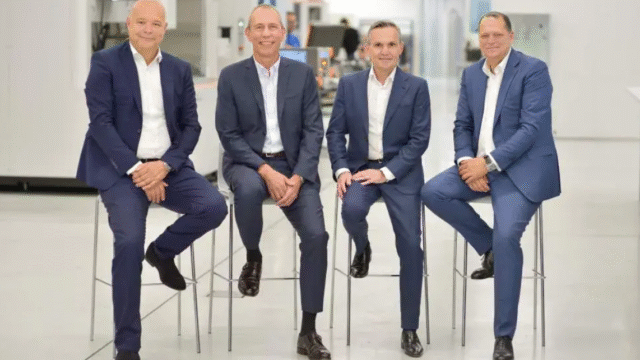
United Machining Solutions Emerges as Global Powerhouse Following GF Machining Solutions Takeover
The merger of the GF Machining Solutions Division of George Fischer AG with the United Grinding…
Niigata has introduced the HPN800 horizontal machining center (HMC), designed to offer superior performance, speed, and flexibility for high-demand production environments. The HPN800 is built with a rugged, high-torque spindle that optimizes operations, increases throughput, and enhances efficiency, making it ideal for the machining of larger parts across a variety of materials and industries. With its robust construction, the HPN800 addresses the need for reliable and cost-effective solutions in the most challenging manufacturing settings.
The HPN800 comes equipped with a powerful 75 hp high-torque spindle, enabling it to handle demanding machining tasks with precision. This powerful spindle allows the machine to perform both rough machining and fine finishing processes with ease, making it an excellent choice for manufacturers looking for versatile, high-performance equipment. Additionally, the machine offers a range of tool and pallet system options, providing flexibility for various machining needs.
At the core of the HPN800’s performance is its ultra-rigid, T-shaped machine base with a honeycomb structure and three-point leveling. This design ensures maximum stability and durability, which are essential for achieving high precision and reliability during machining. The rigid base also contributes to the machine’s ability to maintain a solid spindle connection, minimizing vibration and enhancing accuracy, even under heavy loads.
The HPN800 incorporates advanced lubrication and cooling systems, ensuring optimal temperature control for the spindle and other critical components, reducing wear and extending machine life. The machine also features accessible service points and built-in diagnostics, making it easier for operators to maintain the machine and address potential issues promptly. Niigata’s hybrid guideway system contributes to the HPN800’s impressive rapids of 2,400 ipm, significantly boosting productivity and minimizing downtime.
Another standout feature of the HPN800 is its cam-driven automatic tool changer (ATC) system, which offers an impressive tool-to-tool time of just 2.5 seconds. This feature enables high-speed tool changes, enhancing the overall efficiency of the machining process. In addition, the HPN800 is equipped with an exclusive carousel-type Multi-Pallet System and a Flexible Manufacturing System (FMS), controlled by Niigata’s Intelligent Cell Controller (ICC). These systems allow for seamless automation, improving overall productivity and reducing the need for manual intervention.
The HPN800 is designed to handle heavier duties and a greater workpiece envelope compared to other machines in its class. It also provides a variety of high-performance spindles to accommodate different machining requirements, further expanding its versatility. These capabilities make the HPN800 an ideal solution for manufacturers looking to increase productivity while maintaining precision and reliability in their operations.
In summary, the Niigata HPN800 HMC combines advanced features like its high-torque spindle, hybrid guideway system, and fast tool-changing capabilities to deliver exceptional performance in demanding production environments. Its robust construction and advanced systems make it a highly reliable choice for manufacturers seeking to improve efficiency, reduce costs, and meet the demands of large-scale production.
Stay up to date with the latest industry news and events.
Be first to see all the updates from MTDCNC
Our newsletters frequency varies dependant on content
All the latest deals from the industry feature on our newsletters