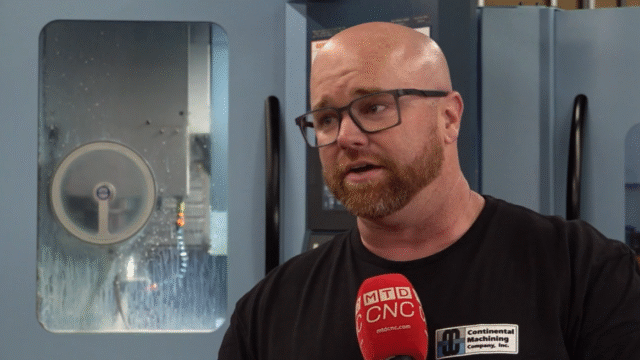
How did they cut a 3-week job down to just three days?!
When Continental Machining Company added a Matsuura to their lineup, they didn’t just upgrade—they accelerated. Kelly…
At Eastec 2025, Heule Precision Tools showcased their advanced DCC tooling, a breakthrough solution designed to drill and chamfer both sides of a workpiece in a single operation—all without the need to turn the workpiece or change tooling. This innovative technology provides a highly efficient way to reduce cycle times while maintaining precise results at high feed rates.
Heule’s DCC tooling integrates a solid carbide drill body with a SNAP chamfering system, enabling the tool to both drill and chamfer a bore in one seamless process. The tool is capable of working with holes ranging from 4.0 to 10.0 mm (0.15 to 0.39 inches), making it well-suited for a variety of applications. The tool’s ability to chamfer both edges of the bore immediately after drilling significantly reduces the need for secondary operations, leading to increased overall efficiency.
The solid carbide construction of the DCC tooling ensures optimum concentricity and high drilling performance, even at high cutting speeds and feed rates. This specialized design allows the tool to achieve precise results at cutting speeds that would typically be challenging for other tools. With bore depths of up to 2.5×D and chamfer sizes up to 0.8 mm, the DCC tooling excels in both precision and depth, ensuring high-quality results in a fraction of the time.
In addition, the SNAP chamfering system is equipped with easily replaceable carbide chamfering blades, which feature material-specific coatings to enhance tool life and performance. This tool’s ability to perform multiple functions in one pass, without needing to switch between drills or turning the workpiece, significantly reduces downtime and improves workflow efficiency.
The DCC tooling is versatile and can be customized with specific drill geometry and coatings to suit a wide range of materials, including cast iron, stainless steel, titanium, aluminum, and steel. Depending on the workpiece material, Heule adapts the drilling geometry and coating to maximize performance and tool longevity. Additionally, if larger chamfers are needed on the front edge of the bore, a stepped drill configuration can be integrated into the tool.
Another key advantage of the DCC tooling is its ability to machine both even and slightly uneven bore edges. The defined cutting process coupled with ground carbide blades ensures complete edge breakage, resulting in burr-free surfaces both on the front and back of the workpiece. This eliminates the need for manual machining, further simplifying tool management and enhancing overall process efficiency.
The DCC tooling system’s one-piece solid carbide construction is engineered for both precision and speed, allowing the bore to be drilled and chamfered in a single operation. By eliminating the need to turn the workpiece or change tooling, the system reduces cycle times and streamlines the manufacturing process. This means that manufacturers can achieve high-quality results faster and more efficiently, while also reducing the risk of error and tool wear associated with multiple tool changes.
Heule’s DCC tooling technology offers a highly efficient and precise solution for drilling and chamfering in a single operation, providing significant advantages in terms of cycle time reduction, tool management, and overall machining efficiency. With its solid carbide construction, customizability for various materials, and ability to create burr-free, high-quality results, DCC tooling is a game-changer for manufacturers looking to enhance productivity while maintaining high standards of precision.
Stay up to date with the latest industry news and events.
Be first to see all the updates from MTDCNC
Our newsletters frequency varies dependant on content
All the latest deals from the industry feature on our newsletters