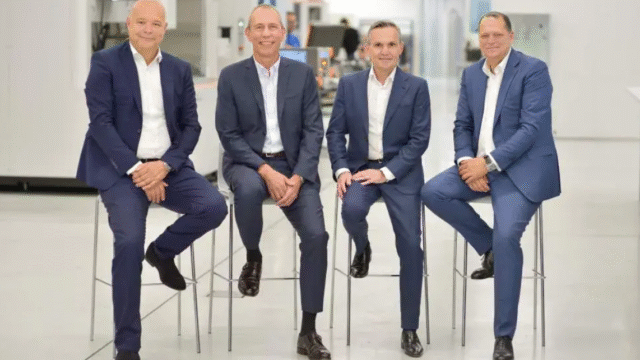
United Machining Solutions Emerges as Global Powerhouse Following GF Machining Solutions Takeover
The merger of the GF Machining Solutions Division of George Fischer AG with the United Grinding…
ALM Positioners and Path Robotics have announced a groundbreaking multiyear strategic partnership aimed at transforming industrial positioning systems into fully autonomous, AI-powered welding solutions. This collaboration marks a significant milestone in the evolution of automation technology in the manufacturing sector. As part of the agreement, ALM Positioners has been named Path Robotics’ Preferred Positioner Partner—the first of its kind.
The strategic partnership between ALM Positioners and Path Robotics focuses on developing intelligent automation for high-mix, multipass welding applications. The combined system, which integrates Path Robotics’ advanced AW-3 welding robot with ALM’s precision positioning systems, is designed to tackle challenges associated with extreme part variability and complex weld paths. The system’s ability to adapt seamlessly to different part configurations without the need for reprogramming makes it a game-changer for industries dealing with variable production runs and complex welding tasks.
With this advanced system, manufacturers will be able to automate their welding processes more efficiently and with greater flexibility, even in environments where traditional automated systems would have struggled. This partnership empowers manufacturers to handle intricate, multipass welding applications that require high precision and adaptability, making automation a viable option in more industries and applications than ever before.
The AI-powered welding system created by ALM Positioners and Path Robotics eliminates the need for constant reprogramming. This is especially crucial for applications where parts vary greatly from one production run to the next. Typically, the need to reprogram welding robots for each new part or weld path is a significant hurdle, but with this new technology, the system automatically adjusts to the part and the specific welding requirements in real time.
This level of adaptability is made possible through Path Robotics’ cutting-edge computer vision and machine learning algorithms, which work in conjunction with ALM Positioners’ state-of-the-art positioners. Together, they create an intelligent, flexible, and autonomous welding system that minimizes downtime and maximizes productivity.
The partnership between ALM Positioners and Path Robotics comes at a time when the demand for greater automation and precision in welding is on the rise. The ability to offer autonomous welding systems that require minimal human intervention could significantly reduce labor costs and increase operational efficiency for manufacturers. Moreover, the intelligent automation system is expected to help reduce the likelihood of errors that can result from human operators, improving the overall quality and consistency of the welded parts.
By making automation feasible in applications with extreme part variability, this partnership opens the door to new possibilities for industries such as automotive, aerospace, heavy machinery, and more, where high-mix welding is essential. The ability to efficiently and consistently weld parts with complex geometries and varying dimensions will set the new system apart from conventional welding methods.
With Path Robotics and ALM Positioners leading the way, the future of welding automation looks promising. By combining AI technology with precision positioning systems, the partnership is setting the stage for more accessible, adaptable, and efficient automation solutions in the welding industry. As manufacturing environments continue to demand more flexibility and precision, this collaboration is poised to revolutionize the industry, offering solutions that were once out of reach for many businesses.
This partnership marks the beginning of a new chapter for industrial automation, with potential for wide-reaching impacts across multiple sectors. With intelligent welding systems that adapt in real-time to part changes, manufacturers can look forward to a future where automation is smarter, more efficient, and more accessible than ever before.
Stay up to date with the latest industry news and events.
Be first to see all the updates from MTDCNC
Our newsletters frequency varies dependant on content
All the latest deals from the industry feature on our newsletters