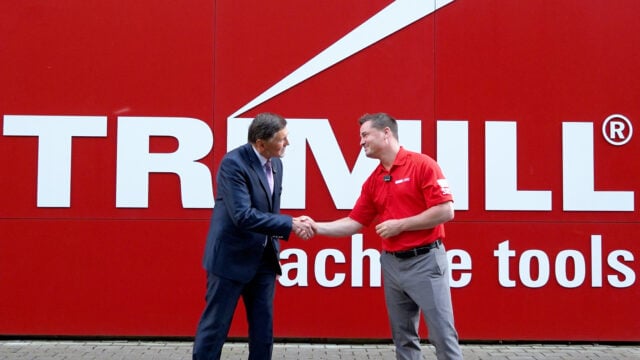
How did a two-person startup become a global machine tool powerhouse?
Precision, passion, and persistence — that’s the story behind this Czech company’s success.Join Tony Gunn of…
Okuma America Corp. announced the launch of its latest innovation, the LB2000 EX III horizontal lathe, expanding its esteemed LB-EX series. Designed to meet the demands of high-accuracy machining, the LB2000 EX III stands out with its robust construction and advanced features, making it an ideal choice for manufacturers seeking precision and efficiency.
Equipped with a 140 flat spindle, the LB2000 EX III is engineered to produce finely-tuned small parts and complex components with exceptional accuracy. When paired with optional MYW (milling, Y-axis, and sub-spindle) modules, this horizontal lathe offers unparalleled versatility, catering to a wide range of machining applications. The integration of these optional features allows users to perform high-speed milling, drilling, and coolant-free cutting, ensuring consistent, high-quality results across various projects.
A key factor contributing to the LB2000 EX III’s high-accuracy performance is its rigid construction, which minimizes vibrations and enhances stability during operation. This solid build is complemented by a high-torque PREX motor, delivering both high power and torque essential for heavy-duty and high-speed cutting tasks. The combination of robust construction and powerful motor ensures that the lathe maintains machining precision and thermal stability, even under demanding conditions.
The LB2000 EX III is further enhanced by Okuma’s exclusive OSP-P500 open-architecture control system. This advanced control platform is specifically designed for Okuma machines, providing a host of intelligent machining technologies that streamline operations and improve user experience. The OSP-P500 features a Windows-based open-architecture platform, allowing seamless integration with applications from the Okuma App Store and beyond. Its dual-core computer processors offer greater processing power, enabling faster data handling and smoother machine operations. Additionally, the control system includes embedded cybersecurity features to protect operations and data, ensuring secure and reliable machining processes.
Energy efficiency and sustainability are also at the forefront of the LB2000 EX III’s design. The on-board energy management and green machining capabilities leverage Okuma’s thermo-friendly concept and ECO suite plus functionality, optimizing energy usage and promoting sustainable machining practices. The lathe is equipped with a full-color touchscreen interface, available in both 15″ and 21.5″ sizes, providing an intuitive and user-friendly control experience. Its space-saving, ergonomic design includes tilt and swivel capabilities, as well as optional pulse handles, enhancing operator comfort and accessibility.
Key specifications of the LB2000 EX III include a maximum machining diameter and length of 16.93″ and 11.81″, respectively, and a rapid traverse rate of 1,181 ipm in both the X and Z axes. The lathe operates within a speed range of 45 to 5,000 rpm, making it highly adaptable to various machining requirements. With a standard power rating of 15 hpfor the main spindle and 10 hp for the sub spindle, the LB2000 EX III delivers the performance needed for both precision and heavy-duty applications.
Designed to significantly enhance productivity while ensuring operator safety, the LB2000 EX III reduces the need for frequent setups and adjustments, allowing for uninterrupted machining operations and higher throughput. The thermo-friendly concept minimizes thermal growth during machining, maintaining dimensional accuracy and prolonging tool life. Okuma’s intuitive drag-and-drop feature and extensive function library facilitate rapid workflow optimization, saving valuable time and resources for operators.
The rigid construction of the LB2000 EX III not only boosts machining speed but also fosters a safer and more efficient working environment. Its advanced safety features and ergonomic design reduce the risk of accidents and operator fatigue, contributing to a more productive and comfortable shop floor.
Stay up to date with the latest industry news and events.
Be first to see all the updates from MTDCNC
Our newsletters frequency varies dependant on content
All the latest deals from the industry feature on our newsletters