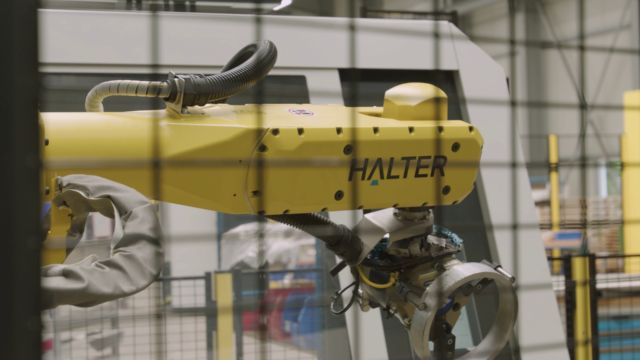
Everything robots, service, and support with Michiel at HALTER CNC Automation Open House
What’s it like to be a Service Manager at HALTER CNC Automation? When you’ve got robots…
HALTER CNC Automation presents itself at the AMB as an automation partner
Hoevelaken – 30 June 2022
At the AMB in Stuttgart, HALTER CNC Automation presented its extensive and varied portfolio of robot cells for the automated loading and unloading of CNC machines. The company also demonstrated how automation solutions with highly customer-specific functions can be realized in a simple and flexible manner on the basis of standardized loading robots.
At present, HALTER CNC Automation offers its HALTER LoadAssistant in the Compact, Premium and Big versions, which in turn can be divided into the model variants for turning and milling (Universal), turning (TurnStacker) and milling (MillStacker). Thanks to the open interface (the HALTER Smart Interface), all CNC machines – whether older machines you already have in stock or new investments – can be easily connected to our loading robots, which can be quickly integrated into any production environment due to the high degree of standardization.
HALTER CNC Automation has shown during the AMB that the HALTER LoadAssistant is increasingly proving its value as an extremely flexible automation solution, especially through the customer-specific functions. “Configuring our loading robots individually according to customer requirements is almost a daily task. Most customers are particularly interested in automation that helps them meet the challenges associated with production while maintaining a high degree of flexibility. This is why all our robot cells can be expanded with new functions and robot processes without much effort,” explains Wouter van Halteren, CEO of HALTER CNC Automation.
Such additional functionalities may, for example, consist of additional special grid plates or part buffers for accommodating a larger number of customer-specific workpieces. Moreover, in addition to the actual loading and unloading, the kinematics of a robot can be flexibly adjusted in just a few steps with the HALTER Smart Control. For example, this can be done to integrate a measuring point into the automation process or to transport a certain number of completed parts of a production batch from the robot cell via a conveyor belt. But it is also conceivable that a robot, before loading a CNC machine, first grips a workpiece at a station and turns it to the optimal position for clamping. However, these are just a few examples of the possibilities offered by the HALTER LoadAssistant.
Another important advantage is that the additional functions and processes can be implemented at any time, including at a later date. The user-owners are therefore always flexible. Even if they initially invest in a standard solution, they do not have to decide at that moment what the loading robot should be able to do in five years’ time. “We always implement the desired functions when needed, because with our many years of experience we do not see ourselves as a supplier but as a real automation partner. The demand from our customers proves this, because they increasingly see the potential of our solutions. More than 80 percent of them have more than one HALTER LoadAssistant in operation,” says Wouter van Halteren.
HALTER CNC Automation at the AMB:
Hall 6, Stand 6C55
Be first to see all the updates from MTDCNC
Our newsletters frequency varies dependant on content
All the latest deals from the industry feature on our newsletters