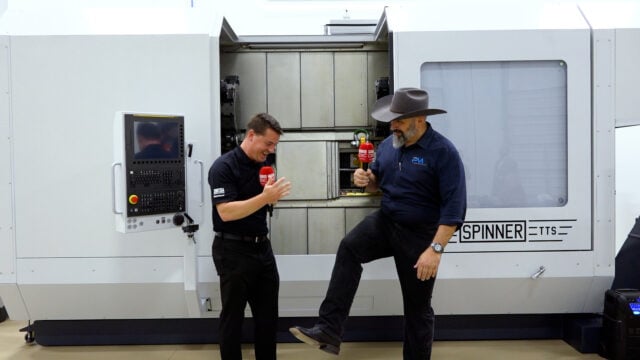
When the parts get massive, you need a machine that does more than keep up.
The Spinner TTS 85 is not just any turning center—it’s a precision beast with live tooling,…
3D Systems and TE Connectivity, a global leader in connectors and sensors, today announced their collaboration to develop an additive manufacturing solution for electrical connectors that exceed UL regulatory criteria. 3D Systems’ Figure 4® Modular, Figure 4 material, 3D Sprint® software, and services met TE Connectivity’s specific material performance and high-tolerance, dependable printing needs. The solution is based on a photopolymer 3D Systems created for TE Connectivity.
It is the first printable photopolymer to undergo UL®1-recognized long-term thermal ageing (RTI). TE Connectivity devices require reliability and accuracy, which this material and optimised print process provide. 3D Systems’ Figure 4 technology’s novel material qualities, speed, and precision enable the first tough industrial solutions for appliances, cellular, and data-center applications.
Additive manufacturing allows TE Connectivity to develop complicated geometries that injection moulding cannot. It improves flexibility for low-volume, quick-turn production runs and tooling avoidance, allowing TE to demonstrate its capabilities and clients to satisfy demand faster.TE Connectivity and 3D Systems’ Application Innovation Group (AIG) developed a full production pipeline from design to connector.
Be first to see all the updates from MTDCNC
Our newsletters frequency varies dependant on content
All the latest deals from the industry feature on our newsletters