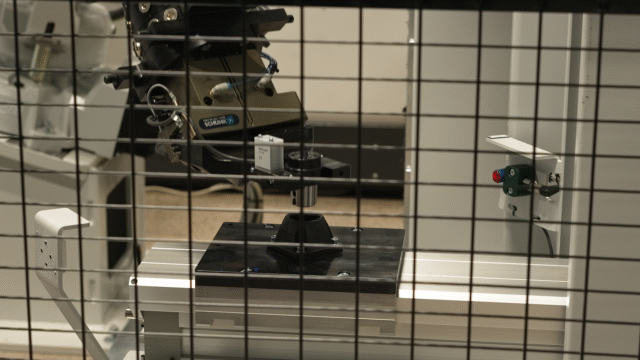
Unlock the power of flexible manufacturing with true end-to-end automation!
Think Fastems is just about pallet automation? Think again. In this exclusive walkthrough, Mika Laitinen of…
This blog discusses the daily difficulties production managers face and how they can be solved. In the studio with the host and Marketing Director Mikko Tuomaala are Head of Product Management of digital products Topi Juden and product manager Janne Kivinen.
This blog post is a summary of what was discussed on the second episode of FasTALKS – our video podcast that discusses relevant topics around factory automation in the metalworking industries.
What does a typical production manager’s day look like nowadays?
If you look at the big picture the key theme is hurry. This is caused by pressure from customers, i.e. meeting the promised delivery times, and from the manufacturing set-up itself, including all of its limitations, imperfections and of course the capacity. Then, when you add unexpected surprises like missing resources, machine breakdowns, sick-leaves or quick customer requests distorting the production plan heavily or eating away at most of the capacity, the average day starts to look like quite the nightmare.
What’s behind the curtain?
Probably lot’s of things but one of the fundamentals is a lack of transparency and monitoring over production. This means that problems (like missing resources) are not being identified beforehand or that information about problems (like machine breakdowns) reach the production manager with too much of a delay. Oftentimes, it might also be that the production manager doesn’t simply know the current status – utilization – of the machinery (discussed about in more detail in the “top 5 manufacturing myths” podcast episode). This has a lot of implications on performance analysis and continuous improvement: the foundation of reliable data and stable, re-producible processes are missing.
Topi illustrated this exact situation with a story about a visit to of an aerospace manufacturer in Italy. At the time, the company was thinking of investing in a fourth machine tool to increase capacity. However, when Topi got a tour of the factory, he noticed that even the existing three machines weren’t utilized even close to their full potential: they were idling (not-chip-cutting) most of the time during the visit. The key here was that this company felt, nevertheless, that their capacity was full and that they needed a new machine. Quite obviously, the problem had a root cause in lacking transparency and the true utilization of the machinery. Once the actual problem had been identified the best solutions could be found.
Utilization is important – but why isn’t it enough?
Simply monitoring utilization doesn’t paint the entire picture. Even if machines are running with, say, over 90 % utilization, they might not be providing the right parts at the right time which – at the end of the day – is what reels in the money. Instead, to optimize set-up times, manufacturers oftentimes make larger batches than customer orders require at the time. In turn, this creates an unnecessary increase in work-in-progress (WIP) and looses lead time capacity for items, that would be more crucial to be manufactured at that precise moment.
Additionally, the production needs to fulfil all of the quality requirements. Everyone who has ever worked on anything knows that being rushed equals to errors and mistakes. Although they are not done on purpose, the negative effect for production is substantial. This can lead to scrapping not just one item, but in worst cases the entire machine tool can stop and need maintenance – and there we go, that’s another unexpected surprise…
Let’s wrap this up – is it really hell that production managers are facing?
The daily hurry and number of unexpected changes keeps the production manager very busy. Combined with a lack of visibility and transparency over key production figures, at worst this means a constant negative cycle and at best, a kind of running-to-stand-still situation where long-lasting total process improvement is difficult to achieve. Being stuck like this can be hell for some.
We’ve been working with thousands of manufacturers globally for decades, so we know that some versions or stages (think Dante) of this is real for some. The manufacturers are not to be blamed here, of course. These problems are really large and systemic, and unfortunately practical and easy-to-use solutions haven’t been around for very long time.
Nevertheless, this situation is in stark contrast with controlled, re-producible processes that make the right things at the right time, optimizing and giving visibility over all of the production key figures of utilization, lead time, WIP and quality.
Is there any way out?
Fortunately, a lot can be done to remedy the situation. Here’s a summary of steps followed by a more thorough discussion:
Order driven manufacturing
Let’s begin with the concept of order-driven manufacturing. This means that parts are only produced according to the actual need of customers and not to stock. This requires having full visibility and control over the production capacity and orders, as well as being able to (re-) prioritize them. Everyone involved in production needs to know what the current order priorities are and how these boil down to the practical level of actual job tasks and when.
Automatic fine-scheduling and production planning
Another key is to utilize automatic fine-scheduling and production planning software. This means that when there are customer orders (typically in ERP), there is another system that creates the production plan automatically based on the delivery dates of each production item. If something changes – for any reason – the plan is automatically re-calculated and updated. For the software to be able to plan and run the production, it needs to have the capability to link the manufactured item to certain raw materials, fixtures, NC-programs, operations and tools.
This software can be used with or without automation hardware, as is the case e.g. for our Work Cell Operations. There are huge implications here for the daily life of a production manager! When production management software is responsible for the production plan, it is also able to prompt the operator to start preparing the next workpiece(s) at exact the right time. This is a huge leap towards a LEAN-type of manufacturing process.
Optimizing set-ups
When talking about batch manufacturing and how to make the daily life easier and smoother, set-ups have a paramount role because they are big systemic part of the production. Minimizing set-up times requires standardization of processes, making sure all required tools and materials are available, and creating good instructions for the operators. In many cases, automation that enables for simultaneous* set-ups of one workpiece while another is being processed in the machine tool is also needed, increasing the machine tool utilization and lead times tremendously. Set-ups can also be automated, like Fastems is doing in various applications like RCO and AMC. Here, set-ups are almost completely eliminated.
*this applies only to machines that use pallets of course. For info on turning machines and gripper changes, see the AMC product page.
Transparent production monitoring
The final step is having transparent production monitoring software, that confirms (or contradicts) judgements on the production performance. This helps the production manager see where the inefficiencies truly are and helps them adapt to changes as easily.
Let’s finally boil all this down!
The combination of order-driven manufacturing, automated production planning and fine-scheduling software, and production monitoring features give the production manager the control and visibility that is urgently needed. This means breaking the negative cycle of unexpected changes and hurry, which lead to various kinds of quality problems and inefficiencies.
With these three tools, the production manager can reliably estimate when there is capacity to deliver the next customer order, and easily stay on top of production even when things change. Furthermore, enabled by analytics and standardized processes, production can be more LEAN. Continuous improvement will not just be a word in PowerPoint presentations, but actual, observable reality in the shop floor, supported by the evidenced improvement in utilization and quality, shorter lead times and decreasing WIP.
All in all, this sounds like a lot of manageable Mondays for the production manager!
Stay up to date with the latest industry news and events.
Be first to see all the updates from MTDCNC
Our newsletters frequency varies dependant on content
All the latest deals from the industry feature on our newsletters