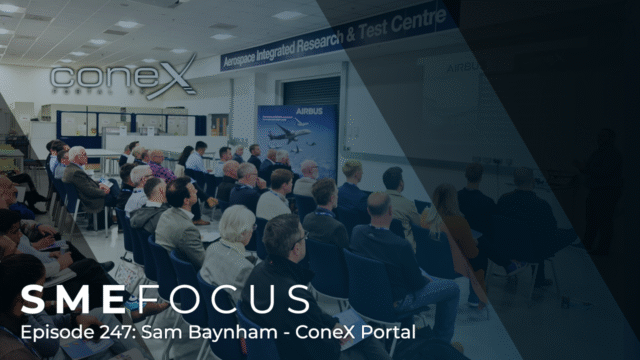
SME Focus Episode 247: Sam Baynham – ConeX Portal
SME Focus is the programme showcasing our brilliant SMEs. For manufacturers, by manufacturers. The weekly show…
Formlabs, a renowned leader in additive manufacturing, has expanded its ecosystem with the introduction of new materials, improved workflows, and advanced postprocessing tools. These updates are designed to streamline 3D printing applications across various industries, especially in the realm of stereolithography (SLA) and selective laser sintering (SLS) technologies. The goal is to make it easier and more efficient for manufacturers to create consumer-ready parts while enhancing productivity and precision.
One of the significant additions to Formlabs’ portfolio is the Clear Cast Resin, developed specifically for investment casting applications. This new resin offers superior thermal expansion properties, allowing foundries to produce intricate cast designs in-house. By enabling faster casting with minimal cracking and enhanced accuracy within 0.25 mm, Clear Cast Resin is set to transform the casting process. The material helps reduce costs, speed up turnaround times, and offers greater flexibility in iterating designs. John Farr, Vice President of Technology at Diversified Metalsmiths, praised the resin for seamlessly integrating into their workflow, highlighting the time savings achieved by bypassing machining and handwork after casting.
In addition to new materials, Formlabs has introduced enhanced postprocessing solutions for both SLA and SLS workflows. The Resin Washing Solution is a nonflammable cleaning agent that dissolves twice as much resin compared to traditional methods, making it a cost-effective option. This solution is designed to reduce the frequency of top-offs, ultimately lowering the overall cost per washed part. Another noteworthy tool is the Fuse Blast Polishing System, which cleans and polishes parts straight from the Fuse Sift, delivering a smooth, semigloss finish that is scuff-resistant and dye-ready. The Fuse Sift Glovebox Bundle further improves postprocessing by streamlining part extraction and minimizing powder exposure, resulting in a cleaner and more ergonomic workflow.
Formlabs is also expanding its impact in the dental industry with the introduction of BEGO VarseoSmile TriniQ Resin, a biocompatible material designed for permanent dental restorations, including bridges. This certified third-party material is compatible with Form 4B printers and offers enhanced accuracy and an efficient workflow for dental professionals. Additionally, the company has launched Open Material Mode for its Form 4 series printers, allowing users to print with any 405-nm resin, thus providing greater flexibility and customization options for businesses across various sectors.
These innovations demonstrate Formlabs’ commitment to advancing 3D printing technology, making it more accessible and efficient for manufacturers. By continuously expanding its ecosystem with new materials and postprocessing tools, Formlabs is empowering businesses to achieve higher-quality results and unlock new possibilities in additive manufacturing.
Stay up to date with the latest industry news and events.
Be first to see all the updates from MTDCNC
Our newsletters frequency varies dependant on content
All the latest deals from the industry feature on our newsletters