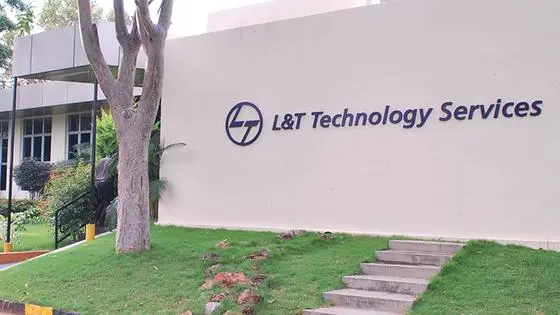
L&T Technology Services and thyssenkrupp Steering Forge Strategic Partnership to Launch Global Software Hub in Pune, India!
thyssenkrupp Steering, a global leader in steering technologies, and L&T Technology Services (LTTS), a prominent player…
HCLSoftware has announced the release of HCL CAMWorks 2025, a groundbreaking update to its leading CAMWorks software, now fully integrated with 3DExperience SolidWorks. This integration facilitates seamless data management and cross-discipline collaboration in the cloud, offering companies an advanced platform for new product development. With cloud-connected technologies, teams across engineering, design, and manufacturing can collaborate efficiently, ensuring smoother workflows and faster product development cycles.
The integration of HCL CAMWorks with 3DExperience SolidWorks allows users to access the benefits of cloud connectivity, enabling cross-disciplinary collaboration in real-time. This integration ensures that companies can combine expertise across different sectors while working on new products, improving efficiency and innovation throughout the design and manufacturing process.
HCL CAMWorks for 3DExperience SolidWorks is also fully compatible with CAMWorks and SolidWorks CAM data from the SolidWorks desktop version, providing flexibility for businesses to coordinate CNC part programming across different platforms. By allowing data sharing between the new cloud-based system and the desktop versions of SolidWorks CAM and CAMWorks, companies can work seamlessly across different environments, improving efficiency and workflow consistency.
One of the most significant enhancements in HCL CAMWorks 2025 is the introduction of machine-aware programming, which now includes machine components, collision detection, and an option to pause on collision. This powerful feature enables CAM programmers to create a CNC setup and program parts on a digital twin of the CNC machine. By incorporating a digital twin into the programming process, programmers gain immediate graphical insights into critical machine parameters, such as table size, travel limits, rotational limits, and available tooling. This enables them to assess the feasibility of the machining process before starting the physical operation.
Machine-aware programming transforms the CNC machine into an interactive component of the programming process. It empowers programmers to identify potential issues early in the development cycle, ultimately increasing productivity and enhancing part quality. By minimizing errors during the programming stage, companies can avoid costly mistakes and reduce downtime, further streamlining the entire production process.
In addition to the machine-aware programming feature, HCL CAMWorks 2025 includes several new features and enhancements designed to optimize CNC programming and improve operational efficiency:
With these improvements, HCL CAMWorks 2025 offers a comprehensive and efficient solution for companies looking to optimize their CNC programming processes. The software’s cloud-based collaboration, machine-aware programming, and additional enhancements position it as a vital tool for modern manufacturers looking to stay competitive in a rapidly evolving industry.
The release of HCL CAMWorks 2025 represents a significant step forward in the evolution of CNC programming and manufacturing. The seamless integration with 3DExperience SolidWorks and the introduction of machine-aware programming elevate the software’s capabilities, providing manufacturers with more efficient, accurate, and cost-effective solutions for CNC part programming. By adopting these cutting-edge technologies, businesses can streamline their operations, improve product quality, and achieve greater productivity.
Stay up to date with the latest industry news and events.
Be first to see all the updates from MTDCNC
Our newsletters frequency varies dependant on content
All the latest deals from the industry feature on our newsletters