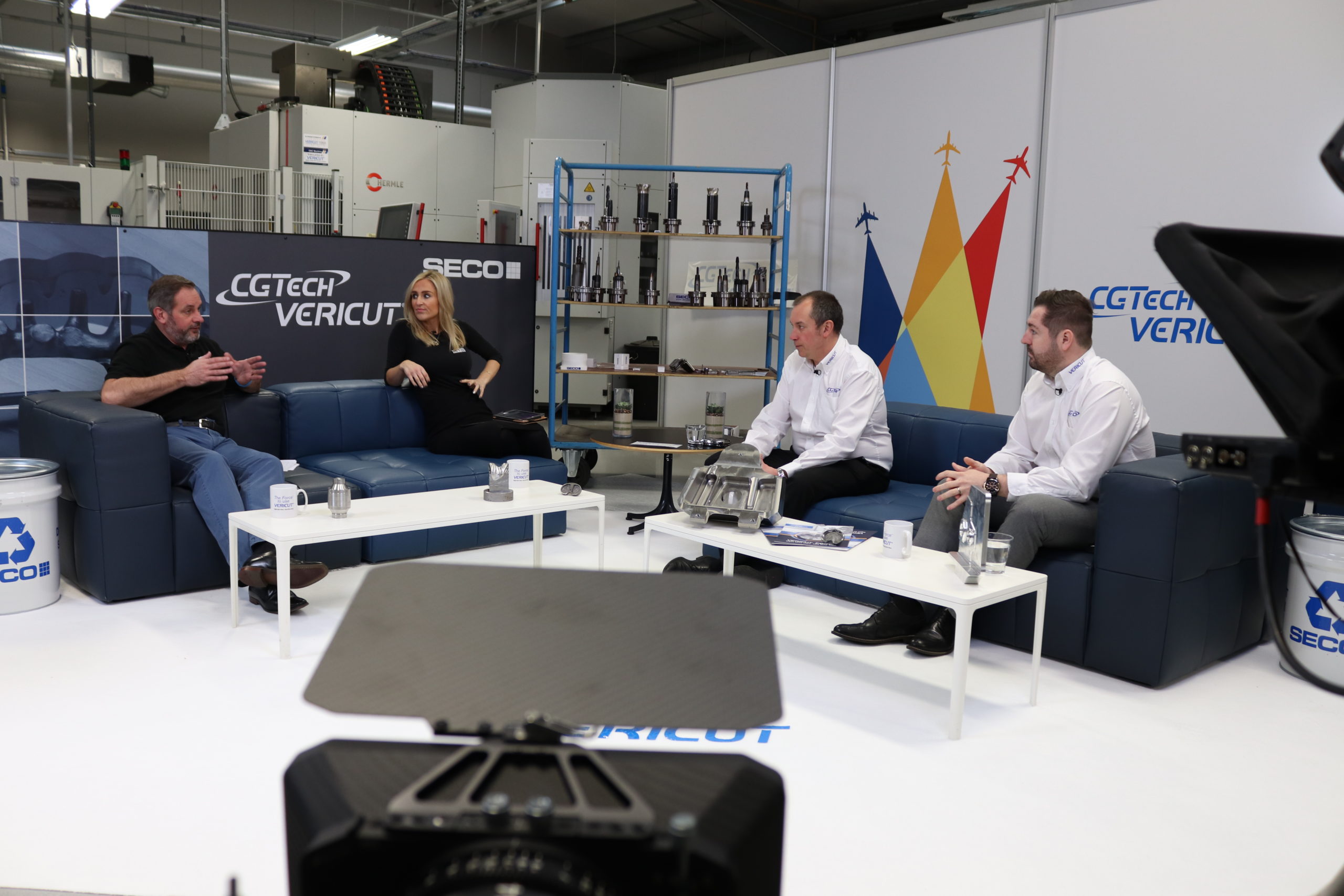
The MTDCNC team recently hosted a live event with NC verification and optimisation experts CGTech at the UK headquarters of technology partner Seco tools. MTD Magazine was on hand to pick up the key points and give our readers the highlights from this event.
Hosted by Lyndsey Vickers and Mark Deadman, the event showed MTDCNC viewers how the VERICUT Force module from CGTech optimises CNC programs and ultimately increases profit margins. The event provided demonstrations of real-world cutting applications of aerospace and medical components on machine tools using VERICUT, ultimately providing a real eye-opener for any manufacturers that want to make significant improvements to their bottom line. One of the key points of this event was to highlight the fact that regardless of whether you are using a high-quality CAM system utilising dynamic machining strategies at present, VERICUT Force can still optimise your system to create improvements.
Scott Ravenscroft the Sales Manager at CGTech kicked off the event by announcing a competition where the winner would win a 12-month subscription to the Force module – and if the winner was already a CGTech customer, they would win a free 12-month subscription to CGTech’s core product VERICUT as well as the Force module.
Following the announcement of a competition, Arran Radford Sales Engineer from CGTech initially gave an outline of what the system achieves. Saying: “VERICUT is the number one NC verification, simulation and collision detection software available. So, when we talk about optimising our profits, we have to start at the beginning. Any time spent at the machine with manual prove-out is costing you money, using a digital twin and NC verification system within VERICUT ensures that your process is safe, there are no collisions and it’s correct before it even enters the shop floor. From there, within VERICUT we can do manual inspection to compare cut stock models against design models. Ultimately, if your machine is idle or you are cutting a component that isn’t going to the customer, it is creating a cost to your business.”
“The technology has developed and evolved and with the digital twin, we take a digital model based on your actual machine, its kinematics and parameter file. This means that your machine acts exactly the same in the digital environment as it would in the real world. This gives us the power to fully simulate the process accurately. Now, there are a lot of other modules available in VERICUT as well, such as proving-out probing routines, grinding and wheel dressing and much more. It’s also important to remember that this is all accumulated in the machines true NC code, so it is reading the same language as the machine tool.”
When questioned about working with existing CAM systems from other vendors, Arran continued: “We work with pretty much all of the CAM systems that are available and we have interfaces that can seamlessly transfer data from virtually any CAM platform into VERICUT, but the key thing to remember is that we are simulating true data. On CAM systems, as good as the simulation may be, it is just simulating axis movements from point A to point B and predicting what the machine is theoretically going to do. VERICUT shows exactly how the machine reacts.”
With the key focus of the event being the Force module, Scott Ravenscroft explains: “VERICUT Force will take an existing NC program, analyse it and optimise it. When speaking to potential customers, I ask ‘how do you know your current process is truly optimised?’ One of the key objections we get when we are talking about Force, is that customers say they have a truly great CAM system. I am not knocking leading CAM systems, but it doesn’t matter how that code has been generated or which CAM system it has been generated from – the important thing is that we can take that NC code, analyse it, optimise it and make it more efficient. When we say more efficient, we mean we are going to give you cycle time reductions and tool life improvements. Force is available for turning, milling and complex machining applications – it is a truly multi-discipline package.”
To demonstrate the capabilities of VERICUT Force, the event looked at three demonstrations from a recent Seco Tools ITI aerospace event. The first demonstration part, an aluminium grade aerospace skin plate component was taken from a multi-operation process to one-hit machining, which required the implementation of ‘snap-off’ tabs when machining from a solid billet. Commenting on this, Arran says: “This process was already optimised, so where do you go from there? Seco approached us and asked if they could run it through Force to see what could be achieved. We are usually approached to look at harder material and this was an aluminium component, but we still managed to achieve a 17% cycle time reduction. Additionally, by maintaining a constant chip thickness within the program, we are removing high loads and poor cutting conditions, and we are working with the cutting tool manufacturers and their cutting tool data.”
Alluding to the technology behind the system, Scott says: “You think about how your parts are programmed, you are generally running with a flat feed rate with some small variation. When we analyse that strategy, very rarely do you get a constant chip thickness – it always varies. What we do, is flip that on its head. If a cutting tool manufacturer recommends a particular chip thickness, to maintain that we vary the feed rate motion in the NC programme to get what I refer to as ‘attack’. Then the ‘Force’ is where we want to limit deflection and poor cutting conditions, and that is where we get the tool life benefits. We used to justify the payback period of VERICUT to large aerospace companies on a single component. With smaller subcontract companies, this justification would have to be done over several components, but we ultimately yield a payback period of between two and six months with Force for subcontractors.”
The second component that was demonstrated at the event was a titanium pylon for the commercial aerospace sector. Scott says: “Heller and Seco got us involved in this component at the Seco ‘Inspiration Through Innovation’ event in 2020. We looked at the family of components in Force and we established there was definitely a saving there. Now, we have taken on the parts for the customer in conjunction with Seco and we are seeing phenomenal savings. We are saving 30% cycle time on roughing operations. On one pocket alone, we have reduced the dynamic milling cycle time by 50% – a lot of engineers will query how that is physically possible, but it is.”
Describing the third and final component, which created such a stir of interest during the event as it was the part discussed in the competition, Arran says: “The final part is a medical component, it is a tibial tray that is used in Total Knee Arthroplasty and is made out of 3D printed titanium. When we started speaking to Seco on this component, they provided the component, the tooling and the Hermle machining centre – we realised the part was going to be a challenge, as it was a small part. We didn’t think there was a huge saving to be made, but Seco soon informed us that there were somewhere between 600,000 and 700,000 of these parts to be made per year and per manufacturer. We have taken 15% out of this part and when you convert that into financial terms over the quantity of parts, it is more than £500,000 saving. Furthermore, the component is part of the set with a femoral mating part – if you can make a similar saving on the femoral part, that is a saving of well over £1 million per year.”
In fact, the tibial trays have a global market demand of around 5 million per year and Force reduced the cycle time on one feature by 15%. This may seem meagre compared to the 20% plus often attained by the software. However, with the large volumes required the benefits soon add up. If a machine shop is producing 600,000 per year at an hourly machine rate of £100 it equates to an annual saving of £724,000 or 301 days.
But what was the overall cycle time and what saving did VERICUT Force make? Well, the overall cycle time for the medical part was 7 minutes 25 seconds and this was reduced by 15% to 6 minutes 30 seconds with the implementation of VERICUT Force. The individual that guessed the correct answer was Dessie Diamond from Moyola Precision Engineering and they have won a 12 month subscription to the Force module, including training.
Discussing the relationship from a Seco perspective, Dave Magnall from Seco Tools says: “We have changed our business model to ‘innovation hub’ where we now look at full process improvement for our customers. This is where the relationship really starts to pay off, the Force software is a fantastic piece of process optimisation software. We are under a lot of pressure from a lot of our customers, such as big high-end aerospace customers that want to improve their processes and productivity, not just incrementally but by large amounts.”
“We can attain incremental improvements with just the cutting tool, but to achieve the 40 to 50% improvement that customers are demanding, we need to make some major gains – and with CGTech on some of these large difficult material aerospace components or high-volume parts, we can achieve these major gains from using the Force software. Protecting the tool is also an important element. Force is a real win-win for us, as we can get stuck in that trade-off between increasing cutting speeds and creating a detriment to tool life or achieving process stability. Force looks at those peaks and troughs and evens them out, so we get a kind process that reduces the spindle load, provides a much kinder cutting process that reduces spindle load and vibration, and it gives us much higher productivity with a much kinder process.”