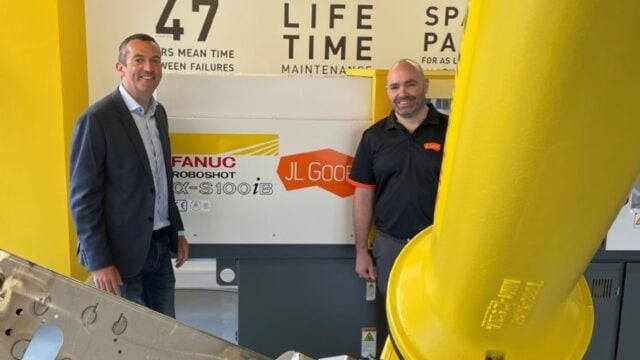
J L Goor Expands Long-Standing FANUC Partnership to Include Robodrill CNC Machines in Ireland
J L Goor Machinery, Fanuc’s trusted Irish partner for over two decades, has announced an expansion…
FANUC has expanded its highly successful portfolio of ROBOCUT high precision CNC Wire EDM machines with the release of the α-C800iB model. Boasting an increased 800mm table, it is the largest machine launched by the company to date.
The FANUC α-CiB machine series comprises of compact, high-performance submerged wire-cutting machines with high rigidity and cutting accuracy.
First displayed to UK customers at MACH, the α-C800iB variant uses Ø0.1-0.3mm wire to process thick, stepped and tapered workpieces up to 300mm in thickness and 3000kg in weight. It also features an increased XY-axis stroke of 800mm x 600mm, along with a Z-axis traverse of 310mm, which can be increased to 510mm on request.
One of the stand-out features of the α-C800iB is the built-in CORE STITCH function, which allows operators to extend unmanned machining hours by the better planning of cutting jobs. Stitch points are set directly on the machine’s CNC without the need for any pre-programming, and when used in combination with the wire path re-threading function it offers the ideal solution for long-lasting unmanned machining and multi-workpiece cutting. Once the job is complete, operators simply knock-out the cores by hand, avoiding any risk of damaging the machine.
The symmetrically designed cast iron structure of the α-C800iB has been optimised for higher stiffness and thermal stability in order to cater for high precision cutting demands. Its space-saving design also combines a large cutting table with a compact footprint and the lowest height in its class.
As with other machines in the series, the α-C800iB employs FANUC’s AWF2 Automatic Wire Feed threading technology to provide fast, reliable automatic threading in just 10 seconds. Unlike other machines, the ROBOCUT series does not need to return to the starting point after a wire break, which radically reduces cycle times. To guarantee reliable threading and re-threading, wires are electronically cut to leave a pointed end which is truly straight and burr free.
Improved cutting control can also be achieved via the built-in iPulse 2 cutting function, which provides highly accurate corner control, regardless of material thickness or surface roughness.
FANUC’s unique twin servo wire tension control also maintains wire tension to within +/-15g of accuracy, further improving both reliability and consistency. As such, a 30kg spool of wire can provide 140 hours of unmanned machining – more than double the expected industry standard.
To help promote a long operational life, built-in sensors measure the water pressure at the bottom of the machine’s tank and self-regulate via servomotors depending on the Z-axis height, to ensure the optimum water level is maintained throughout.
As with all models in the range, the centrepiece of the α-C800iB is the ultra-reliable 31i-WB high-performance control. Complete with 15” colour touchscreen display with intuitive iHMI home screen, it is quick and easy to input and monitor data, while the intuitive visual maintenance interface features a built-in early warning system to identify potential errors before they occur.
Andy Spence, ROBOCUT Product Manager at FANUC UK, comments: “The new α-C800iB is not only our largest ROBOCUT machine launched to date, but also our most versatile. With the ability to machine parts up to 1250 x 975 x 500mm, it is the perfect futureproof wire EDM solution for a market which is becoming increasingly unpredictable. Should the workpiece design change, the α-C800iB is perfectly placed to adapt.
“Whether the α-C800iB is used for specific applications in the automotive, medical or electrical industry, or as part of a general purpose subcontract machine shop, its low running costs and ability to machine sophisticated parts to incredible degrees of accuracy make it the perfect tool for wire EDM cutting.”
For more information on FANUC UK’s ROBOCUT α-C800iB wire EDM machine, please visit: https://www.fanuc.eu/uk/en/robocut.
Be first to see all the updates from MTDCNC
Our newsletters frequency varies dependant on content
All the latest deals from the industry feature on our newsletters