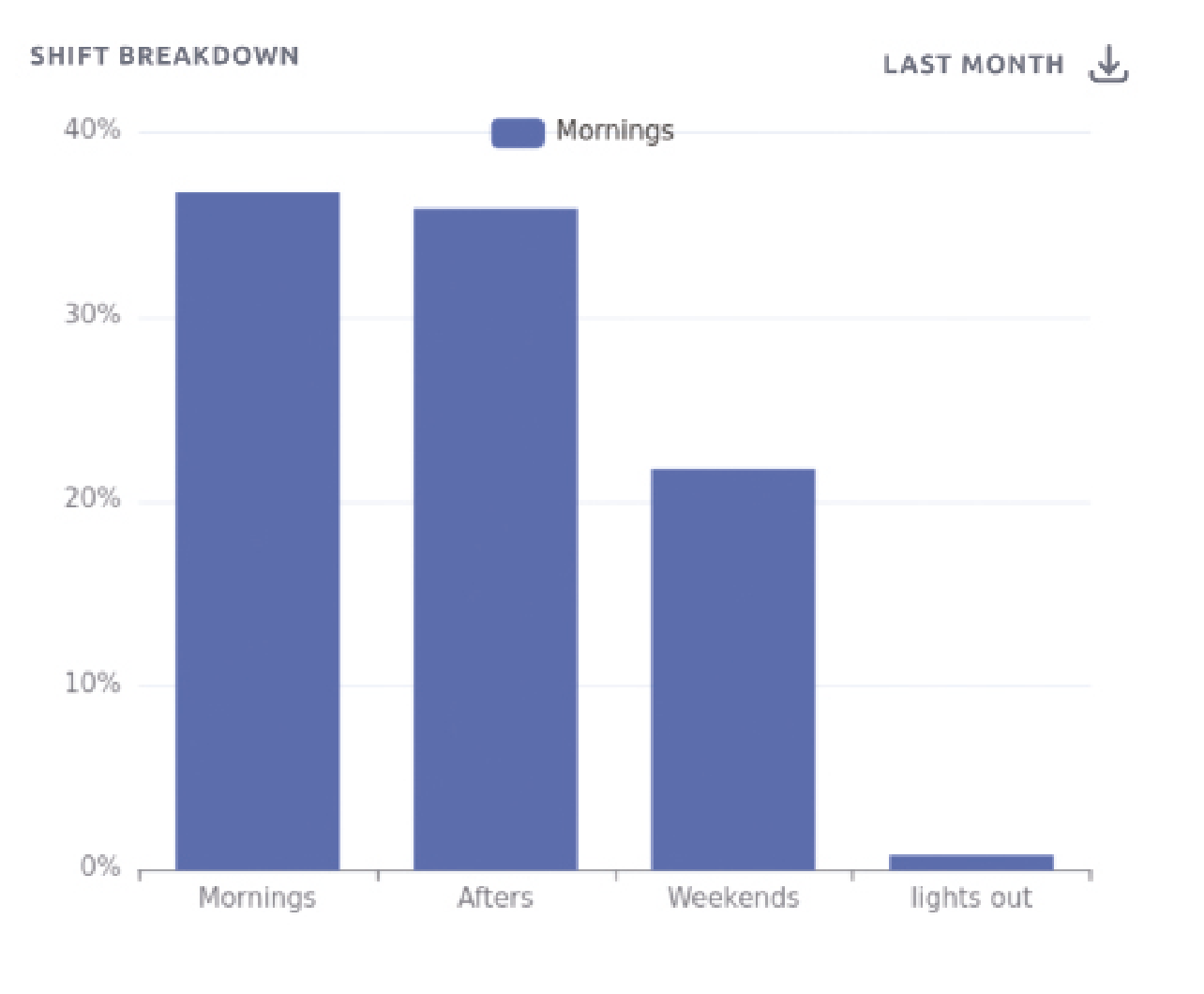
By MTDCNC’s Rowan Easter Robinson
Overall Equipment Effectiveness (OEE) is a measure often banded around by manufacturing management experts. It supposedly combines three metrics into one single measure that represents shop floor productivity. Like many simplifications, this doesn’t fully capture the major differences between manufacturing methods. For example, what works for a bottle-making facility won’t work for a CNC machine shop.
Firstly, what is OEE?
To break it into its most fundamental form, OEE identifies how much of your manufacturing time is actually productive. For example, an OEE score of 100% identifies that you are producing only good parts with no rejects, as fast as possible with no downtime – it’s the utopian dream. It means that your quality, performance and uptime are all at 100%.
When we measure OEE, we can gather insights on how to systematically enhance manufacturing processes. However, OEE is claimed to be the single best metric for benchmarking, identifying losses and improving productivity or eliminating waste – in my opinion, this is not strictly accurate.
So, how is OEE calculated?
OEE = Availability * Performance * Quality
Where:
Availability = Actual uptime/planned uptime
Performance = Actual cycle time/ideal cycle time
Quality = Good parts/total parts
Availability
Availability is really easy to calculate, either by hand or with machine monitoring. It is even shown as ‘pride of place’ in a dashboard on a TrackMyMachines dashboard that I work with.
Quality
Quality is again, easy to calculate. Once you’ve inspected your parts, you know the ‘good’ proportion. There are also statistical techniques you can use if you’ve got a large batch and only want to inspect a certain subset of them.
Performance – the potential misfit
Performance however is tricky. What is the best possible cycle time for a given part? It’s as low as possible – right? Well, if your only limiting factor is your cycle time, then it must be. There’s no machine shop I’ve seen whose limiting factor is only cycle time, this is for a myriad of reasons. A lower cycle time might increase tool wear and cost more over time. Or someone might not be available to change over a part if it’s finished too quickly. Sometimes if a machine has a longer cycle time, you can save on tool wear and an operator can run more machines. It’s a little more complicated than just reducing cycle times.
What is an ‘ideal’ cycle time anyway? If you’ve got a new part or manufacturing process, there is no way to know exactly how long it will take to produce. The job of estimating this cycle time is often left to an extremely experienced individual, whose best guess might still be out by a factor of 2 or more. So, the ‘performance’ portion of OEE isn’t really possible to calculate in many cases.
There’s another point to consider here too. If you have a long-running part that you set in the evening and leave to run overnight, you’re getting ‘free productivity’ regardless of what its cycle time is. It is these 3 factors that, in my opinion, can play a part in making the ‘performance’ measure not only less useful but potentially misleading and harmful to your efforts in increasing actual productivity.
Since this performance measure consists of one-third of your total OEE metric, if it’s wrong then using that metric as an indicator of productivity might be one-third wrong too.
Where did OEE come from?
Focusing on just a single OEE measure might not be able to capture all of this operational complexity. That’s probably because its origins were founded in specialist manufacturing plants with assembly lines – factories that make bottles, pharmaceuticals, cars, iPhones or any other mass-produced product. These factories make much larger volumes. CNC machine shops are quite literally at the opposite end of the spectrum, especially the shops that have a huge variation in their daily workload, often with small or differing batch sizes and component types.
Take a more nuanced approach
Instead, a less rigid approach is needed that considers the needs of the business and its engineering capabilities. Rather than just observing a simplistic metric, try to follow the manufacturing thread for a component or batch of components clocked into and out of each work order operation. Find out how much time that operation spent doing useful work (probing, cutting etc), semi-useful work (work setting, tool changing) and non-useful work (machine sitting idle). You might be surprised to find that during that 3-hour operation, the machine only spent 50 minutes doing useful work! Regardless of how your costs are calculated: either by person-hours, machine hours or a combination; There are savings to be made by investigating and improving this dead machine time.
It’s the closing of the loop between expected machining time and actual machining time that’s going to supercharge your growth as a business. Although this investigative work by hand is certainly possible, it really can be time-consuming. An automated machine monitoring system makes this information transparent and easy to build a clear picture of what is happening on your shop floor.