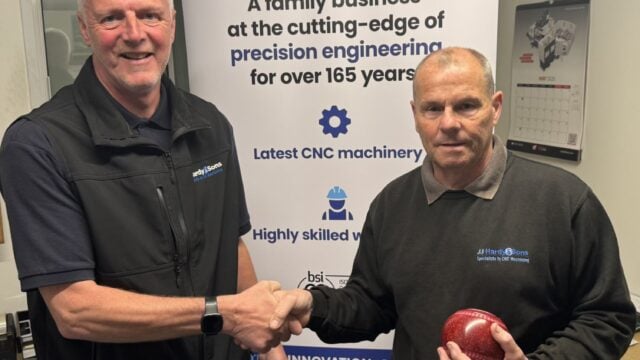
JJ Hardy & Sons Celebrates the Retirement of Long-Serving Team Member Archie
JJ Hardy & Sons, a renowned family-owned precision engineering firm established in 1856, announces the upcoming…
LiCON, a leading manufacturer of precision CNC machines, has introduced its twin-spindle machine with i³ technology, designed to offer an economical solution even for small batch production runs. This innovative machine, developed through a collaboration with Bosch Rexroth, promises to enhance production efficiency, reduce space requirements, and increase output by 20 to 25 percent compared to previous solutions.
One of the key features of LiCON’s twin-spindle machine is its ability to maintain high precision during the machining of hydraulic valve housings. The main requirement in the production of these components is the accuracy of the control valve bore, which is critical for the overall functionality of hydraulic systems. The i³ technology employed by LiCON corrects the motor spindles independently, ensuring that the machine maintains high spindle stiffness across all three axes (X, Y, and Z). This correction is essential for precision during the machining process, even in the presence of external variables such as temperature changes.
Temperature sensors integrated with sophisticated algorithms actively monitor and adjust the spindle performance, ensuring minimal impact on the machine’s positioning accuracy. This allows for fast start-up times and high-quality production, even during frequent setup changes. The use of LiFLEX technology has also been a game-changer for flexibility in production, with the ability to handle over a hundred different hydraulic valve variants, each containing four workpieces per clamping.
LiCON’s twin-spindle machine features a compact design that reduces the required footprint in the manufacturing facility, offering space-saving benefits. Despite its smaller size, the machine has increased output by a significant margin, with improvements in productivity, tool life, and setup times. The machine’s compact design does not compromise its ability to process large volumes of parts efficiently, which makes it an ideal solution for manufacturers who need both performance and efficiency in a smaller, more agile package.
The collaboration between LiCON and Bosch Rexroth also extended to the integration of automation and data collection, marking a significant step toward Industry 4.0. The machine integrates seamlessly with Rexroth’s automation solutions, enabling the intelligent networking of machines and processes. This integration allows for better communication and data exchange between machines, improving operational efficiency and providing manufacturers with real-time insights into production.
Furthermore, the project’s success can be attributed not only to the machine’s technical capabilities but also to the excellent customer support provided by LiCON. The company offered quick responses to change requests, ensuring that adjustments and additions could be implemented smoothly during the project’s progression. LiCON’s commitment to customer satisfaction is evident in the ongoing service and support available to clients, with a dedicated project manager and a 24/7 service hotline ensuring assistance is always accessible.
Following the success of the initial implementation, LiCON and Bosch Rexroth have embarked on a follow-up project that involves two additional manufacturing cells. These newer systems feature the LiFLEX II 776 i3 PC B2, which incorporates even faster tool-changing capabilities and further reduced non-productive times. With these updates, the cycle time per component has been reduced by an additional 25 seconds, further enhancing production efficiency.
LiCON’s collaboration with Bosch Rexroth also continues in the realm of hydraulic valves, with both companies relying on each other’s technologies. The hydraulic valves used in these systems, which are manufactured on LiCON machining centers, are known for their high reliability and precision, ensuring that the final components meet the stringent quality standards required in the manufacturing process.
LiCON’s twin-spindle machine with i³ technology represents a significant leap forward in the world of small batch production. By combining precision, flexibility, and efficiency, the machine is helping manufacturers streamline their processes and reduce operational costs. With a strong focus on continuous innovation and customer satisfaction, LiCON is well-positioned to drive further advancements in the machining industry. The successful collaboration with Bosch Rexroth also highlights the importance of integrating automation and data-driven technologies in modern manufacturing, paving the way for smarter, more efficient production lines.
Stay up to date with the latest industry news and events.
Be first to see all the updates from MTDCNC
Our newsletters frequency varies dependant on content
All the latest deals from the industry feature on our newsletters