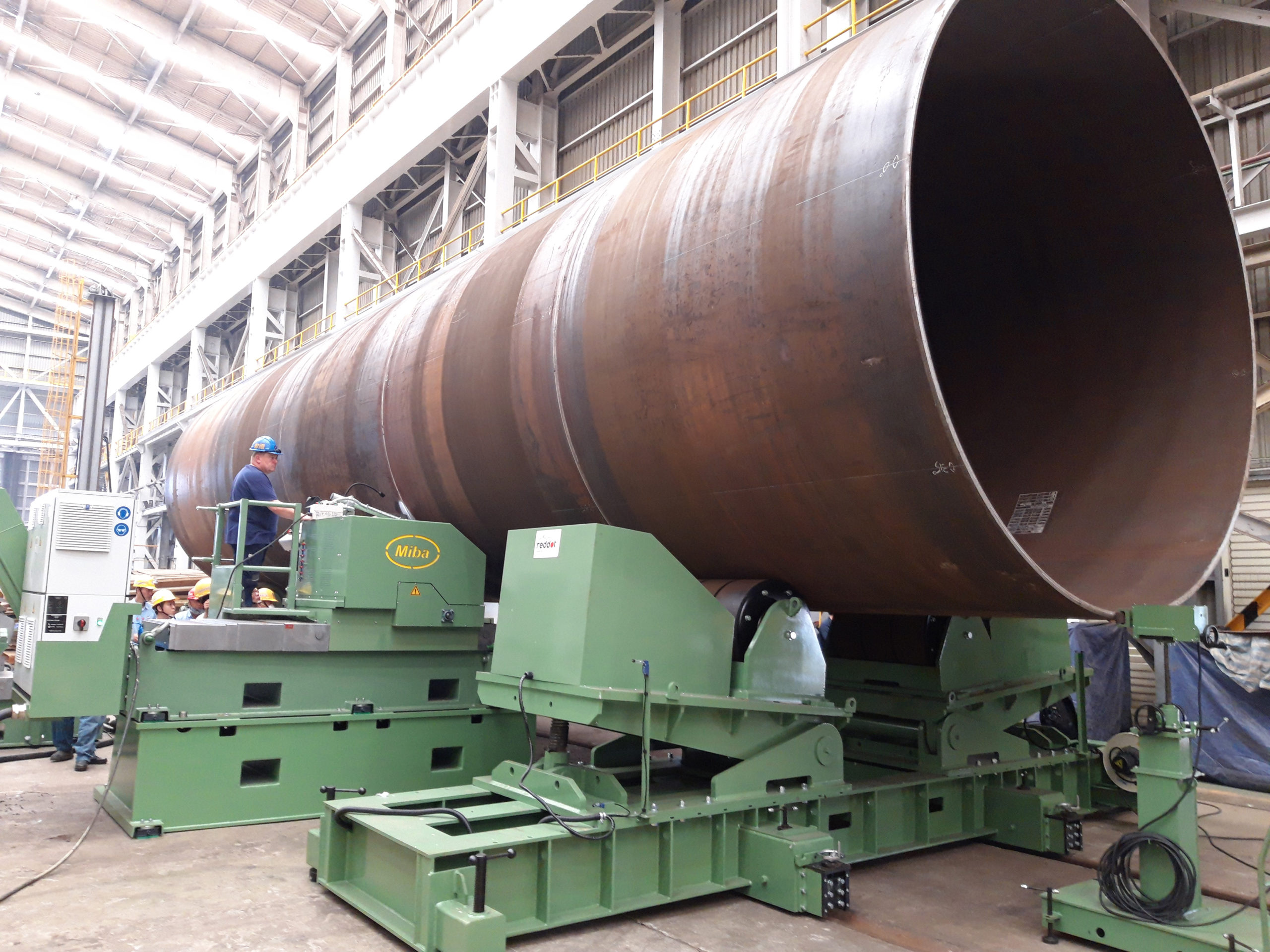
With the advances of 5-axis machining, twin spindle multi-axis turning and the like, machine tool technology has evolved to make ‘one-hit machining’ and efficient cycle time reductions the norm in industry. But what if you are manufacturing colossal components and structures such as wind turbines, offshore oil & gas projects, shipbuilding and submarines, nuclear projects or even infrastructure projects that demand significant pipework? RAM Engineering & Tooling Ltd now has a solution with its ‘Big 4’.4
For manufacturers of components of unfathomable size and weight, the production process is often restricted by the available technology and the logistics of moving large parts through the process chain. With the ‘Big 4’ from RAM Engineering, components and structures can now smoothly pass through the process chain to simplify and streamline production and assembly, reduce costs and deliver factory-wide efficiency. The wind turbine sector is witnessing exponential growth with climate change being an existential threat to humanity. Demonstrating how the ‘Big 4’ is revolutionising this sector, we take a look at the ‘end-to-end’ solution from RAM Engineering.
The ‘Big 4’ is a combined solution from RAM Engineering that encompasses technology from world-leading brands such as Linsinger, Haeusler, Urhan & Schwill and Miba to cover everything from edge-milling, rolling, gouging, welding and growing lines. The process chain applied in the wind turbine industry from the ‘Big 4’ essentially takes large plates through more than 20 processes that encompass everything from milling, jointing, roll forming, testing and much more.
Getting into the flow
In the case of wind turbines, a series of different sized steel plates are plasma or gas cut to unlimited, application specific, sizes before edge milling. Example of common wind tower plate: 4.2m x 18m x 0.15m. Linsinger has been successfully producing edge milling technology since the 1970’s and comfortably mills large plates with efficiency and speed. Large bed edge milling gantry-type machines are the newest generation (PFM Falcon), with magnetic clamping tables that utilise the Linsinger cutting tool product, consisting of a sandwich cutter head that is driven by a minimum 60kW+ high-powered spindle capable of edge milling over 150mm depths of cut, with the preferred profile and DoC factored, in a single pass. The sandwich cutter head incorporates a specialised form and Linsinger’s proven ‘thick chip technology’ for machining any required edge form whilst the integrated chip removal system evacuates swarf from the table to eradicate re-cutting and extend tool life. This single-pass process removes material that may be heat-affected by plasma cutting whilst also creating the weld preparation form.
Upon machining to the desired dimensions, the plates are transferred to a pre-fabrication plate jointing machine with a capacity of over 200 tonnes. With long seam welding beams on linear slides, the plate jointing can be rotated to add more welding lines with the potential to increase flexibility. Productivity can be enhanced with the facility to synchronise three or more welding machines simultaneously to automate the process. The welding lines utilise advanced multi-layered submerged-arc welding (SAW) heads and Lincoln Electric’s Power Wave AC/DC 1000SD inverter technology that drastically improves productivity and consistency.
Following the joining process, the plates are manipulated on a plate bending machine capable of facilitating very large diameters. With a roller table for fast loading, side support manipulators and precision laser checking for roundness tolerances, the Haeusler bending machines are available in a variety of options to suit the demands of the customer.
From the bending process, the tube structure is then ready for external weld seam requalification via a long seam milling machine that can rotate the part without a crane to ensure accurate positioning. The positional accuracy is guaranteed with an automatic tracing system and laser guiding that works in synergy with an easy clamping system and camera for automated production control. Once in position, the tube is machined with a specialist cutting wheel that machines a cone-shaped seam with depths up to around 120mm deep to prepare the part for subsequent welding.
Growing together
With the tube structure formed and seam milled, it is then transferred to the next station – the SAW triple arc welding process. The triple arc system has a deposition rate of 70kg/hour that is more than 80% faster at welding external diameters and 79% more efficient on internal diameters. This is a credit to a deposition rate that is 311% higher than tandem arc alternatives. This is once again credit to the Wave Form Control (WFC) of the Power Wave inverter technology, the multiple SAW process that can accommodate up to four long stick out effect arc welds simultaneously on one pipe section and the electrode feeding system. In synergy with electrode feeding is the continuous provision of a powder-protective shield for the arc weld process that permits exceptionally fast welding of deep cavities.
Having the facility to take large plates to complete structures for the wind turbine industry through the ‘Big 4’ solutions available from RAM Engineering & Tooling encompasses so much more than the cut, bend and weld. The edge-milling, rolling, gouging, welding and growing lines incorporate dedicated solutions that can measure, calibrate and even ultrasonically test at different stages – all with sheet handling and storage systems in the process to streamline the workflow.