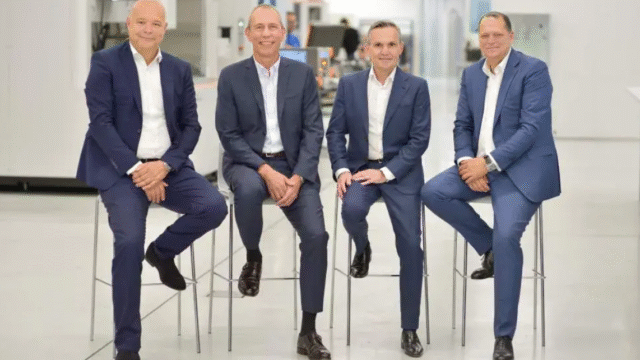
United Machining Solutions Emerges as Global Powerhouse Following GF Machining Solutions Takeover
The merger of the GF Machining Solutions Division of George Fischer AG with the United Grinding…
When asked about the disparity between 2D and 3D machining, the typical response might be, “2D machining operates in two axes, while 3D operates in three.” While this answer is accurate, it barely scratches the surface. So, what exactly does this mean, and when should you opt for one over the other? Delve into this article to gain insights into 2D and 3D machining.
What Sets Apart 2D and 3D Machining? In simple terms, 2D machining operates with two axes, while 3D employs three. The “Ds” in these terms represent “dimensions.” In 2D machining, a tool remains fixed at a certain height but can move side-to-side and front-to-back – these movements constitute the two axes, hence the 2D classification. This concept extends to drilling as well, where the tool remains static on the X and Y axes while the Z axis moves vertically. Picture a wooden block intended for engraving a name; this scenario perfectly aligns with 2D milling, as the engraving stays at a single level along the surface.
In contrast, 3D milling introduces an additional axis of motion, allowing the tool to move up-and-down, thus utilizing three axes. This expanded range of motion enables the machining of significantly more intricate shapes, such as fan blades, mechanical brackets, and gears. For instance, envision carving a miniature mountain into the same wooden block; due to the varying heights and multidirectional cuts involved, 3D machining becomes the method of choice.
2D Machining: Noteworthy Aspects Although foundational, 2D milling is not necessarily simpler than its 3D counterpart. Machining a part in two dimensions isn’t a default choice for ease of operation; instead, it hinges on the part’s design. Commonly 2D machined components include panels, electrical circuits, and signs.
Embracing 3D Machining: Exploring Complexity In contrast, 3D milling thrives on parts with intricate shapes, particularly those featuring sculpted or non-planar surfaces. Industries like mold and die manufacturing, as well as aerospace, heavily rely on 3D machining for their components.
Illustrative Example: Challenging Assumptions A case in point is showcased with a sample part: a butterfly. While the butterfly on the left appears more intricate, it was actually 2D milled, whereas the one on the right underwent 3D milling. This example underscores the importance of letting the part’s complexity dictate the machining method.
Further Insights Many individual machinists initially start with 2D milling and progress to 3D milling as their skills evolve, especially in facilities equipped with both capabilities. It’s common for shops to offer both 2D and 3D services, broadening the spectrum of machinable parts. In such environments, the boundaries between these technologies, and even the next step – multi-axis machining, can become blurred.
Original source www.mtwmag.com
Stay up to date with the latest industry news and events.
Be first to see all the updates from MTDCNC
Our newsletters frequency varies dependant on content
All the latest deals from the industry feature on our newsletters