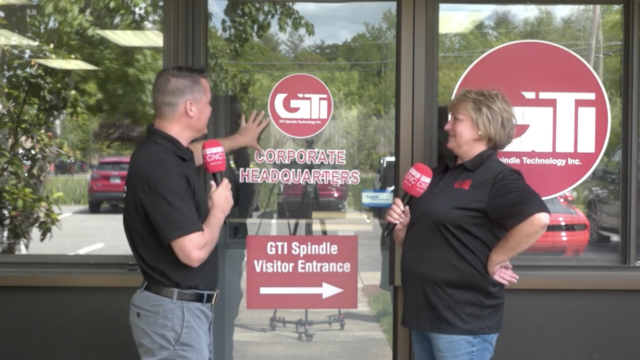
A closer look at the history and expansion of world leaders in spindle Technology
MTDCNC is at the GTI Spindle Technology headquarters in New Hampshire, where Tony Gunn talks to…
No matter how built-out your in-house repair department is — how well-equipped or how well-staffed — there will be times when you need to outsource certain services, and source replacement parts. That’s a simple fact. Even union facilities, which mandate in-house repairs, need to outsource certain things they can’t do themselves, due to lack of either equipment or specific expertise.
That’s the nature of the modern manufacturing workspace. You simply can’t do it all. And frankly, you shouldn’t strive to.
One of the most commonly seen issues at facilities with in-house programs is that components on failed spindles are simply swapped out, without addressing the root cause of failure. This leads to repeat failure, quickly, and possibly more extensive damage.
Take a bearing. If one fails and you simply replace it, and never learn the reason it failed, your setting yourself up for more failure and headaches. The cause could be a worn, or undersized, bearing journal, that will continue to cause bearings to fail. Until you rework the journal to specification, you’re just throwing good money after bad, as the saying goes.
It’s like putting air in a tire that’s on a bent rim. You can fill that tire as many times as you want, or even replace the tire, but until you replace or repair the rim — until you address the underlying cause — your tire is going to keep getting flat.
Luckily, in today’s manufacturing landscape, you can find somebody with expertise in anything, no matter how niche of a discipline it may seem to you. You can’t possibly be expected to maintain in-house expertise in such a wide variety of unique processes and parts, especially with current labor constraints.
Commonly outsourced services, other than bearing inspection and replacement, include:
Parts that you’ll need to purchase include:
It’s important to source “exact match” replacement parts, in accordance with the manufacturer’s stated specifications. “Close enough” will not do. It might work briefly, but eventually will lead to more problems. In certain cases, a spindle needs to be disassembled and a part may need to be reverse engineered. This is particularly true for older models, as well as certain less common brands of specialty spindles.
You should also consider outsourcing training and other support services. Certain complex machinery, such as spindles, require more detailed knowledge than you can expect to maintain in-house, but also more regular maintenance than is possible with outsourcing alone. Getting training and support from a specialist bridges that gap.
Strictly in terms of spindles, a support training program should include:
Inspection, including:
Finally, you can help to ease the burden on your in-house repair program and lower the financial impacts of repeat failure with the smart implementation of a predictive maintenance strategy.
Be first to see all the updates from MTDCNC
Our newsletters frequency varies dependant on content
All the latest deals from the industry feature on our newsletters