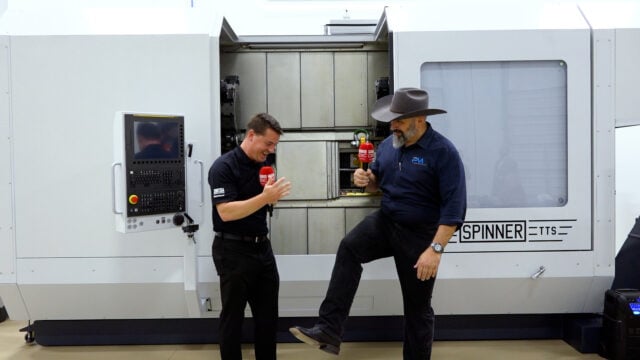
When the parts get massive, you need a machine that does more than keep up.
The Spinner TTS 85 is not just any turning center—it’s a precision beast with live tooling,…
HII’s Newport News Shipbuilding (NNS) division has made a significant breakthrough in additive manufacturing (AM) by successfully installing the first-ever 3D-printed valve manifold assembly on a new construction aircraft carrier. This marks a pivotal moment in shipbuilding as the company continues to integrate additive manufacturing into the construction process, aiming to enhance efficiency and streamline production for the U.S. Navy.
The valve manifold assembly, which is an essential component that distributes fluid from a single source to multiple points on the ship, was installed in the pump room of the Gerald R. Ford-class aircraft carrier, Enterprise (CVN 80). The assembly, weighing approximately 1,000 pounds and measuring about 5 feet long, represents a leap forward in the use of 3D printing for producing large, complex parts in the shipbuilding industry.
This development is part of NNS’s broader strategy to use certified 3D-printed components to accelerate construction timelines and improve manufacturing quality. The shift to additive manufacturing for critical parts like the valve manifold could significantly reduce lead times and enable faster delivery of vessels to the U.S. Navy.
NNS collaborated with DM3D Technology, a key partner, to manufacture the manifold body using additive manufacturing. This collaboration reflects the shipyard’s commitment to exploring and capitalizing on all opportunities to integrate 3D printing into the construction process. As a result, the shipbuilding industry is witnessing the evolution of traditional manufacturing methods toward more efficient, modern techniques that can meet the demands of military applications.
With this successful installation on Enterprise (CVN 80), NNS plans to replicate this approach for similar manifolds on the Doris Miller (CVN 81). By using additive manufacturing instead of traditional casting methods, these components will help reduce schedule risks, improve efficiency, and optimize the overall shipbuilding process.
Dave Bolcar, NNS Vice President of Engineering and Design, emphasized the importance of this milestone, stating, “What started as a proof of concept quickly turned into a tangible result that is making a meaningful difference to improve efficiencies in shipbuilding.” The use of additive manufacturing in shipbuilding is not only enhancing the process for current projects but also laying the groundwork for future innovations in the industry. NNS’s ability to harness 3D printing technologies has the potential to transform the way the U.S. Navy’s fleet is built, making shipbuilding faster, more flexible, and cost-efficient.
NNS has already received certification and approval as a supplier for additive manufacturing components for Naval Sea Systems (NAVSEA) platforms. So far, the shipyard has produced and installed over 55 AM parts on both new construction vessels and existing ones currently in service. With plans to install over 200 additional AM parts in 2025, the shipyard is poised to continue its leadership in the integration of 3D printing technology in shipbuilding.
This latest achievement in additive manufacturing highlights the growing role of 3D printing in defense and aerospace industries. With the successful integration of 3D-printed components like the valve manifold assembly into critical military platforms, NNS is setting the stage for further advancements that could redefine how ships are constructed. By leveraging the power of AM, NNS is not only improving the efficiency of shipbuilding but also contributing to the future of naval technology, ensuring that the U.S. Navy remains at the forefront of innovation in defense capabilities.
Stay up to date with the latest industry news and events.
Be first to see all the updates from MTDCNC
Our newsletters frequency varies dependant on content
All the latest deals from the industry feature on our newsletters