significant productivity gains. It allows for a seamless and automated approach to five-axis machining, making it easier to tackle even the most demanding tasks.
The HyperMill 2025 software also introduces a redeveloped pocket milling algorithm designed for high-feed cutters. This new algorithm improves 3D-optimized roughing performance, offering greater efficiency during roughing operations and providing better machining control. This feature is particularly valuable when machining large lateral in-feeds and managing remaining material. Additionally, contour and path radii can be precisely defined, resulting in improved toolpath rounding and smoother operation, further enhancing the quality of the finished part.
Deburring is an essential part of many machining processes, and HyperMill 2025 addresses this with a fast, easy, and safe five-axis hole deburring strategy. This feature excels at deburring sharp edges on holes and intersecting holes, ensuring that parts are smooth and safe to handle. Using CAM Plan programming assistance and analysis technology, the software automatically recognizes all holes in the model and marks sharp edges for deburring. This eliminates the need for manual intervention, saving time and reducing the risk of errors.
The deburring strategy supports both three-axis and five-axis modes, allowing manufacturers to select the most appropriate option for their needs. The five-axis deburring strategy offers even greater flexibility, enabling access to more component edges and automatically generating the required inclinations, all while ensuring collision avoidance for safe and effective deburring.
To further improve the machining process, HyperMill 2025 integrates Dynamic Stock technology via the HyperMill Virtual Machining Optimizer. This technology automatically updates the stock for all machining jobs, ensuring that stock conditions are accurately accounted for when calculating linking movements. By taking into account the actual stock conditions, Dynamic Stock helps optimize tool paths, improve cycle times, and reduce the risk of errors associated with inaccurate stock data.
This enhancement leads to better-informed machining decisions, particularly in the context of multiple operations, where managing the stock condition is crucial to achieving high-quality results.
The HyperMill 2025 CAD/CAM Software Suite from Open Mind Technologies represents a significant advancement in five-axis and mill/turn machining. With its enhanced capabilities in toolpath optimization, high-feed roughing, hole deburring, and stock management, HyperMill 2025 empowers manufacturers to achieve higher productivity, improved precision, and faster turnaround times on complex parts. These innovations make it an essential tool for businesses looking to stay competitive in an ever-evolving manufacturing landscape, ensuring efficiency, flexibility, and high-quality results.
Stay up to date with the latest industry news and events.
Be first to see all the updates from MTDCNC
Our newsletters frequency varies dependant on content
All the latest deals from the industry feature on our newsletters