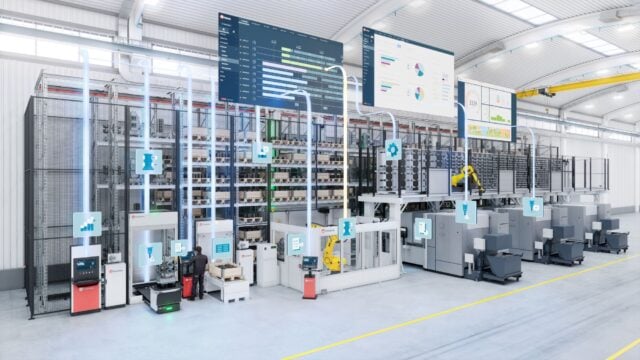
Fastems Unveils Revolutionary Automation Solutions at EMO Hanover 2025
Krefeld, Germany – June 20, 2025 – Fastems is set to unveil groundbreaking innovations at EMO…
This article discusses what flexible manufacturing is and explains why it’s relevant. Furthermore, it presents what an actual flexible manufacturing system or FMS consists of and how its different parts work together. The context of this blog is aimed at the metal cutting industries.
Machine tools automated with an FMS typically reach from 6,000 up to 8,000 annual manufacturing hours, whereas standalone, manually loaded machine tools typically max out at only 2,000 hours.
Undoubtedly, the gap is huge, so let’s find out how this is possible!
Flexible Manufacturing is a production concept that enables economic manufacturing of variable workpieces in small and repeatable batches – that’s why it’s called flexible. When one adds the word ‘system’, the concept comes alive. In short, the idea is to feed machine tool(s) using a rail guided vehicle or a robot, thus enabling simultaneous setups while another workpiece is being machined. The system also needs a buffer storage and control software to allow all this to happen.
Before going any further, let’s consider the two systemic problems causing inefficiency in variable small batch manufacturing. This helps us to understand why FMS is relevant and how it can help achieve impressive machine utilization figures:
Manual workpiece set-up changes take a lot of time, even with automatic pallet changers (APC). Given the large amount of different production items, this becomes the biggest systemic problem for variable small batch manufacturing. In addition, to ensure quality and avoid collisions, the first item needs to be produced with reduced speed and with an operator overseeing the process.
FMS solves this with a buffer of pre-configured pallets and fixtures, combined with related production data such as workpiece item IDs, NC-programs, required tools and tool life. It separates the work schedules of the operator and the machine tool, which means no unnecessary waiting for either. This enables an automated and smooth flow of production items for the machines, and keeps their utilization close to 100% even during nights, weekends and holidays.
The flexibility also means dynamic re-routing of pallets to different machines, creating a huge difference compared to pallet pools, in case of a tool or machine error. Pre-configured set-ups mean that every item, starting from the first, can be run with 100% speed.
The second problem in variable small batch manufacturing is the complexity of organizing different kinds of resources like tools, materials or workholding as well as data, like NC-programs or tool wear information. This quickly becomes one of the main reasons for production ineffectiveness. Scheduled production fails because of fast, unexpected changes, unrealistic production scenarios or unavailable resources. The result is very tangible: low utilization of machines.
As we understand the principal concept and drivers behind flexible manufacturing, it’s time to look at what an actual FMS consists of. Below we illustrate the typical parts of a solution designed to move larger – 400mm or above – pallets. Other scenarios will be discussed in coming blog posts:
Let’s take a closer look on each item:
With proper control software, a flexible manufacturing system can give you really impressive machine tool utilization figures, but the story doesn’t end there: Fastems FMS provides you with the right parts at the right time – and does it at low costs and without large stocks. It enables economic manufacturing of repeatable small batches used in thousands of industrial applications such as:
Be first to see all the updates from MTDCNC
Our newsletters frequency varies dependant on content
All the latest deals from the industry feature on our newsletters