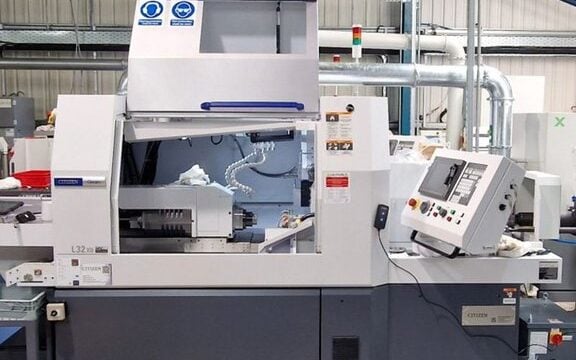
Citizen Machinery Delivers Advanced CNC Lathes in Northeast
Citizen Machinery UK has successfully delivered and installed the Cincom L32-XII LFV numerical control machine to…
For machining parts from bar up to 20 mm in diameter (optionally 25 mm), a third generation of the Cincom L20-LFV series of sliding-head lathes with a considerably uprated specification has been launched by Citizen Machinery UK. Now offered in five variants, VIII, IX, X, XII and XIIB5, it is a best-selling model with platen tooling as well as front and rear tool posts, all stations having driven and static positions on the top three models, which also have additional Y-axis movement of the sub spindle.
Simultaneous 5-axis control for performing complex machining cycles is supported on the top two models, one of which has a B-axis tool post with optional ATC (automatic tool change) for tools up to 30 mm in diameter, chip-to-chip time being four seconds. Cutters are driven by a 2.2 kW motor at up to 12,000 rpm, so even small diameter mills are capable of productive metal removal rates. The additional programmable B-axis motion raises the total number of CNC axes to seven.
The Japanese manufacturer was the first to offer B-axis ATC on a sliding-head lathe to extend the machine’s versatility when executing angled cross working or end facing operations. The magazine accommodates 12 tools, while a 13th is fixed in the upper position on the live tool unit. While cutters are normally rotating for performing drilling, slitting, hobbing or multi-axis milling, either axially, radially or at a compound angle, magazine positions may be occupied by turning tools if expedient.
Another feature contributing to the lathe’s versatility is the ability to switch over quickly between Swiss-type operation and non-guide bush turning for more economical production of shorter components. This mode results in less bar wastage due to the shorter remnants and is well suited to coping with tight drawing tolerances and close bore-to-OD geometry. Removal of the guide bush also means that the diameter of the stock material does not have to be tightly controlled.
All lathe versions are supplied with the manufacturer’s programmable LFV function embedded in the operating system of the Windows-based Mitsubishi control, which is equipped with a 15-inch touch screen for easy visibility and intuitive operation. The three LFV modes of operation work at either spindle by oscillating the X and Z servo axes in synchrony with spindle rotation, breaking stringy swarf into short, manageable chips. It is especially effective when producing parts from malleable materials. The results are higher productivity by avoiding machine stoppages to clear away swarf manually, prevention of damage to the workpiece and/or tool, less tool wear and a better finish on the machined surface.
The number of turning tools that can be mounted on the gang tool post has been increased from five to six, so up to 45 tools may now be held in the machining area for enhanced machining capability. Citizen Machinery’s quick-change CIToolingSystem speeds tool exchange and improves repeatability of postioning to ±2 microns radially and longitudinally.
Access to the machining area has been improved, as the front door may now be fully opened and an extra door has been provided at the rear. Internally, units have been made as compact as possible and the coolant nozzles have been rearranged to improve efficiency during setup. Another improvement has been to upgrade the capability of the sub spindle, which is now rated at 3.7 kW / 10,000 rpm. Numerous robotic loading and unloading systems for automated storage and handling of raw material and finished workpieces are available.
Citizen Machinery’s Eco II suite of energy-saving features are incorporated, designed to optimise power consumption, reduce compressed air usage, minimise CO2 emissions and promote environmentally friendly manufacturing practices by allowing operators to monitor and understand energy utilisation patterns.
For example, an idling stop function puts the machine into standby when no programmed operation is in progress. The machine is equipped with intermittent air blow that maintains its effectiveness while reducing compressed air consumption by about 60%. Air purge control shuts off the function after a preset time while the machine is on standby to reduce air consumption further. A touchscreen Eco Monitor continuously displays in graphical form the power drawn and regenerated to ensure the lathe always runs at peak efficiency.
Citizen’s IoT-ready turning centres are compatible with its ‘alkapplysolution’ software, allowing them to be networked via a simple LAN connection. It enables users to take advantage of various software packages for tasks like NC program management and machine operation data monitoring. Specifically, ‘alkartlive 2’ software enhances production efficiency by visualising machine downtime and automatically aggregating data to reduce manual effort and enable preventive / predictive maintenance planning. The software displays machine status with colour-coded indicators on a timeline, alongside production results and alarm history, providing a clear overview of factory-wide operations.
Stay up to date with the latest industry news and events.
Be first to see all the updates from MTDCNC
Our newsletters frequency varies dependant on content
All the latest deals from the industry feature on our newsletters